# Maximizing Magnet Strength: Improving the Pull Force of a Magnet with a Hole
Magnets with holes are incredibly versatile, used in everything from motors and sensors to crafting projects. But that hole can sometimes compromise their pull force. This article will delve into the nuances of optimizing the pull force of magnets with holes, providing practical strategies and scientific explanations. Whether you’re an engineer, hobbyist, or simply curious, you’ll gain valuable insights into maximizing the performance of these specialized magnets.
## Understanding Pull Force and its Relationship to Magnet Design
The pull force of a magnet is the amount of force required to detach the magnet from a ferromagnetic material (like steel). The design, including the presence of a hole, significantly impacts this force. The hole, while often necessary for mounting or other functional reasons, disrupts the magnetic flux flow, potentially reducing the overall holding power. Understanding how to compensate for this disruption is crucial.
### Why Does a Hole Affect the Pull Force of a Magnet?
A hole in a magnet creates a break in the magnetic circuit. Think of it like a kink in a garden hose. The magnetic flux, which represents the strength and flow of the magnetic field, has to divert around the hole. This diversion:
* **Reduces the cross-sectional area:** Less area for the flux to travel through directly diminishes the force.
* **Creates air gaps:** The hole introduces air, which has a much higher reluctance (resistance to magnetic flux) compared to the magnet material.
* **Distorts the magnetic field:** The hole distorts the field lines, concentrating them near the edges and potentially weakening them overall.
These factors combined contribute to a lower pull force compared to a solid magnet of the same dimensions and material. It’s akin to having fewer soldiers in an army – you simply have less force to exert.
### What Role Does Magnet Material Play in Maximizing Pull Force?
The material of the magnet is paramount. Neodymium (NdFeB) magnets are the strongest type readily available.
* **Neodymium (NdFeB):** These rare earth magnets offer the highest energy product and, consequently, the highest pull force for their size. They are more expensive but deliver unparalleled performance. Think of them as the Formula 1 cars of the magnet world.
* **Samarium Cobalt (SmCo):** SmCo magnets are also strong but less susceptible to demagnetization at high temperatures compared to Neodymium. They are a good option for applications with extreme heat, where Neodymium might not be suitable.
* **Ceramic (Ferrite):** Ferrite magnets are much weaker but also significantly cheaper. They are suitable for low-force applications. Imagine them as the reliable, fuel-efficient sedan – good for everyday use, but lacking in power.
* **Alnico:** Alnico magnets have good temperature stability but lower coercive force (resistance to demagnetization) than Neodymium or SmCo. They are often used in applications where the magnetic field needs to be consistent over a wide temperature range.
**Data:** The energy product of a Neodymium magnet can be more than 10 times higher than that of a Ferrite magnet.
**Table: Magnet Material Comparison**
| Material | Relative Strength | Temperature Resistance | Cost | Applications |
|——————-|——————–|————————|————-|———————————————|
| Neodymium (NdFeB) | Very High | Moderate | High | Motors, hard drives, sensors |
| Samarium Cobalt (SmCo) | High | High | Very High | High-temperature applications |
| Ceramic (Ferrite) | Low | High | Low | Speakers, magnetic separators |
| Alnico | Moderate | Very High | Moderate | Electric motors, guitar pickups |
### How Does the Size and Shape of the Magnet Affect Force?
Larger magnets generally have a higher pull force. A larger surface area allows for more magnetic flux to interact with the target material.
* **Size:** A magnet twice the size, assuming similar proportions, can have significantly more than twice the pull force. The relationship isn’t linear due to magnetic saturation effects. Think of it like a larger engine – it can generate more power.
* **Shape:** Disc magnets generally exhibit higher pull force than rod magnets of similar volume. The shape concentrates the flux at the surface.
* **Thin and Wide:** A thin, wide magnet will typically have a stronger pull force than a thick, narrow magnet of the same volume.
* **Cylindrical vs. Rectangular:** Cylindrical magnets often provide a more focused magnetic field, leading to higher pull forces when used in direct contact.
### Can the Hole’s Position and Size Be Optimized?
Absolutely! The characteristics of the hole (position and size) are critical.
* **Hole Position:** Ideally, the hole should be located in a region of the magnet where it minimally disrupts the main magnetic flux path. This usually means placing it closer to the center, avoiding the edges where the flux density is highest. Moving the hole slightly off-center might even improve the force in certain applications by strategically redirecting the flux.
* **Hole Size:** Smaller is better. Minimize the hole size as much as possible while still meeting the mechanical requirements. A smaller hole disrupts less of the magnetic circuit. Experimentation is key to finding the optimal balance.
**Diagram:** A simple diagram illustrating magnetic flux lines with a centered hole versus an off-centered hole could visually demonstrate the difference in flux distribution.
### What About Using Steel Washers or Backing Plates – Do They Help?
Yes! Steel washers and backing plates can dramatically improve the pull force.
* **Steel Washers:** Positioning a steel washer between the magnet and the target ferrous material concentrates the magnetic flux, increasing the effective surface area of contact and reducing the air gap.
* **Backing Plates:** A steel backing plate behind the magnet acts as a flux concentrator. It channels the magnetic field towards the front surface, significantly boosting the pull force. Experiment with different thicknesses of steel to find the optimal balance. A backing plate effectively reflects the magnetic field, directing it where you need it most.
* **Enclosed Pot Magnets:** Commercially available “pot magnets” fully enclose the magnet within a steel shell. This is a highly effective method for maximizing pull force.
**Statistics**: The pull force of a magnet can increase by 30-50% or more with the addition of a steel backing plate.
### Are There Coatings That Can Enhance Pull Force or Protect The Magnet?
Coatings themselves do not directly enhance pull force; however, they are essential for protecting the magnet from corrosion and damage, which can indirectly affect its performance in the long run.
* **Nickel Coating:** A common coating that provides good protection against corrosion.
* **Epoxy Coating:** Offers excellent resistance to harsh environments but may slightly reduce the magnetic field due to the increased distance from the target material.
* **Parylene Coating:** A thin, conformal coating that provides excellent protection without significantly affecting the magnetic field.
Maintaining the integrity of the magnet material ensures consistent pull force overtime.
### How Does the Air Gap Affect the Pull Force?
Air gaps are the enemy. The pull force drops off rapidly as the air gap increases.
* **Minimize Air Gap:** Ensure the magnet is making direct contact with the ferromagnetic material. Even a thin layer of paint or dust can significantly reduce the pull force. Clean contact surfaces are critical.
* **Surface Finish:** A smooth, flat surface on both the magnet and the target material minimizes the air gap created by surface imperfections.
**Case Study:** In an application requiring secure attachment, cleaning the metal surface with isopropyl alcohol prior to magnet placement resulted in a 20% increase in holding strength because of a reduced air gap.
### What About Magnet Orientation and Polarization?
The direction of the magnet’s polarization must be aligned correctly.
* **Polarization:** Ensure that the magnet’s poles are correctly oriented for maximum attraction. For example, if you are attaching the magnet to a steel plate, the north pole should be facing the plate. Misalignment will drastically reduce the effectiveness.
* **Multiple Magnets:** If using multiple magnets, ensuring they are all polarized in the same direction is vital. Reversing the polarity of just one magnet can dramatically reduce the overall force.
### Are There Specialized Magnet Designs for High Pull Force With a Hole?
Yes, specialized designs exist that counteract the weakening effect of the hole.
* **Counterbore Magnets:** These magnets have a recessed hole, allowing a screw head to sit flush. The recessed design maintains a larger surface area for contact, compensating for some of the losses due to the hole.
* **Multi-Pole Magnets:** While less common with through-holes, specialized magnet designs can incorporate multiple poles to concentrate the magnetic flux and improve the pull force. Often these are rings, which use alternating North and South poles to greatly increase the holding power.
* **Optimized Geometries:** Finite element analysis (FEA) software can be used to simulate the magnetic field distribution and optimize the shape of the magnet and the hole to maximize pull force. This is commonly done in advanced engineering applications.
## Common Pitfalls and How to Avoid Them
It’s easy to make mistakes when working with magnets with holes. Here are a few common pitfalls and how to avoid them:
* **Using too small of a magnet:** Always overestimate the required pull force. It’s better to have a magnet that’s slightly too strong than one that’s too weak.
* **Ignoring air gaps:** Ensure that the magnet makes direct contact with the target material. Clean surfaces and use steel washers or backing plates to minimize air gaps.
* **Using low-quality magnets:** Invest in high-quality Neodymium magnets from reputable suppliers for maximum performance.
* **Exposing magnets to high temperatures:** Neodymium magnets can lose their magnetism at high temperatures. Choose a magnet material with a higher Curie temperature if operating in a hot environment.
* **Incorrect hole placement:** The hole should be positioned to minimize disruption to the magnetic flux. Experiment with different hole locations to find the optimal solution.
## FAQ Section
**What is the best material for a strong magnet with a hole?**
Neodymium (NdFeB) is generally the best choice for applications requiring high pull force.
**How does the size of the hole affect the pull force?**
Generally, the bigger the hole, the lower the pull force. Minimize the hole size as much as possible.
**Can steel washers really make a difference?**
Yes! Steel washers concentrate the magnetic flux, significantly increasing the pull force.
**Is there a specific shape that maximizes pull force for magnets with a hole?**
Disc-shaped magnets generally have a higher pull force than rod-shaped magnets of the same volume. The hole position also matters.
**How can I protect my magnet from corrosion?**
Use a coated magnet (e.g., nickel-plated or epoxy-coated) to protect it from rust and corrosion.
**Can I increase the pull force of a magnet with a hole by repeatedly magnetizing it?**
No, the magnet’s strength is determined by its material and size, not the number of times it’s magnetized. Repeated magnetization won’t increase its pull force beyond its inherent capabilities.
## Schlussfolgerung
Improving the pull force of a magnet with a hole requires understanding the interplay of material properties, magnet geometry, and external factors. By carefully considering these elements and employing techniques like using steel washers and backing plates, you can significantly enhance the performance of these versatile components. I hope this blog post gave you the insights to achieve your magnet goals.
* **Material Matters:** Choose Neodymium for maximum pull force.
* **Minimize Air Gaps:** Ensure direct contact between the magnet and the target material.
* **Optimize Hole Placement:** Position the hole strategically to minimize flux disruption.
* **Use Steel Washers/Backing Plates:** Concentrate the magnetic flux and significantly increase pull force.
* **Protect Your Magnets:** Coatings like nickel or epoxy prevent corrosion.
* **Consider Magnet Size:** Always use appropriately sized magnet, as bigger magnets often yield increased pull force.
Improving the Pull Force of a Magnet with a hole
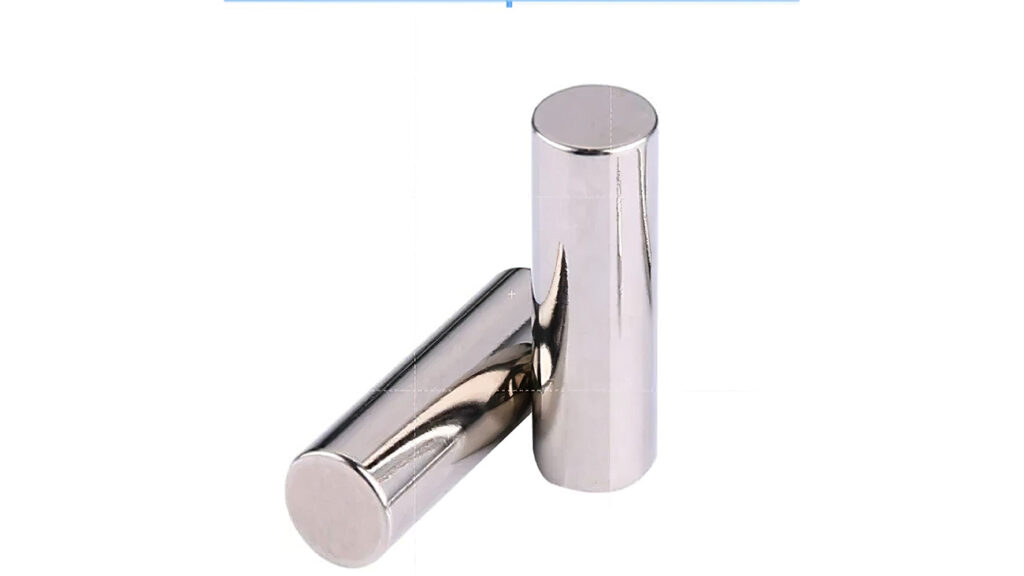