# Stuck on Magnets? Choosing the Right Adhesive for Your Magnet Application
Have you ever struggled to find the perfect glue for your magnet project? From fridge magnets to industrial applications, a strong bond is crucial. This article is your comprehensive guide to selecting the best adhesive. We’ll explore various adhesive types, surface preparation techniques, environmental considerations, and application methods to ensure your magnets stay put. You’ll discover the secrets to achieving a long-lasting, reliable bond, no matter the project.
## 1. What are the Key Considerations When Choosing an Adhesive for Magnets?
Selecting an adhesive for magnets isn’t as simple as grabbing the first glue you see. Many factors influence the success of your project. Strength, temperature resistance, and the materials being bonded are paramount. It is essential to contemplate the type of magnet you are looking to affix (neodymium, ferrite, alnico, etc.) and the composition of the surface that it will be paired with. Consider that magnets attract metals, so some adhesives that may be designed for use with metals could be a good pairing.
Think about the environment your magnet will be exposed to. Will it endure high temperatures, humidity, or chemical exposure? Also, the application method matters. Do you need a fast-setting glue or one that allows for adjustments? Finally, examine the shear strength you require; that’s the force needed to slide the magnet off the surface. Ignoring these variables only makes the outcome less predictable. I learned this lesson the hard way on a craft project using super glue on a ceramic magnet that broke a couple of days later.
## 2. Which Adhesive Types Offer the Best Bonding Performance for Magnets to Different Surfaces?
Navigating the adhesive landscape can be daunting, but understanding the strengths of each type is key. Epoxies are renowned for their exceptional strength and durability, making them ideal for demanding applications. Cyanoacrylates (super glues) provide a rapid bond, great for quick fixes, but might lack long-term resilience in certain conditions. Acrylic adhesives offer a balance of strength and flexibility, while polyurethane adhesives offer excellent adhesion to porous surfaces.
Silicone adhesives are resistant to high temperatures and chemical exposure, perfect in harsh environments. Hot melt adhesives are cost-effective and easy to use; however, their strength and temperature resistance may be limited. Pressure-sensitive adhesives (PSAs), like double-sided tape, are convenient for temporary bonds. Ultimately, the ‘best’ adhesive depends on your specific materials and conditions.
Here’s a quick comparison in table form:
| Adhesive Type | Strength | Temperature Resistance | Best For | Drawbacks |
|——————-|——————-|———————–|———————————————-|———————————————|
| Epoxy | Excellent | Excellent | Heavy-duty applications, dissimilar materials | Can be brittle, requires mixing |
| Cyanoacrylate | High | Low-Medium | Quick fixes, small areas | Brittle, poor impact resistance |
| Acrylic | Medium-High | Medium-High | General-purpose, plastics, metals | May require surface preparation |
| Polyurethane | Medium-High | Medium-High | Porous surfaces, wood, fabrics | Can be messy, may require curing |
| Silicone | Medium | Excellent | High temperatures, weather resistance | Lower strength, slow curing |
| Hot Melt | Low-Medium | Low | Crafts, packaging | Low strength, poor temperature resistance |
| Pressure Sensitive | Low-Medium | Low-Medium | Temporary bonds, mounting | Limited strength, affected by temperature |
## 3. How Does Surface Preparation Impact Adhesive Bonding with Magnets?
Surface preparation is the unsung hero of adhesive bonding. A clean, properly prepared surface ensures maximum adhesion. Contaminants like grease, oil, and dust weaken the bond. Start by cleaning surfaces with a solvent like isopropyl alcohol or acetone. (Be careful about using strong solvents on plastics, test first to avoid damaging the surface). For metal surfaces, consider sanding or abrasion to create a rougher texture. This increases the surface area for the adhesive to grip onto.
Ensure the surfaces are dry before applying the adhesive. Primers can also enhance adhesion, particularly on difficult-to-bond materials like plastics. Remember, even the best adhesive will fail if the surface is poorly prepared. I used to think surface prep was overkill, but the durability of my projects improved dramatically when I started prioritizing it.
## 4. What Role Does Temperature Play When Selecting an Adhesive for a Magnet?
Temperature plays a crucial role in adhesive performance. High temperatures can weaken or even melt some adhesives, while low temperatures can make others brittle and inflexible. Before choosing an adhesive, consider the temperature range your magnet will be exposed to. Look for adhesives with a high glass transition temperature (Tg), which is the temperature at which the adhesive transitions from a rigid to a rubbery state.
Silicone and epoxy adhesives generally offer good temperature resistance. Hot melt adhesives, on the other hand, are less suitable for high-temperature applications. Always check the manufacturer’s specifications for the recommended temperature range. Also, consider thermal expansion of the materials you are gluing to. The difference in expansion rates could stress the adhesive.
## 5. Are there any Special Considerations for Bonding Different Types of Magnets (Neodymium, Ferrite, Alnico)?
Different magnet compositions have varied surface characteristics and expansion rates, which means you’ll need to be considerate when choosing your adhesive. Neodymium magnets, for instance, are sensitive to moisture and often have protective coatings. Cyanoacrylate adhesives should be used cautiously with these magnets, as they can attack certain coatings.
Ferrite magnets, being more porous, require adhesives that can penetrate and bond effectively. Epoxy resins and special acrylic adhesives are good choices. Alnico magnets, known for their high-temperature performance, need durable adhesives capable of enduring extreme conditions.
| Magnet Type | Surface Characteristics | Adhesive Considerations |
|—|—|—|
| Neodymium | Often coated to prevent corrosion | Avoid adhesives that might damage the coating (certain cyanoacrylates) |
| Ferrite | Porous | Use adhesives that can penetrate and bond to porous surfaces (epoxies, acrylics) |
| Alnico | High temperature resistance | Choose high temperature adhesives |
## 6. How Do I Choose the Right Adhesive Viscosity and Application Method?
Viscosity, or the thickness of the adhesive, affects its application and bonding performance. Low-viscosity adhesives are runny which are great for penetrating small gaps. High-viscosity adhesives resist sagging and are suitable for vertical surfaces. The application method also impacts adhesive selection. Manual dispensing is suitable for small projects, while automated dispensing systems are more efficient for high-volume production.
Consider the size and shape of the magnet and the substrate. Syringes, brushes, and dispensing guns are common application tools. Ensure proper ventilation during application, especially with solvent-based adhesives. Choosing the right application method will reduce waste and enhance bond consistency.
## 7. What Environmental Conditions Impact Adhesive Performance During the Application and Curing Process?
Environmental conditions such as humidity, temperature, and UV exposure heavily influenced by the adhesive’s curing procedure and performance. High humidity can interfere with the curing of certain adhesives, while very dry environments can cause fast solvent evaporation. Control temperature and relative humidity within recommended parameters to insure successful cures.
UV radiation can break down specific adhesives with time. If your assignment is exposed to sunlight, you need to pick an adhesive that is UV-resistant. Proper ventilation is vital when working, for example, with solvent-based adhesives to protect your health and ensure proper venting of fumes. These controls ultimately lead to a stronger and longer-enduring bond.
## 8. Case Study: Selecting an Adhesive for an Outdoor Magnetic Sign
Let’s illustrate adhesive selection with a real-world example: creating a magnetic sign for outdoor use. The sign is made of a thin aluminum sheet and attached to a vehicle using strong neodymium magnets. Given the outdoor environment, we need an adhesive that resists water, UV radiation, and temperature fluctuations.
Epoxy adhesives are a excellent choice due to their outstanding strength and weather resistance. Surface preparation is crucial. The aluminum sheet should be thoroughly cleaned and scuffed before applying the epoxy. A two-part epoxy formulation can provide additional resistance to the tough environmental conditions. The selected application method includes even and cautious distribution over the surface to make sure that the maximum bond and holding strength are achieved.
This case study highlights how considering environmental factors and material compatibility leads to the best choice when using adhesives.
## 9. What are Common Mistakes to Avoid When Bonding Magnets with Adhesives?
Bonding magnets with the correct adhesive could still fail if common mistakes are made. First and foremost, do not overestimate surface preparation. Neglecting to clean and scuff surfaces can result in poor adhesion. Secondly, using the wrong adhesive for the intended environment or materials can lead to bond failure.
Another mistake is over- or underapplying the adhesive. Always follow the manufacturer’s recommendations. Avoid using expired adhesives, as their properties may have deteriorated. Insufficient curing time is also a culprit. Allow the adhesive to cure fully before subjecting the bond to stress. Avoid rushing the process.
## 10. Where Can I Find Additional Resources and Expert Advice on Adhesive Selection for Magnet Applications?
Choosing the perfect adhesive can be a challenge. Luckily, plenty of resources are available. Consult with adhesive manufacturers and suppliers. They can provide technical data sheets and application guidelines. Online forums and industry websites often have user reviews and discussions on specific adhesives. Look for case studies and application notes related to magnet bonding. Local specialized adhesive distributors often possess staff that are knowledgeable about choosing the right adhesive for a specific application.
Universities and research institutions conduct studies on adhesive performance. Leverage these resources to make informed decisions. Seek advice from experienced engineers or technicians with expertise in adhesive bonding. I’ve found that talking to experts and researching online has saved me time and money in the long run.
## Häufig gestellte Fragen
**What adhesive do I use for gluing a magnet to plastic?**
For gluing a magnet to plastic, epoxy adhesives, acrylic adhesives and cyanoacrylates (super glues) are a good option. Ensure the surfaces are clean and you may need to lightly sand smooth plastics to get a better bond. Always test in a small, inconspicuous area first. This will help ensure that the glue is effective for the specific types of materials used in the process and that it wont break down the materials you are combining.
**Why did my strong magnet fall off the adhesive even though it was supposed to be strong?**
Numerous factors can cause a magnet to fall off, even with a strong adhesive. These include improper surface preparation, using the wrong adhesive (e.g., not suitable for the materials being bonded), temperature extremes affecting the adhesive, and insufficient curing time. Shear forces or impact on the magnet might exceed the adhesive’s strength.
**What kind of glue is waterproof for attaching magnets?**
For a waterproof bond when attaching magnets, consider using epoxy adhesives or polyurethane adhesives. Silicone sealants also offer good water resistance. Ensure proper surface preparation and follow the manufacturer’s instructions for application and curing to achieve a durable, waterproof seal.
**Is it okay to use hot glue to stick magnets?**
Hot glue works well for craft project but the holding power and long term results could be questionable. Hot glue is not as strong as many other adhesives and can fail when exposed to temperature variations, high stress or moisture. So, it’s not recommended for something permanent where structural integrity is required.
**What is the best adhesive for magnets exposed to high heat?**
For magnets that will be exposed to high heat, you’ll need an adhesive specifically designed for high-temperature applications. Silicone adhesives, epoxy adhesives with high-temperature resistance, and ceramic adhesives are your best bets.
**How long does it take for an adhesive to cure for a magnet application?**
Cure times vary depending on the type of adhesive. Cyanoacrylates (super glues) can cure in seconds, while epoxies may require several hours or even days for a full cure. Always consult the manufacturer’s instructions for specific curing times and conditions.
## Schlussfolgerung
* **Surface Prep is Key:** Cleaning, scuffing, and priming ensures optimal bonding.
* **Adhesive Choice Matters:** Select the right adhesive based on materials, environment, and application.
* **Temperature Considerations:** High and low temperatures can affect adhesive performance.
* **Application Method:** Correct tools and techniques reduce waste and ensure consistent bonds.
* **Avoid Common Mistakes:** Follow instructions, ensure proper curing, and use fresh adhesives.
* **Seek Expert Advice:** Consult with manufacturers and experienced professionals.
Die Wahl des richtigen Klebstoffs für Ihre Magnetanwendung
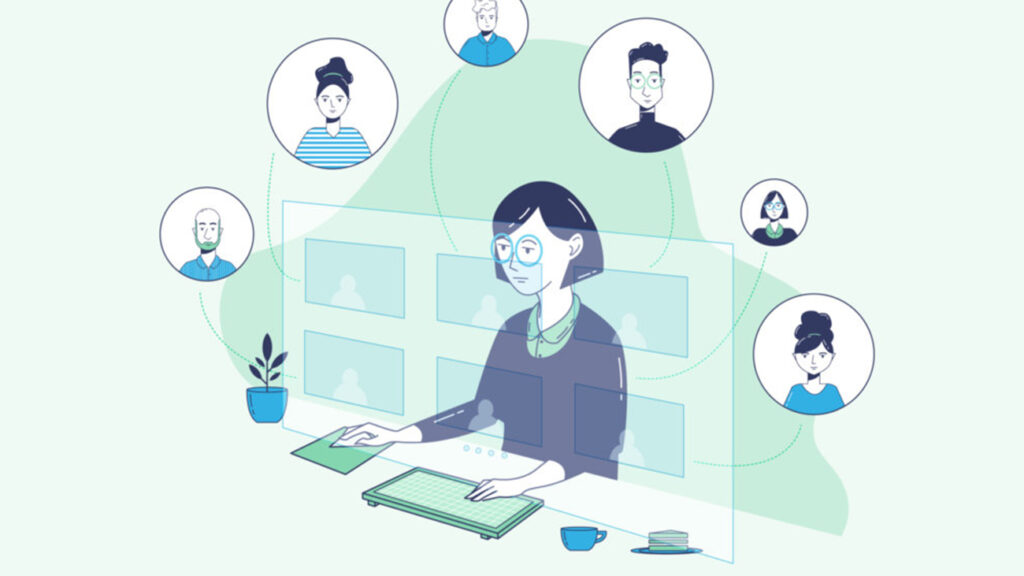