# Unlocking Peak Performance: Understanding Motor Torque with Ring Magnets
**Summary:** Ever wondered how powerful motors generate their rotational strength? This article dives deep into the fascinating world of motor torque, specifically focusing on the crucial role ring magnets play in optimizing performance. We’ll explore the principles behind torque generation, analyze the impact of ring magnet characteristics, address common challenges, and uncover practical strategies for maximizing torque output. You’ll gain a comprehensive understanding of how ring magnets contribute to efficient and potent motor operation, whether you’re a hobbyist, engineer, or simply curious about the technology that powers our world.
## What is Torque and Why is it Important in Motor Performance?
Torque, in simple terms, is a twisting force that causes rotation. It’s the “oomph” behind a motor’s ability to turn a shaft and do work. Think of it like tightening a bolt – the more effort (torque) you apply, the tighter you can make it. In a motor, torque determines how much load it can handle, how quickly it can accelerate, and its overall power. Without adequate torque, a motor might struggle to start under load, operate efficiently, or deliver the desired performance.
Therefore, maximizing torque is a primary goal in motor design. This involves carefully selecting materials, optimizing geometries, and strategically employing components like… you guessed it, ring magnets. A motor with high torque can handle heavy loads, maintain speed under pressure, and provide a more robust and reliable performance. A high torque motor is generally more desirable in most applications.
## How Do Ring Magnets Contribute to Motor Torque Generation?
Ring magnets, often strategically placed within the motor’s rotor or stator (depending on the motor’s construction – brushed or brushless DC), are essential for generating the magnetic field that interacts with the current-carrying conductors. This interaction creates the force necessary to produce torque. The stronger the magnetic field produced by the ring magnet, the greater the torque potential. The alignment and arrangement of these magnets are critical to maximizing the magnetic flux density, which directly affects the motor’s overall torque output.
The material these ring magnets are made from has a huge effect. Neodymium magnets, for instance, are incredibly strong and allow for smaller, more compact motors with impressive torque capabilities. Alnico magnets, while weaker, are more resistant to high temperatures, making them suitable for demanding applications. The choice of magnet material directly impacts the motor’s ability to generate and sustain torque under varying operating conditions.
## What Magnet Material is Best for High Torque Ring Magnets?
This is a complex question with no single answer! The “best” material depends entirely on the specific application’s requirements. However, **Neodymium (NdFeB) magnets** generally lead the pack for high torque applications due to their exceptional magnetic strength. Their high remanence (Br) and coercivity (Hcj) allows them to generate a strong magnetic field in a relatively small volume, which translates directly into increased torque. However, Neodymium magnets have limitations. They can be brittle and susceptible to demagnetization at high temperatures.
Alnico magnets offer better temperature stability and corrosion resistance but have significantly lower magnetic strength than Neodymium. Samarium Cobalt (SmCo) magnets provide a good balance of high strength and temperature resistance but are more expensive than Neodymium. Ferrite magnets are the least expensive option but offer the lowest magnetic strength. The selection must consider:
* **Operating Temperature:** How hot will the motor get?
* **Size and Weight:** Is there a size constraint?
* **Cost:** What is the budget?
* **Corrosion Resistance:** Will the motor be exposed to harsh environments?
* **Required Torque:** How much torque must be generated?
| Magnet Type | Magnetic Strength (approx.) | Temperature Resistance | Cost | Main Advantages | Disadvantages |
|————-|—————————–|————————|——|—————————————————|——————————————–|
| Neodymium | Highest | Lower | Mid | Highest torque for size, compact motors | Low temperature resistance, brittle |
| Samarium Cobalt| High | High | High | Good torque, high temperature resistance | More expensive than Neodymium |
| Alnico | Medium | Highest | Mid | High temperature resistance, good stability | Lower torque than Neodymium and SmCo |
| Ferrite | Lowest | Medium | Low | Inexpensive, widely available | Lowest torque, bulky |
## How Does Ring Magnet Arrangement Affect Torque Output?
The arrangement of ring magnets within a motor plays a crucial role in shaping and concentrating the magnetic field. A common configuration involves arranging multiple magnets with alternating polarities to create a strong and uniform magnetic field within the air gap between the rotor and stator. This ensures consistent torque generation as the rotor rotates. However, the optimal arrangement depends on the motor’s specific design and operating principles. Some arrangements are more efficient at focusing the magnetic flux, leading to increased torque, while others minimize cogging torque, which can cause jerky motion.
Consider a few possibilities:
* **Halbach Array:** This special arrangement concentrates the magnetic field on one side of the array, greatly increasing field strength and therefore torque. It is more complex to implement.
* **Multi-pole Arrangement:** Increasing the number of magnetic poles in the rotor or stator increases the frequency of interaction between the magnetic fields and the current-carrying conductors, leading to higher torque at lower speeds.
* **Segmented Ring Magnets:** Using multiple segmented ring magnets allows for finer control over the magnetic field distribution, enabling optimization for specific torque-speed characteristics.
## What is Cogging Torque and How Can Ring Magnets Minimize it?
Cogging torque, also known as detent torque, is an undesirable effect in permanent magnet motors that causes jerky motion, especially at low speeds. It arises from the interaction between the permanent magnets and the stator teeth (the iron core structures that house the windings). When the rotor is in certain positions relative to the stator teeth, it experiences a strong attraction that resists movement. This fluctuation in torque causes the rotor to “cog” or stick in these positions.
Ring magnets can be strategically designed to minimize cogging torque through several methods:
* **Skewing:** Magnet skewing involves angling the magnets relative to the stator teeth, effectively smoothing out the magnetic field distribution and reducing the abrupt changes in magnetic force that cause cogging.
* **Pole Shaping:** Modifying the shape of the magnet poles or the stator teeth can also help to distribute the magnetic flux more evenly, reducing cogging torque.
* **Fractional Slot Pitch:** Choosing a slot pitch that is not a whole number fraction of the pole pitch can disrupt the symmetry that leads to cogging.
* **Placement:** Careful placement and orientation of the ring magnets can help to cancel out the forces causing cogging torque.
## How Does Air Gap Size Impact Torque When Using Ring Magnets?
The air gap is the space between the rotor and the stator. The size of the air gap has a significant impact on the motor’s performance, particularly its torque. A smaller air gap generally leads to stronger magnetic fields in the air gap, resulting in higher torque. This is because a smaller air gap reduces the reluctance (resistance to magnetic flux) of the magnetic circuit, allowing more magnetic flux to flow. However, reducing the air gap too much can introduce challenges such as increased friction, potential for rotor-stator contact, and manufacturing difficulties.
A larger air gap, on the other hand, reduces the magnetic field strength and torque but can also improve the motor’s tolerance to manufacturing imperfections and thermal expansion. Choosing the optimal air gap size involves balancing the desire for high torque with the need for reliable and robust operation.
Therefore:
* **Smaller Air Gap = Higher Torque (generally), Increased risk of contact, tighter tolerances**
* **Larger Air Gap = Lower Torque, More forgiving of tolerances and thermal expansion**
## Can Finite Element Analysis (FEA) Optimize Ring Magnet Design for Torque?
Absolutely! Finite Element Analysis (FEA) is a powerful computational tool that allows engineers to simulate the behavior of electromagnetic fields in a motor. By creating a virtual model of the motor, including the ring magnets, stator, rotor, and windings, FEA can predict the magnetic flux distribution, torque output, cogging torque, and other performance parameters.
FEA enables engineers to:
* **Optimize magnet shape and arrangement:** Identify the optimal magnet geometry and placement to maximize torque and minimize cogging.
* **Evaluate different magnet materials:** Compare the performance of various magnet materials under different operating conditions.
* **Predict motor performance:** Accurately predict the motor’s torque-speed characteristics, efficiency, and thermal behavior.
* **Identify and mitigate potential problems:** Detect potential issues such as magnetic saturation or high eddy current losses.
By using FEA, engineers can significantly improve the motor’s design and optimize ring magnet characteristics for maximum torque performance. It’s a much more efficient and cost-effective method than relying solely on physical prototyping.
## What are Some Common Manufacturing Challenges When Using Ring Magnets?
Manufacturing motors with ring magnets, especially high-performance ones, presents several challenges:
1. **Handling and Assembly:** Ring magnets, particularly Neodymium magnets, are brittle and susceptible to chipping or cracking. They also have strong magnetic attraction forces, making them difficult to handle and assemble without specialized tooling and techniques. Controlling alignment during assembly is also critical.
2. **Magnet Alignment and Placement:** Precise alignment and placement of the ring magnets are crucial for achieving optimal performance. Even small misalignments can significantly degrade torque output and increase cogging torque.
3. **Adhesive Bonding:** Securing the ring magnets to the rotor or stator often involves adhesive bonding. Selecting the appropriate adhesive and ensuring proper bonding surfaces are critical for long-term reliability, especially under high temperatures and centrifugal forces.
4. **Magnet Demagnetization:** High temperatures, strong opposing magnetic fields, or mechanical stress can cause magnets to partially demagnetize, reducing their performance. Protecting the magnets from these factors is essential.
5. **Machining and Tolerances:** Maintaining tight tolerances on the magnet dimensions and the surrounding components is critical for achieving the desired air gap and magnetic field distribution. Machining magnetic materials can be challenging and requires specialized equipment and techniques.
Addressing these manufacturing challenges requires careful planning, precise manufacturing processes, and robust quality control measures.
## Case Study: Improving Torque in a Drone Motor with Ring Magnet Optimization
Let’s consider a hypothetical case study involving optimizing the ring magnets in a drone motor to improve its torque output. The initial drone motor’s performance was deemed inadequate for carrying heavier payloads and maintaining stable flight in windy conditions. The engineers suspected that the ring magnets were a limiting factor and decided to investigate.
**Initial Situation:**
* **Motor Type:** Brushless DC (BLDC) motor
* **Application:** Drone propulsion
* **Problem:** Insufficient torque, struggling with heavier payloads and wind gusts.
* **Existing Magnets:** Ferrite ring magnets (lower strength)
**Optimization Process:**
1. **FEA Simulation:** The engineers used FEA software to model the existing motor and analyze the magnetic flux distribution. The simulation revealed that the magnetic field strength in the air gap was relatively weak, limiting the torque output.
2. **Material Upgrade:** Based on the FEA results, the engineers decided to replace the ferrite magnets with Neodymium magnets (NdFeB), known for their significantly higher magnetic strength.
3. **Magnet Arrangement Optimization:** The FEA model was used to experiment with different magnet arrangements to maximize the flux density in the air gap and minimize cogging torque. They tested various skew angles and pole shaping to achieve the desired performance.
4. **Air Gap Adjustment:** The air gap was carefully optimized to balance torque output with manufacturing tolerances.
5. **Prototyping and Testing:** A prototype motor with the optimized ring magnets was built and tested. The test results showed a significant increase in torque compared to the original motor.
6. **Flight Testing**: The motor was placed into a drone and subsequently tested in various conditions.
* **Results:**
* **Increased Torque:** The optimized motor exhibited approximately 30% higher torque than the original motor.
* **Payload Capacity:** The drone could now carry heavier payloads without sacrificing performance.
* **Improved Stability:** The increased torque improved the drone’s stability in windy conditions.
* **Efficiency:** The motor’s efficiency remained comparable to the original design, despite the increased torque.
This case study demonstrates how careful selection, arrangement, and design of ring magnets, combined with FEA simulation, can significantly improve the torque performance of a motor. It highlights the importance of a data-driven approach to motor design and optimization.
## How Can I Measure the Torque of a Motor Using Ring Magnets?
Measuring motor torque is crucial for validating designs, assessing performance, and troubleshooting issues. Several methods exist for torque measurement, each with varying levels of accuracy and complexity:
* **Dynamometer:** A dynamometer is the most accurate method for measuring motor torque. It consists of a load-absorbing device that applies a controlled resisting force to the motor’s shaft. The dynamometer measures the force and rotational speed, allowing for precise torque calculation.
* **Prony Brake:** A Prony brake is a simpler and less expensive method. It involves applying friction to the motor’s shaft using a brake pad or belt. The force required to prevent the shaft from rotating is measured, and the torque is calculated. Prony brakes are less accurate than dynamometers.
* **Torque Sensor:** A torque sensor (or torque transducer) is an electronic device that directly measures the torque applied to a rotating shaft. It typically uses strain gauges to detect the twisting force.
* **Indirect Methods:** Indirect methods rely on measuring other parameters, such as input current and voltage, and using motor performance curves or equations to estimate the torque. These methods are less accurate but can be useful for quick estimations.
The best method for measuring torque depends on the required accuracy, budget, and available equipment. Dynamometers provide the most reliable results, while indirect methods offer a convenient and cost-effective alternative for less demanding applications.
## FAQ: Ring Magnets and Motor Torque
**How often should ring magnets in a motor be replaced?**
In most cases, ring magnets made from materials like Neodymium or Samarium Cobalt are designed to last the lifetime of the motor under normal operating conditions. Magnet degradation is slow, but high temperatures, mechanical damage, or exposure to corrosive environments can accelerate demagnetization. Regular inspection of the motor’s performance can help identify potential magnet-related issues.
**Do larger ring magnets always produce more torque?**
Not necessarily. While larger magnets generally have the potential to generate a stronger magnetic field, the optimal magnet size depends on the motor’s specific design, geometry, and operating parameters. It’s crucial to consider the overall magnetic circuit and optimize the magnet dimensions to maximize flux density in the air gap. A smaller, higher-grade magnet might outperform a larger, lower-grade one.
**Can the shape of the ring magnet affect the efficiency of the motor?**
Yes. The shape of the ring magnet significantly impacts the distribution of the magnetic field within the motor. Carefully designed shapes can minimize cogging torque, reduce eddy current losses, and improve the overall efficiency of the motor. Tools such as FEA are critical to designing a properly shaped magnet.
**Are there any safety precautions when working with ring magnets?**
Absolutely. Powerful ring magnets, especially neodymium varieties, can be dangerous. Their strong attractive force can cause pinching injuries if fingers or other body parts get caught between magnets or between a magnet and a metallic object. Keep magnets away from sensitive electronic devices, such as pacemakers and credit cards, as they can interfere with their operation. Always wear appropriate safety glasses and gloves when handling ring magnets, and be aware of the potential hazards.
**How does temperature affect the performance of ring magnets?**
Temperature is a critical factor. The magnetic strength of most ring magnets decreases as temperature increases. Neodymium magnets have a relatively low Curie temperature (the temperature at which they lose their magnetism), while Samarium Cobalt magnets are more resistant to high temperatures. Operating a motor at temperatures above the magnet’s recommended limit can cause irreversible demagnetization and performance degradation.
## Conclusion: Key Takeaways for Maximizing Motor Torque with Ring Magnets
* **Torque is the rotational force of a motor and is critical for performance.** Higher torque allows for handling larger loads.
* **Ring magnets are essential for generating the magnetic field that produces torque.** Their strength, material, and arrangement are all impactful.
* **Neodymium magnets are typically the best choice for high torque applications but have temperature limitations.** Consider Alnico or Samarium Cobalt for high-temperature environments.
* **The arrangement of ring magnets significantly influences torque output and cogging torque.** Proper skewing and pole shaping is key.
* **Smaller air gaps generally lead to higher torque, but require tighter manufacturing tolerances.**
* **Finite Element Analysis (FEA) is a valuable tool for optimizing ring magnet design for torque.**
* **Manufacturing challenges related to magnet handling, alignment, and bonding must be addressed carefully.**
* **Real-world case studies demonstrate the potential for significant torque improvement through ring magnet optimization.**
* **Various methods exist for measuring motor torque, with dynamometers providing the most accurate results.**
* **Understanding the relationship between ring magnets and motor torque is essential for designing high-performance and efficient motors.**
Torque Performance of a Motor using Ring Magnets
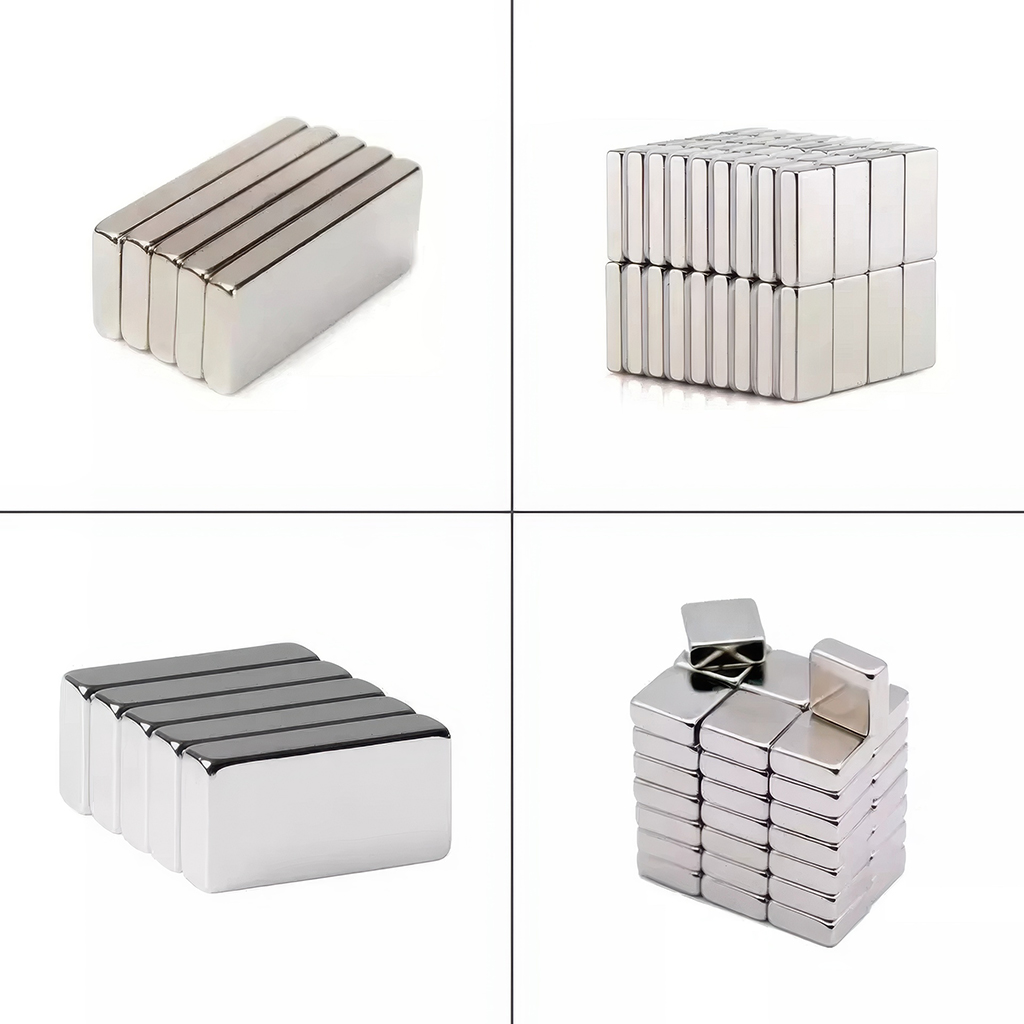