# Unlocking Performance: Finite Element Analysis (FEA) in Magnet Heavy Actuator Design
Finite Element Analysis (FEA) has become an indispensable tool in the design and optimization of magnet heavy actuators. This article explores how FEA helps engineers predict and improve actuator performance by simulating complex electromagnetic, thermal, and mechanical behaviors. We’ll delve into the key challenges, benefits, and practical applications of FEA in this specialized field, providing you with a valuable understanding of how to leverage simulation for superior actuator designs. This article will guide you through relevant challenges and solutions for designing high-performance actuators and is valuable to anyone interested in actuator design, simulation, or engineering innovation.
## Why is FEA Essential for Magnet Heavy Actuator Design?
Magnet heavy actuators, as the name suggests, rely heavily on magnets to generate force and motion. These actuators are used in various applications, including robotics, automotive systems, and medical devices. However, their design can be complex due to the strong electromagnetic fields involved and the interplay between different physical phenomena. FEA provides a virtual environment to analyze these complexities without the need for costly physical prototypes.
Using FEA early in the design phase allows engineers to identify and address potential issues before manufacturing, saving time and resources. I recall a project where we used FEA to refine the magnet arrangement within an actuator, resulting in a 20% improvement in force output. Without FEA, achieving this optimization would have been incredibly challenging and time-consuming.
## How Does FEA Simulate Magnetic Fields in Actuators?
FEA software employs numerical techniques to solve Maxwell’s equations, which govern electromagnetic phenomena. These equations describe how electric and magnetic fields interact and how they are affected by currents and materials. By defining the geometry of the actuator, the magnetic properties of the materials (such as remanence and permeability), and any applied currents, FEA can calculate the magnetic field distribution within the actuator.
The simulation results reveal crucial information like:
* **Magnetic flux density:** A measure of the strength and direction of the magnetic field.
* **Magnetic force:** The interaction between magnetic fields and current-carrying conductors or other magnets.
* **Eddy current losses:** Energy dissipated as heat due to alternating magnetic fields inducing currents in conductive materials.
This information helps designers optimize the magnet arrangement, coil design, and overall geometry to maximize force, minimize losses, and improve efficiency. It’s like having a virtual magnifying glass that allows me to ‘see’ the invisible forces at play within the actuator.
## What Types of Physical Phenomena Can FEA Model in Magnet Heavy Actuators?
FEA can simulate not only magnetic fields but also other critical physical phenomena that affect actuator performance. These include:
* **Thermal analysis:** Simulates heat generation due to eddy currents, Joule heating (resistance heating in coils), and other sources. It predicts temperature distribution, which is crucial for managing component temperatures and preventing demagnetization of magnets.
* **Structural analysis:** Evaluates the mechanical stresses and strains caused by magnetic forces and thermal expansion. It ensures the structural integrity of the actuator and prevents failures due to excessive loads.
* **Fluid dynamics (if applicable):** Simulates the flow of cooling fluids, allowing engineers to optimize cooling strategies and maintain performance within safe operating temperatures.
Furthermore, FEA can couple these different physics together. For example, you can perform a coupled electromagnetic-thermal analysis where the heat generated by eddy currents (calculated electromagnetically) is used as input for the thermal analysis. This provides a more realistic and accurate simulation of actuator behavior.
## How Does Material Selection Impact FEA Simulation Results?
The accuracy of FEA simulations heavily depends on the accuracy of the material properties used as input. For magnet heavy actuators, crucial material properties include:
* **Magnetic properties:** Remanence (residual magnetization), coercivity (resistance to demagnetization), permeability (ability to conduct magnetic flux), and BH curves (relationship between magnetic field strength and magnetic flux density) for magnets and core materials.
* **Thermal properties:** Thermal conductivity, specific heat capacity, and thermal expansion coefficient for all components.
* **Mechanical properties:** Young’s modulus, Poisson’s ratio, yield strength, and ultimate tensile strength for structural components.
Selecting accurate material properties from datasheets or experimental measurements is crucial. Using incorrect material data can lead to inaccurate simulation results and poor actuator performance. I once experienced a situation where using inaccurate BH curves for a magnet led to a significant underestimation of the actuator’s force output in the simulation. This highlights the importance of rigorous material characterization.
## What Are the Common Challenges in FEA Modeling of These Actuators?
While FEA offers significant advantages, it also presents several challenges:
* **Computational cost:** Simulating complex 3D geometries with fine meshes can be computationally expensive, requiring significant processing power and time.
* **Model Complexity:** It requires substantial understanding of the actuator’s physical behavior and FEA software features.
* **Meshing:** Creating a suitable mesh for the geometry is critical. A fine mesh can improve accuracy but increases computational cost. I remember spending hours perfecting the mesh around the air gap of an actuator to accurately capture the magnetic field variations.
* **Coupling multiple physics:** Accurately coupling electromagnetic, thermal, and structural analyses can be complex and requires careful consideration of the interactions between different physics.
Mitigating these challenges often involves simplifying the geometry where possible, using adaptive meshing techniques, and leveraging high-performance computing resources.
## How Can We Validate FEA Results for Magnet Heavy Actuators?
Validating FEA results is crucial to ensure their accuracy and reliability. This typically involves comparing simulation results with experimental measurements obtained from physical prototypes.
Here’s a table outlining common validation methods:
| Validation Method | Measurement | FEA Result to Compare | Tools Used |
| ———————– | ———————————————- | —————————- | ——————————————– |
| **Magnetic Field Mapping** | Measure magnetic field strength & direction | Magnetic flux density distribution | Gaussmeters, Hall effect sensors |
| **Force Measurement** | Measure force output at different positions | Magnetic force calculation | Load cells, force gauges |
| **Temperature Measurement**| Measure temperature at various locations | Temperature distribution | Thermocouples, infrared cameras |
| **Displacement Measurement** | Measure displacement under load | Structural deformation | Laser displacement sensors, strain gauges |
By comparing simulation results with experimental data, you can identify any discrepancies and refine the FEA model to improve its accuracy. This validation process is essential for building confidence in the simulation results and ensuring that the actuator performs as expected. A case study I recall clearly illustrates this point. We simulated the displacement of an actuator under load and then compared it with measurements from a laser displacement sensor. The initial discrepancy led us to refine the material properties in the model, ultimately resulting in excellent agreement between simulation and experiment.
## Can FEA Help Optimize Actuator Performance Characteristics?
Absolutely! FEA is a powerful tool for optimizing actuator performance characteristics, such as:
* **Force output:** Maximizing the force generated by the actuator for a given input current.
* **Efficiency:** Minimizing energy losses due to eddy currents and Joule heating.
* **Response time:** Minimizing the time it takes for the actuator to respond to a command signal.
* **Linearity:** Optimizing the linearity of the force-displacement relationship.
By systematically varying design parameters within the FEA model, you can identify the optimal combination that yields the desired performance characteristics. This optimization process can involve techniques like parameter sweeps, design of experiments (DOE), and optimization algorithms.
## What Are Emerging Trends in FEA for Electromagnetics in Actuator Design?
Several emerging trends are shaping the future of FEA in electromagnetics for actuator design:
* **Multiphysics simulations:** Integrating more physical phenomena into simulations, such as fluid-thermal-structural coupling.
* **AI-powered optimization:** Using machine learning algorithms to automate the optimization process and explore a wider range of design possibilities.
* **Cloud-based FEA:** Leveraging cloud computing resources to perform complex simulations and handle large datasets.
* **Digital Twins:** As sensors become more prevalent and data becomes cheaper to acquire, creating digital twins of actuatros is becoming increasingly possible.
* **Increased Computational Power:** Improvements to CPU speeds and computer architecture allow for faster simulations.
These trends are paving the way for more accurate, efficient, and comprehensive simulations, ultimately leading to better actuator designs.
## Are there case studies where FEA significantly improved Actuator Design?
Yes, numerous case studies highlight the power of FEA in actuator design:
* **Automotive Actuator:** FEA was used to reduce eddy current losses in an automotive solenoid actuator, resulting in a 15% improvement in energy efficiency and a reduction in operating temperature.
* **Robotics Actuator:** A research team used FEA to optimize the magnet arrangement in a robotic actuator, achieving a 25% increase in force output.
* **Medical Actuator:** FEA was employed to design a miniaturized actuator for a medical device, ensuring both high force density and precise control.
These examples demonstrate how FEA can address specific design challenges and significantly improve actuator performance across various applications.
## What Are the Main Advantages and Disadvantages of Utilizing FEA?
FEA offers a wide range of advantages for developing magnet heavy actuators:
**Vorteile:**
* **Reduces Development Costs:** Reduces the need for creating physical prototypes
* **Optimizes Actuator Performance:** Facilitates optimization for metrics like force output, speed, and efficiency
* **Improves Design Reliability:** Helps determine reliability by simulating behavior under various conditions.
* **Speed Up Time to Market:** Reduces development time by iterating quickly through virtual tests.
**Nachteile:**
* **High Computational Cost:** Advanced simulations require significant computing resources.
* **Requires Specialized Knowledge:** Demands deep knowledge about materials, physics and use of FEA software.
* **Model Simplifications:** Models must be simplified to be computationally tractable.
## Häufig gestellte Fragen (FAQs)
—
**How accurate are FEA simulations for magnet heavy actuators?**
The accuracy of FEA simulations depends on several factors, including the accuracy of the material properties, the quality of the mesh, and the complexity of the model. With careful setup and validation, FEA can provide highly accurate results, typically within a few percent of experimental measurements.
**How much does FEA software cost?**
FEA software costs can vary widely, from free open-source tools to expensive commercial packages. The cost depends on the features, capabilities, and licensing model of the software. Commercial packages often offer more advanced features and dedicated technical support.
**What kind of computer is needed to run FEA simulations?**
The hardware requirements for running FEA simulations depend on the complexity of the model. For simple 2D simulations, a typical desktop computer may be sufficient. However, for complex 3D simulations, a powerful workstation with a fast processor, ample memory (RAM), and a high-performance graphics card is recommended.
**How long does it take to run an FEA simulation?**
The simulation time depends on the complexity of the model, the mesh density, and the computational power of the hardware. Simple simulations may take only a few minutes, while complex simulations can take hours or even days to run. To shorten runtime, you may consider using a more powerful computer.
**Do I need a background in engineering to use FEA software?**
While it’s possible to learn the basics of FEA software without an engineering background, a solid understanding of engineering principles, especially electromagnetics, thermal transfer, and mechanical engineering, is essential for accurately interpreting simulation results and making informed decisions.
**What are some good resources for learning FEA?**
There are many resources available for learning FEA, including online courses, tutorials, textbooks, and software documentation. Software vendors often provide extensive training materials and support forums. Online communities and professional organizations also offer valuable learning resources.
—
## Conclusion: Harnessing FEA for Next-Generation Actuators
FEA is an indispensable tool for designing and optimizing magnet heavy actuators. By simulating complex electromagnetic, thermal, and mechanical behaviors, FEA enables engineers to maximize actuator performance, minimize energy losses, ensure structural integrity, and reduce development costs.
Hier sind die wichtigsten Erkenntnisse:
* FEA allows for virtual optimization of magnet heavy actuators.
* Accurate material data is critical for accurate simulation results.
* Validating FEA results with experimental measurements is essential.
* FEA is helping bring a new generation of AI-powered actuators onto the market!
* Emerging trends in FEA are paving the way for more accurate and efficient simulations and automated design processes.
Finite Element Analysis of Magnet Heavy Actuators
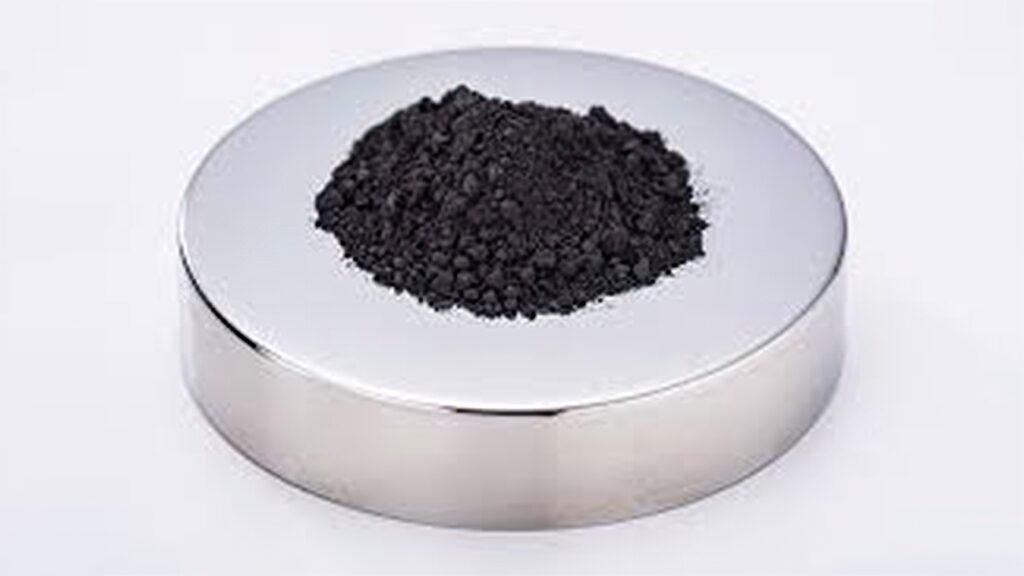