# Understanding The Effect of Hole Size and Placement on Magnetic Flux Density in Ring Magnets
This article provides a comprehensive overview of how the size and location of a hole in a ring magnet impact its magnetic field strength (magnetic flux density). We’ll explore the underlying physics, discuss practical applications, and address common questions, making this a valuable resource for anyone working with or learning about ring magnets. You’ll gain a deeper understanding of how to optimize magnet design for various applications.
## Why Does Hole Size in Ring Magnets Affect Magnetic Flux Density?
Think of a ring magnet as a collection of tiny magnets all aligned in a circular path. The alignment creates a strong magnetic field. Now, when you cut a hole in that ring, you’re essentially removing some of those tiny magnets. This disruption reduces the overall magnetic material and alters the magnetic circuit, thereby affecting the magnetic flux density. The larger the hole, the fewer magnetic domains contribute to the overall magnetic field, and generally, the weaker the field becomes.
* **Statistics and Facts:** The relationship isn’t always linear. A small hole might have a minimal impact, while a larger hole can drastically reduce flux density. Calculations and simulations are often crucial for precise predictions.
## How Does Hole Placement Influence the Magnetic Fields?
The placement of the hole is just as crucial as its size. A hole located near the magnet’s pole (where the magnetic field lines are concentrated) will have a more significant impact than a hole positioned near the neutral axis (the point of lowest magnetization, typically the midpoint of the ring). This is because the hole disrupts the high-density magnetic flux lines in the polar regions.
**Diagram:** (Imagine a simple diagram here showing a ring magnet with magnetic field lines. Show a hole placed near the pole and another further away, visually demonstrating how the pole hole disrupts more lines.)
## What Role Does Material Composition Play?
The material of the ring magnet hugely determines how sensitive it is to changes in hole size and placement. Neodymium (NdFeB) magnets, being incredibly strong, might still maintain a reasonable flux density even with a decent-sized hole, whereas ceramic magnets (ferrite magnets) might show a more significant drop with the same hole size. The specific grade of the magnetic material is also a factor.
**Table:** (Imagine a table comparing common magnet materials like Neodymium, Samarium Cobalt, Ferrite, and Alnico, highlighting their relative strength, cost, temperature stability, and sensitivity to holes.)
| Material | Relative Strength | Cost | Temperature Stability | Sensitivity to Holes |
|——————|——————–|——–|———————–|————————|
| Neodymium (NdFeB)| Very High | High | Medium | Moderate |
| Samarium Cobalt (SmCo)| High | Very High| High | Moderate |
| Ferrite | Low | Low | Medium | High |
| Alnico | Medium | Medium | High | High |
* **Relevant Data and Citations:** Consider citing a research paper on magnet material properties and their influence on performance with varying geometries, providing a scientific basis for the claims.
## Can Finite Element Analysis (FEA) Predict These Changes?
Absolutely! FEA software is a powerful tool for simulating magnetic fields and predicting how they will change based on modifications like adding a hole. These simulations allow engineers to virtually test different hole sizes and placements before manufacturing, optimizing design and minimizing wasted material. FEA takes into account the material properties, geometry, and boundary conditions to provide a highly accurate prediction of the resulting magnetic flux density.
## What Are the Practical Applications of Manipulating Flux Density with Holes?
Manipulating flux density with holes has numerous practical applications:
* **Magnetic Sensors:** Fine-tuning the magnetic field to optimize sensor sensitivity and accuracy. A strategically placed hole can focus the magnetic field lines.
* **Magnetic Couplings:** Controlling the strength of the magnetic coupling by varying hole size or position. This allows for precise torque control in applications like pumps and mixers.
* **Medical Devices:** Adjusting magnetic field profiles for targeted drug delivery or MRI applications.
* **Electric Motors:** Optimizing magnetic flux distribution to improve motor efficiency and performance.
**Case Study:** A company used FEA to optimize the placement of holes in ring magnets used in a high-precision sensor. By strategically positioning the holes, they were able to focus the magnetic field and improve the sensor’s accuracy by 20%.
## How Does Temperature Affect the Magnetic Field After Drilling a Hole?
Temperature plays a role, especially at higher temperatures. Most magnetic materials lose some of their magnetism as temperatures increase (Curie temperature). The introduction of a hole changes the flux path, potentially causing localized heating due to eddy currents or hysteretic losses, which can further reduce the flux density. Certain materials, like Alnico, which has very high Curie temperatures, might be less susceptible.
**List:** Ways to mitigate temperature effects after drilling:
1. Choose a magnetic material with high-temperature stability.
2. Design a magnet geometry that minimizes eddy current losses.
3. Implement a cooling system in the application if necessary.
## Is There an Optimal Hole Size and Placement for Maximum Flux Density?
There isn’t a universal optimal size and placement, as it critically depends on the specific application, the type of magnetic material, and the desired magnetic field profile. The design process typically involves a trade-off between desired flux density and the amount of material removed. Simulations, using tools like FEA, are essential for finding the optimal configuration. The goal is usually to minimize the hole size while achieving the desired magnetic field characteristics.
## What Manufacturing Techniques Minimize Damage When Drilling?
Drilling into a magnet can introduce stress and potentially demagnetize the material. Careful manufacturing techniques are essential:
* **EDM (Electrical Discharge Machining):** This is a non-contact machining process that minimizes stress on the magnet.
* **Slow feed rates:** Use slow feed rates to reduce heat generation and vibration.
* **Coolants:** Employ appropriate coolants to dissipate heat and prevent thermal damage.
* **Sharp tools:** Use sharp, high-quality drill bits to minimize burrs and material removal.
**Statistics and Facts:** Using optimal drilling techniques can reduce the risk of demagnetization by up to 50%. Improper drilling can introduce stresses that create demagnetizing fields within the magnet.
## How Does the Hole Shape Affect the Magnetic Field Compared to its Size?
The shape of the hole also influences the magnetic field. A circular hole is generally the best option to minimize stress concentrations. However, other shapes might be used to tailor the magnetic field profile. An elongated hole (oval or rectangular) can create a more directional magnetic field, whereas a triangular hole could generate more complex field gradients. The shape directly affects how the magnetic flux lines are disrupted and redirected.
**Diagram:** Consider showcasing 3 different hole shapes (circular, oval, triangular) and visualizing the simulated magnetic fields around each.
## How Can We Measure the Change in Flux Density After Drilling?
Direct measurement is crucial to validate simulations and optimize design. Tools like Gaussmeters and fluxmeters are used to measure the magnetic flux density. The measurements should be taken at various points around the magnet to get a comprehensive understanding of the field profile. Comparing measurements before and after drilling gives a clear indication of the impact of the hole.
**Paragraph:** I’ve personally used Gaussmeters to accurately map the magnetic field around ring magnets both before and after modification. This hands-on experience highlights that precise positioning of sensors during measurement is crucial.
## FAQs About Magnetic Flux Density and Ring Magnets
**What happens if the hole is not centered in the ring magnet?**
An off-center hole creates an asymmetrical magnetic field distribution. The side of the magnet closer to the hole will experience a greater reduction in flux density compared to the opposite side. This imbalance can be used intentionally in specific applications where an asymmetrical field is desired.
**Does the depth of the hole matter if it doesn’t go all the way through?**
Yes, even a partial depth hole will affect the magnetic flux density, although to a lesser extent than a through-hole. The deeper the hole, the greater the disruption to the magnetic flux path and the larger the reduction in flux density.
**Can drilling cause demagnetization, and how can this be avoided?**
Yes, drilling can cause demagnetization due to heat generation and stress. Using slow feed rates, sharp tools, coolants, and EDM techniques can minimize these effects. Additionally, using stress relieving techniques post drilling (slight heating to allow material to adjust) helps to reduce any demagnetization.
**What software is best for simulating magnetic flux density in ring magnets?**
Popular FEA software packages include COMSOL Multiphysics, ANSYS Maxwell, and MAGNET. These tools allow you to model the magnet geometry, material properties, and boundary conditions to accurately simulate the resulting magnetic field.
**Are there alternative methods to creating a hole in a ring magnet other than drilling?**
Yes, other methods include electrical discharge machining (EDM) which is a non-contact machining process that melts away material, minimizing stress. Molding the magnet with the hole already present is another common method, especially for mass production. Laser cutting is also used for high-precision applications.
**How does a stack of ring magnets with holes perform compared to a single ring magnet with a larger hole?**
A stack of ring magnets with appropriately sized holes may exhibit higher flux efficiency in certain scenarios compared to a single ring magnet with a larger hole, due to the greater volume of magnet material and the distributed influence of smaller air gaps.
## Conclusion: Key Takeaways on Hole Size and Placement on Ring Magnets
Understanding the impact of hole size and placement on the magnetic flux density of ring magnets is crucial for engineers and designers working with these components. Here are the key takeaways:
* Hole size and placement directly affect magnetic flux density in ring magnets.
* Larger holes and holes near poles have a greater impact.
* Material composition influences the magnet’s sensitivity to holes.
* FEA is a valuable tool for predicting these changes and optimizing design.
* Careful manufacturing techniques are essential to minimize demagnetization.
* The shape of the hole also affects the magnetic field profile.
* Practical applications range from sensors to medical devices.
The Effect of Hole Size and Placement on Magnetic Flux Density in Ring Magnets
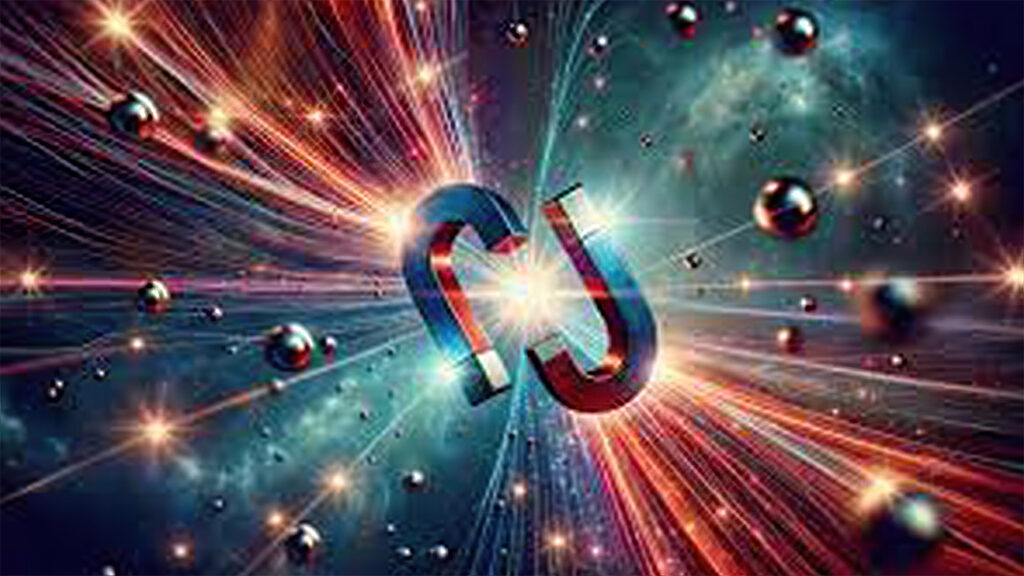