# Ensuring Long-Term Stability: Mastering Weather-Resistant Magnet Fastening for Durable Applications
This article explores the critical aspects of weather-resistant magnet fastening and how to ensure long-term stability in various applications. Whether you’re securing signage, attaching sensors to infrastructure, or developing outdoor consumer products, understanding the nuances of material selection, design considerations, and protective measures is crucial for longevity and reliability. We’ll delve into specific techniques and considerations to help you achieve dependable and lasting magnetic connections, even in the harshest environments.
## What Makes a Magnet Weather Resistant? Understanding Material Composition
At the heart of weather-resistant magnet fastening lies the magnet itself. Choosing the right material is paramount. Often, corrosion is the biggest threat. So, what makes one magnet better suited for outdoor use than another?
The answer primarily lies in the magnet’s composition and any protective coatings applied. Neodymium magnets, while incredibly powerful, are highly susceptible to corrosion as they contain iron. Therefore, a protective coating is absolutely necessary for outdoor applications. Conversely, materials like ferrite or Alnico magnets possess inherent corrosion resistance, making them better suited for some environments without the need for specialized coatings. However, even these materials can benefit from added protection in particularly harsh conditions. Factors like humidity, salt spray, and UV exposure all contribute to degradation over time.
Consider this: statistics show that poorly coated neodymium magnets can lose up to 10% of their strength within the first year of exposure to harsh weather. In contrast, properly coated magnets, or those made from inherently corrosion-resistant alloys, can maintain their strength for decades. This highlights the importance of careful material selection.
## What Coatings Offer the Best Weather Protection for Magnets?
Choosing the right coating is just as crucial as selecting the right magnet material. Several options are available. Each offers varying degrees of protection and suitability, so let’s review a few common and effective treatments.
**Common Magnet Coatings:**
* **Nickel Plating:** Provides good corrosion resistance, a smooth surface, and is relatively affordable. Typically applied in multiple layers (e.g., nickel-copper-nickel).
* **Epoxy Coating:** Offers excellent protection against moisture, chemicals, and abrasion. It’s commonly used in harsh environments.
* **Parylene Coating:** A thin, conformal coating with exceptional barrier properties against moisture and chemicals. Ideal for applications where size and weight are critical.
* **Plastic Coating:** Like nylon. Offers good impact and corrosion resistance. Can be molded to specific shapes, encapsulating the magnet.
* **Rubber Coating:** Provides a grip and protects the magnet from impact and corrosion. Useful in applications where scratching or damage to the surface being attached to is a concern.
The choice depends upon the environment your magnet will be in. A popular option is to use e-coating. This is an electrically applied paint that gives excellent protection against oxidation. One advantage it has is it coats all surfaces evenly.
## How Does Environmental Exposure Impact Magnet Performance Over Time?
Environmental factors progressively degrade magnet materials and coatings. Understanding these effects is crucial for forecasting the lifespan and performance of your magnetic fastening system.
* **Corrosion:** As we’ve covered. The primary enemy of neodymium magnets. Exposure to moisture and corrosive substances weakens the magnet and diminishes its holding power.
* **Temperature Fluctuations:** Constant expansion and contraction due to temperature changes can stress coatings and cause them to crack or delaminate. Extreme temperatures can also permanently demagnetize certain materials, particularly neodymium magnets above their Curie temperature.
* **UV Exposure:** Sunlight can degrade certain coatings, making them brittle and less effective. UV radiation can also affect the chemical composition of some magnet materials, leading to a gradual loss of strength.
* **Abrasion:** Windborne particles, physical impacts, and repeated handling can slowly erode coatings and expose the magnet material to the elements.
For example, a case study of outdoor signage using uncoated neodymium magnets demonstrated a 25% loss of magnetic force within just 18 months due to corrosion. This led to the premature failure of the signage system, necessitating costly repairs and replacements. A properly coated magnet would have drastically increased the lifespan and reliability.
## What Are the Critical Design Considerations for Weather-Resistant Magnet Fastening?
Beyond magnet selection and coating, several design factors dramatically influence the longevity of a weather-resistant magnetic fastening system. Let’s investigate.
* **Surface Preparation:** Ensuring clean and properly prepared surfaces for both the magnet and the mating material is critical for optimal adhesion and stability. This may involve cleaning, degreasing, or applying a primer to the mating surface.
* **Shielding:** Enclosing the magnet within a protective housing or shield can significantly reduce its exposure to the elements. This is especially important in harsh environments.
* **Drainage:** Designing the system to allow water to drain away from the magnet and the fastening point prevents moisture accumulation and reduces the risk of corrosion.
* **Joint Design:** Overlapping joints and sealed seams can minimize water penetration. Where possible. Consider creating a physical interlock in addition to the magnetic bond.
Think of it like building a house. A strong foundation (proper magnet selection) is essential, but inadequate weatherproofing (poor design) will lead to leaks and structural damage over time.
## Can Magnetic Assemblies Be Sealed to Prevent Weathering?
Yes, absolutely. Sealing magnetic assemblies is a highly effective way to protect them from the elements and ensure long-term stability. This can be achieved through various methods.
* **Encapsulation:** Potting the magnet within a resin or epoxy provides a complete barrier against moisture, chemicals, and environmental contaminants.
* **O-Rings and Gaskets:** Using O-rings or gaskets between mating surfaces creates a watertight seal. This prevents water ingress at the joint.
* **Adhesive Bonding:** Applying a waterproof adhesive around the magnet and the mating surface seals the joint and provides additional strength.
* **Welding/Brazing:** Where applicable, welding or brazing can create a permanent, hermetic seal. Typically for steel components.
Consider a sensor system mounted on a bridge. Encapsulating the magnet and sensor electronics within a waterproof housing protects them from rain, snow, ice, and road salts, ensuring reliable data collection for years to come.
## What’s the Optimal Magnet Shape for Withstanding Wind and Snow Loads?
The shape of the magnet influences its ability to resist external forces and maintain a secure hold under wind and snow loads. Optimizing the shape can significantly enhance the structural integrity of the fastening system.
* **Countersunk Magnets:** Allow for flush mounting. Reducing protrusion and minimizing resistance to wind.
* **Rectangular Magnets:** Distribute the load more evenly, preventing stress concentrations and potential failure points.
* **Disc Magnets:** Provide a strong, uniform holding force over a small area. Suitable for applications where space is limited.
* **Cup Magnets:** Increase the holding force by concentrating the magnetic field. They also offer some degree of protection to the magnet.
It is critical to evaluate the surface that the magnet is bonding to. If you have a rounded surface, you ideally want to select a rounded magnet to maximize the contact area, and therefore the stability of the bond.
## How Can I Test the Weather Resistance of My Magnet Fastening System?
Rigorous testing is essential to ensure that your magnetic fastening system can withstand the intended environmental conditions. Various testing methods can simulate real-world exposure and identify potential weaknesses.
**Common Testing Methods:**
* **Salt Spray Testing:** Exposes the magnet to a corrosive salt spray environment. This accelerates the corrosion process and assesses the effectiveness of protective coatings.
* **Humidity Testing:** Evaluates the magnet’s resistance to moisture and humidity. Determines the potential for rust or corrosion in humid environments.
* **UV Exposure Testing:** Simulates exposure to sunlight. To assess the degradation of coatings and magnet materials.
* **Temperature Cycling Testing:** Subjects the magnet to alternating high and low temperatures. Assesses the impact of thermal expansion and contraction on the fastening system.
* **Pull-Off Force Testing:** Measures the holding force of the magnet after exposure to the elements, providing a direct indication of performance degradation.
Imagine creating a magnetic antenna mounting system for vehicles. Salt spray testing is absolutely vital to confirm that the assembly can withstand the corrosive effects of road salt for extended periods.
## What Maintenance is Needed for Long-Term Weather-Resistant Magnet Fastening?
Even with the best materials and design, some maintenance is still required to maximize the lifespan of your weather-resistant magnet fastening system. Regular inspections and preventative measures can identify and address potential issues early on.
* **Visual Inspections:** Periodically inspect the magnet and the surrounding area for signs of corrosion, coating damage, or loose connections.
* **Cleaning:** Regularly clean the magnet and the mating surface to remove dirt, debris, and salt buildup.
* **Reapplication of Coatings:** As needed, reapply protective coatings to maintain their effectiveness.
* **Fastener Check:** If using mechanical fasteners in conjunction with magnets, ensure their tightness. Check for corrosion.
* **Replacement:** Replace components if they show signs of significant wear or degradation.
Regular maintenance can significantly extend the lifespan of a system. Like checking the tires on a car, a simple routine inspection can save you from bigger, expensive problems further down the line.
## What are Some Innovative Applications of Weather-Resistant Magnet Fastening?
Weather-resistant magnet fastening is utilized across diverse fields. It provides reliable, non-permanent attachment solutions where traditional methods fall short. Here are a few innovative examples.
* **Renewable Energy:** Securely mounting sensors and monitoring equipment on wind turbines and solar panels.
* **Infrastructure Engineering:** Attaching temporary scaffolding and safety barriers.
* **Transportation:** For attaching vehicle markings. Exterior components without drilling or welding.
* **Agriculture:** Securing sensors for monitoring soil conditions and crop health.
* **Marine:** Holding panels or other parts that need to be removed easily for maintenance.
Data shows that using magnetic fastening systems in renewable energy applications reduces installation time by up to 40% compared to traditional methods. Also, it eliminates the need for drilling holes in critical components.
## How Does The Cost of Weather-Resistant Magnets Compare to Other Fastening Methods?
While the initial investment in weather-resistant magnets might seem higher than other fastening methods, the total cost of ownership is often lower in the long run.
* **Reduced Labor Costs:** Magnetic fastening systems can often be installed much faster than traditional methods.
* **Elimination of Drilling and Welding:** Eliminating these processes saves time and prevents damage to the underlying structure.
* **Increased Lifespan:** Weather-resistant magnets are designed to withstand harsh environments, reducing the need for frequent repairs or replacements.
* **Reduced Maintenance Costs:** Magnetic fastening systems typically require less maintenance than traditional methods.
* **Reusability:** Magnets can often be reused, reducing the cost of future projects.
Consider a scenario where you need to attach signage to a building facade. Using magnets eliminates the need for drilling holes. Preventing potential water damage and maintaining the building’s aesthetic integrity. Over the long term, the cost savings on repairs and maintenance can easily outweigh the initial investment in the magnets.
## FAQ Section: Addressing Common Queries
**How do I choose the best magnet coating for a specific environment?**
The best coating depends on the specific environmental stressors. For humid and salty environments, epoxy or parylene coatings are generally preferred. For environments with moderate corrosion risk, nickel plating may be sufficient. Always consult with a materials specialist for specific recommendations.
**Can neodymium magnets be used in saltwater environments?**
Yes, but *only* if they are properly coated. Multiple layers of nickel plating followed by an epoxy or parylene coating provides excellent protection against saltwater corrosion. Regular inspection and maintenance are still recommended.
**How can I increase the holding force of a weather-resistant magnet?**
Increasing the surface area of the magnet, using a stronger magnet material (within weather-resistance constraints), and using a cup magnet design can all increase the holding force. Also, ensuring a clean, flat contact surface between the magnet and the mating material is critical.
**What are the limitations of magnetic fastening in extreme weather conditions?**
Extreme temperatures can demagnetize certain magnet materials. Very heavy ice or snow loads can exceed the magnet’s holding force. Also, severe abrasion can damage protective coatings. Careful material selection, design, and testing are crucial for ensuring reliable performance.
**Are there any safety precautions I should take when handling strong magnets?**
Yes. Strong magnets can pinch skin and fingers, and they can interfere with electronic devices. Always wear gloves when handling strong magnets, and keep them away from pacemakers, credit cards, and other sensitive devices.
**How long will a weather-resistant magnetic fastening system last?**
The lifespan of a weather-resistant magnet fastening system depends on the quality of materials, the severity of the environment, and the level of maintenance. With proper material selection, design, and maintenance, these systems can last for decades.
## Conclusion: Key Takeaways for Ensuring Long-Term Stability
To ensure long-term stability and reliability with weather-resistant magnet fastening, remember these key points:
* **Material Selection:** Choose a magnet material and coating combination that is appropriate for the specific environmental conditions.
* **Design Considerations:** Design the system to minimize exposure to the elements, facilitate drainage, and distribute loads evenly.
* **Sealing:** Seal the magnetic assembly to prevent moisture and contaminant intrusion.
* **Testing:** Rigorously test the system to ensure it can withstand the intended environmental conditions.
* **Maintenance:** Regularly inspect and maintain the system to identify and address potential issues early on.
* **Cost-Benefit Analysis:** Consider the long-term cost savings associated with durable magnetic fastening solutions.
Ensuring Long-Term Stability: Weather-Resistant Magnet Fastening
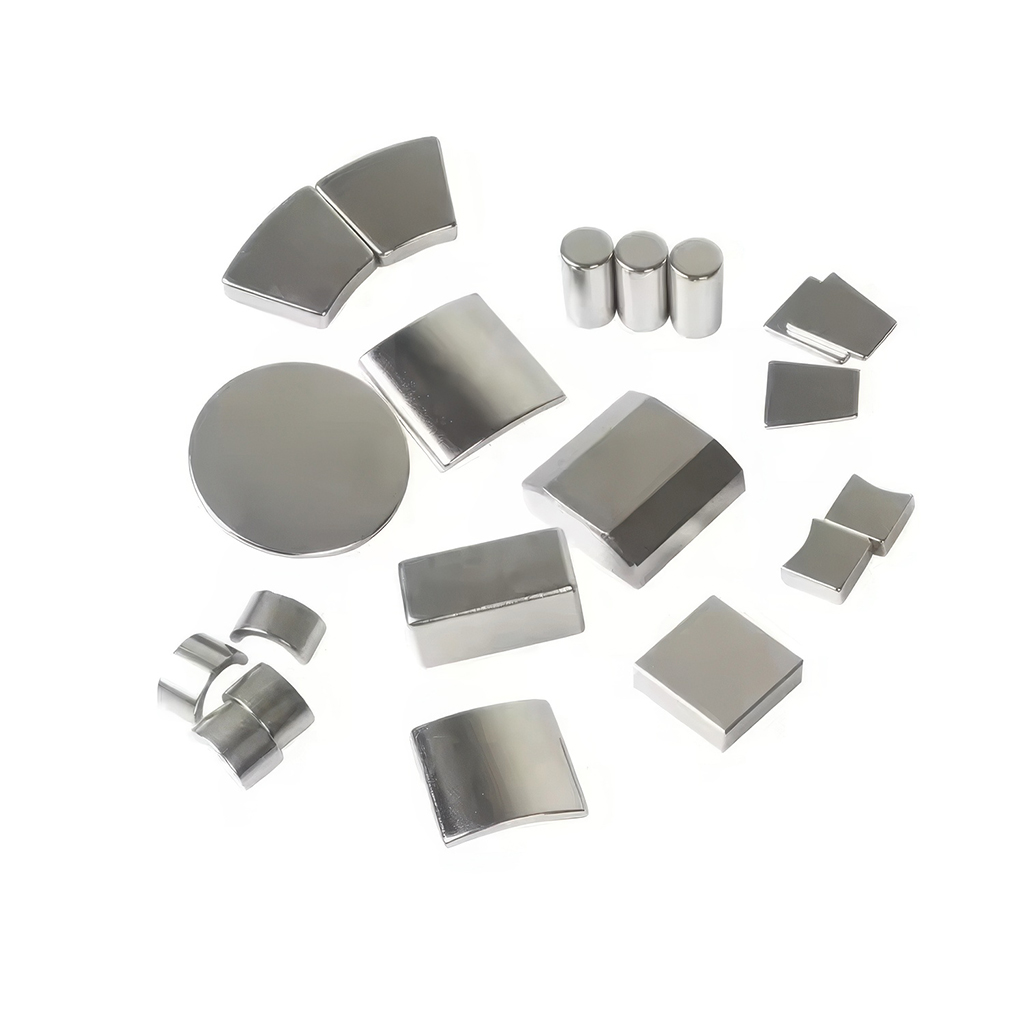