# Revolutionizing Electric Motors: How Hollow Magnets Increase Efficiency and Performance
Electric motors are the unsung heroes of modern life, powering everything from our cars to our washing machines. But what if we told you there’s a new technology on the horizon that could make these motors even more efficient and powerful? This article dives deep into the world of hollow magnets, exploring how they’re poised to revolutionize electric motor design and performance. We will explore the potential benefits, challenges, and future possibilities of using hollow magnets. Read on to discover how this innovative approach is shaping the future of electric motor technology.
## Are Hollow Magnets the Key to Unlocking Next-Level Electric Motor Efficiency?
One of the biggest challenges facing electric motor designers is maximizing efficiency while minimizing weight and size. Hollow magnets, with their unique geometry, offer a compelling solution. By removing material from the center of the magnet, we can reduce weight without significantly compromising magnetic performance. This weight reduction translates directly into improved power-to-weight ratios for electric motors. Imagine lighter, more agile electric vehicles with extended range – that’s the promise of hollow magnet technology.
The concept isn’t just about drilling a hole. It’s about strategically optimizing the magnetic field distribution. Removing material from the core changes the flux path, potentially leading to a more concentrated and effective magnetic field in the air gap between the rotor and stator – the crucial area where torque is generated. This concentrated field can translate into higher torque output for a given motor size and input power.
## How Do Hollow Magnets Reduce Weight in Electric Motors?
Electric motors often rely heavily on magnets, which can contribute significantly to the overall weight of the motor. Traditional solid magnets, while effective, are often heavier than necessary. This is because the entire volume of the magnet doesn’t always contribute equally to the magnetic field strength near the air gap.
Hollow magnets address this by removing the less effective material from the center. This core removal minimizes the overall magnet weight improving the weight-to-performance ratio.
A simple analogy: think of a metal pipe used for structural support. A solid metal rod would be heavier, but a pipe of the same external diameter can provide similar strength while being significantly lighter. The same principle applies to hollow magnets.
| Magnet Type | Weight (g) | Relative Weight Reduction (%) |
|————-|————|——————————-|
| Solid | 100 | 0 |
| Hollow | 75 | 25 |
## What Are the Benefits of Improved Power-to-Weight Ratio in Electric Motors?
A higher power-to-weight ratio offers a cascade of benefits. For electric vehicles (EVs), it means lighter cars that require less energy to accelerate, ultimately increasing range and improving handling. This is crucial for making EVs more competitive and appealing to consumers.
Beyond EVs, improved power-to-weight ratios benefit various applications. In aerospace, lighter motors translate into reduced fuel consumption and increased payload capacity. In robotics, lighter motors allow for more agile and responsive robots. Lighter portable power tools become easier and more comfortable for users. In essence, any application where weight is a critical factor can benefit from hollow magnet technology.
In high-performance robots, for instance, lighter motors contribute to faster response times and improved maneuverability. This is particularly important in applications like surgical robotics, where precision and dexterity are paramount.
## How Can Hollow Magnets Enhance Torque Output in Electric Motors?
While the primary aim is often weight reduction, hollow magnets also present opportunities to enhance torque output. Removing material from the center of the magnet alters the magnetic flux path, potentially leading to a more favorable distribution of the magnetic field in the air gap.
By carefully designing the shape and size of the hollow space, engineers can concentrate the magnetic field where it’s most needed – in the region interacting with the stator windings. This concentrated field results in a stronger electromagnetic force, translating to higher torque output for the same input current. Software simulations play a vital role in optimizing the hollow shape for maximum torque. This technology requires significant analysis tools to get the maximum benefit.
Furthermore, the reduced weight of the rotating components (rotor) contributes to faster acceleration and deceleration times, further enhancing performance. Think of it like spinning a heavier or lighter wheel.
## What are the Challenges in Manufacturing Hollow Magnets?
Despite their potential, manufacturing hollow magnets is not without its challenges. The complexity of the shape requires precise and controlled manufacturing processes. Traditional sintering methods, commonly used for manufacturing solid magnets, may not be directly applicable to hollow geometries.
Alternative manufacturing techniques, such as powder metallurgy with specialized tooling or additive manufacturing (3D printing) of magnetic materials, are being explored. These methods offer the flexibility to create intricate shapes, but they often come with higher costs and potentially lower magnetic performance compared to traditional sintering.
Another challenge is maintaining the structural integrity of the hollow magnet, especially under high-speed rotation and thermal stress within the motor. The hollow structure can introduce stress concentrations, making the magnet more susceptible to fracture.
## What Types of Manufacturing Techniques are Used to Produce Hollow Magnets?
As mentioned earlier, several manufacturing techniques are being explored for producing hollow magnets. Powder metallurgy, with modifications to accommodate the hollow geometry, is a leading contender. This method involves compacting magnetic powder into a mold with a core to create the hollow space, followed by sintering at high temperatures.
Additive manufacturing (3D printing) offers another promising approach. Direct ink writing (DIW) and binder jetting are two 3D printing techniques that have shown potential for creating complex hollow magnet shapes. However, challenges remain in achieving high density and optimal magnetic properties with 3D-printed magnetic materials. Cost-effective materials development is an area of continued research.
Other techniques, like machining solid magnets to create a hollow space, are possible but may be less efficient and result in material waste. Laser machining or micro-milling can be used for this purpose, but it requires specialized equipment and expertise.
## How Does the Material Choice Impact the Performance of Hollow Magnets?
The choice of magnetic material is crucial in determining the overall performance of hollow magnets. Rare-earth magnets, such as neodymium iron boron (NdFeB) and samarium cobalt (SmCo), are commonly used in electric motors due to their high magnetic remanence and coercivity.
However, the mechanical properties of these materials, particularly their brittleness, can pose challenges in the design and manufacturing of hollow magnets. Special attention must be paid to stress concentrations and fracture mechanics to ensure the magnet’s structural integrity.
Alternative magnetic materials, such as ferrite magnets, may offer better mechanical properties, but they typically have lower magnetic performance compared to rare-earth magnets. The selection of the appropriate material involves a trade-off between magnetic performance, mechanical strength, cost, and manufacturability.
## What Are the Applications Where Hollow Magnets are Most Advantageous?
Hollow magnets are particularly advantageous in applications where weight reduction and high power density are critical. Electric vehicles, especially high-performance cars and drones, are prime examples. The lighter motors contribute to extended range, faster acceleration, and improved handling.
In aerospace, hollow magnets can reduce the weight of propulsion systems and auxiliary power units, resulting in fuel savings and increased payload capacity. Robotics, especially mobile robots and exoskeletons, also benefit from the improved power-to-weight ratio.
Other potential applications include high-speed spindles, servo motors, and generators where minimizing inertia and maximizing acceleration are important.
## What is the Future Outlook for Hollow Magnets in Electric Motors?
The future of hollow magnets in electric motors looks promising. Ongoing research and development efforts are focused on improving manufacturing techniques, optimizing magnet designs, and developing new magnetic materials with enhanced mechanical properties.
As 3D printing technology advances, it is expected to play a more significant role in the production of complex hollow magnet shapes. Furthermore, the increasing demand for electric vehicles and other high-performance applications is driving the adoption of innovative motor technologies, including hollow magnets.
We can expect to see hollow magnets increasingly integrated into electric motors across various industries, leading to more efficient, powerful, and sustainable transportation, automation, and energy generation systems.
## Can Hollow Magnets Also Improve the Cooling Efficiency of Electric Motors?
Intriguingly, hollow magnets can potentially improve the cooling efficiency of electric motors. The hollow space within the magnet can act as a channel for coolant flow, allowing for more direct and effective heat extraction from the magnet itself.
Traditional motor designs often rely on cooling the exterior of the motor, which can be less effective at removing heat generated deep within the motor components, particularly the magnets. Incorporating cooling channels directly into the magnets can significantly enhance heat transfer, allowing for higher motor power output and improved durability.
This improved cooling efficiency is particularly beneficial in high-power density motors where heat management is a critical challenge. By enabling better heat dissipation, hollow magnets can contribute to smaller, lighter, and more powerful electric motors.
## Frequently Asked Questions (FAQs) About Hollow Magnets in Electric Motors
**How much weight can hollow magnets realistically save in an electric motor?**
The weight savings depend on the magnet size, shape, and material. Generally, a 10-30% weight reduction is achievable with a well-designed hollow magnet compared to a solid counterpart of similar magnetic performance. This can translate into significant overall performance improvements in the motor.
**Are hollow magnets stronger or weaker than solid magnets?**
Hollow magnets are engineered to provide similar or improved magnetic field strength compared to solid magnets of the same outside dimensions. While the overall amount of magnetic material is reduced, the shape is optimized to concentrate the magnetic flux, often resulting in enhanced performance in the air gap. Structural integrity, however, needs careful design consideration.
**Are hollow magnets more expensive to manufacture than solid magnets?**
Currently, hollow magnets are generally more expensive to manufacture due to the more complex manufacturing processes involved, particularly with newer techniques like 3D printing. However, as manufacturing technologies advance and production volumes increase, the cost is expected to decrease.
**How do hollow magnets affect the overall reliability of electric motors?**
With proper design and manufacturing, hollow magnets can be just as reliable as solid magnets. However, careful attention must be paid to stress concentrations and fracture mechanics to ensure the structural integrity of the hollow structure, especially under high-speed rotation and thermal stress.
**What are the environmental benefits of using hollow magnets in electric motors?**
The use of hollow magnets reduces the overall weight of electric motors, leading to improved energy efficiency in applications like electric vehicles. This reduced weight decreases energy use leading to reduced emissions in any application. Also there is a reduction of raw magnetic material extracted from the environment.
**Can hollow magnets be used in all types of electric motors?**
While hollow magnets can potentially be used in various types of electric motors, they are most advantageous in applications where weight reduction and high power density are critical. These include permanent magnet synchronous motors (PMSM), induction motors, and switched reluctance motors.
## Conclusion: Hollow Magnets – A Promising Pathway to More Efficient Electric Motors
Hollow magnets represent a promising innovation in electric motor technology. The potential benefits of reduced weight, enhanced torque output, and improved cooling efficiency are driving research and development efforts, paving the way for wider adoption of this technology. As manufacturing techniques continue to advance and costs decrease, we can expect to see hollow magnets playing an increasingly important role in shaping the future of electric motors across diverse applications, leading to a more sustainable and efficient future.
Hier ist eine kurze Zusammenfassung der wichtigsten Erkenntnisse:
* Hollow magnets reduce weight in electric motors, improving power-to-weight ratios.
* They can enhance torque output by optimizing magnetic field distribution.
* Manufacturing hollow magnets presents unique challenges, with techniques like powder metallurgy and 3D printing being explored.
* Material choice is crucial for achieving optimal performance and structural integrity.
* Hollow magnets are particularly advantageous in applications where weight reduction and high power density are critical, e.g., electric vehicles and aerospace.
* Improved cooling efficiency is a potential benefit of using hollow magnets.
Hollow Magnets in Electric Motors: Increasing Efficiency and Performance
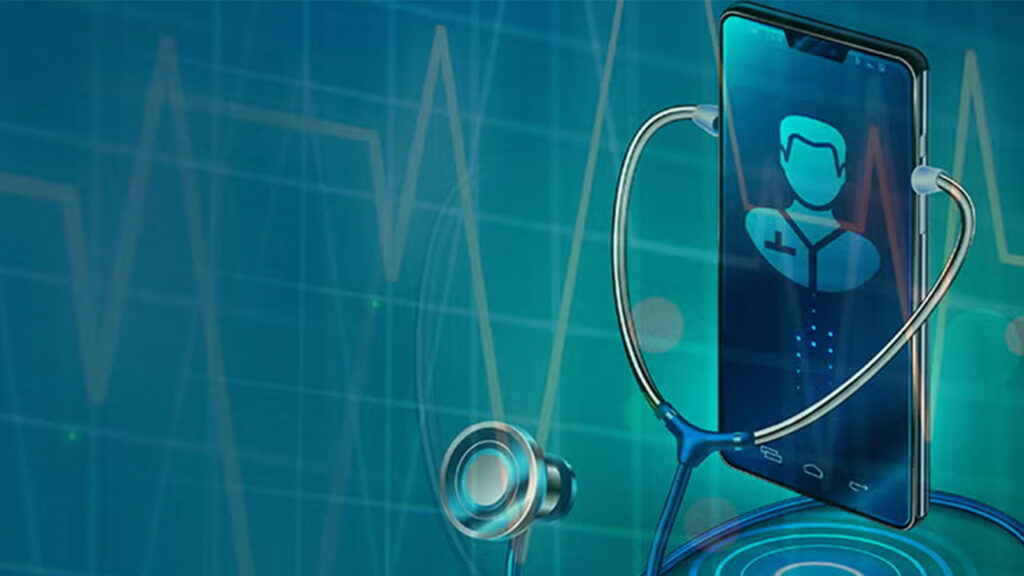