# Fastening Magnets in Motors: Achieving Robust Reliability and Optimal Performance
This article dives deep into the critical world of fastening magnets in electric motors. We’ll explore various methods, materials, and considerations to ensure your motor designs are not only powerful but also exceptionally reliable. This is a must-read for engineers, designers, and anyone involved in motor manufacturing or maintenance who wants to understand how to optimize magnet fastening for peak performance and longevity. I’ll share insights gleaned from years of experience and research, helping you avoid common pitfalls and maximize the potential of your motor designs.
## Why is Magnet Retention Critical for Motor Performance and Longevity?
Magnet retention is paramount! If magnets become detached or even slightly displaced within a motor, the consequences can be severe. This includes reduced torque output, increased vibration and noise, and potentially catastrophic failure. Think of it like this: the magnets are the engine’s pistons – if they aren’t firmly in place and moving correctly, nothing will work properly. Proper fastening directly translates to a longer lifespan and consistently high performance from your motor. Statistical data shows that poor magnet retention is a leading cause of motor failure, accounting for up to 30% of failures in some applications.
## What are the Common Magnet Fastening Methods Used in Motors?
Several techniques are employed to secure magnets in motors, each with its advantages and disadvantages. The choice depends on factors like motor size, operating environment, desired performance, and cost constraints. Common methods include:
* **Adhesive Bonding:** Using epoxies or other structural adhesives to glue the magnets in place.
* **Mechanical Retention:** Employing clips, cages, or other physical structures to hold the magnets.
* **Shrink Fitting:** Heating the rotor or stator and allowing it to cool and shrink around the magnets.
* **Interference Fit:** Press-fitting the magnets into a slightly smaller slot.
* **Hybrid Approaches:** Combining adhesive bonding with mechanical retention for added security.
Each of these methods offers a different level of strength, cost, and complexity. Understanding these differences is key to selecting the right solution.
## Adhesive Bonding: What are the Best Adhesive Selection Criteria for Motor Magnets?
Selecting the right adhesive is crucial for successful magnet bonding. Key considerations include:
* **Shear Strength:** The adhesive’s ability to resist forces trying to slide the magnets apart.
* **Temperature Resistance:** The adhesive must maintain its strength at the motor’s operating temperature.
* **Chemical Resistance:** Resistance to oils, solvents, and other chemicals the motor might encounter.
* **Gap-Filling Ability:** How well the adhesive fills any gaps between the magnet and the housing.
* **Viscosity:** Ensuring the adhesive flows easily and wets the surfaces properly.
* **Cure Time:** Balancing the need for a quick cure with adequate working time.
Epoxies are commonly used due to their high strength and temperature resistance. However, cyanoacrylates (super glues) and acrylics can also be suitable for certain applications. Look for adhesives specifically formulated for magnet bonding; these often contain fillers to improve bond strength and thermal conductivity.
| Adhesive Type | Advantages | Disadvantages | Best Suited For |
|—————|——————————————|——————————————-|————————————————|
| Epoxy | High strength, temperature resistance | Longer cure times, requires mixing | High-performance motors, demanding environments |
| Cyanoacrylate | Fast cure time, easy to apply | Lower strength, poor temperature resistance | Small motors, limited temperature range |
| Acrylic | Good adhesion to various materials | Can be brittle, may require surface prep | Medium-sized motors, general-purpose applications |
## Mechanical Retention: When is it the Best Approach?
Mechanical retention is an excellent choice when dealing with high centrifugal forces, extreme temperatures, or environments where adhesives might degrade. This method involves using physical structures like clips, cages, or retaining rings to hold the magnets in place.
* **Benefits:** Robust, reliable, and less susceptible to environmental factors than adhesives alone.
* **Drawbacks:** Can be more complex and expensive to implement than adhesive bonding. May also add weight to the motor.
Consider mechanical retention for motors operating at high speeds, in high-temperature environments, or where adhesive compatibility is a concern. They are especially valuable in safety-critical applications such as electric vehicles or aerospace.
## Shrink Fitting vs. Interference Fit: Which Offers Superior Magnet Retention?
Both shrink fitting and interference fit methods rely on the principle of compressing the magnet within the rotor or stator.
* **Shrink Fitting:** The outer component (rotor or stator) is heated, expanding its inner diameter. The magnet is then inserted, and as the outer component cools, it shrinks around the magnet, creating a tight fit.
* **Interference Fit:** The magnet is slightly larger than the slot it’s being pressed into. This requires force to insert the magnet, creating a compressive force that holds it in place.
**Shrink fitting generally provides superior magnet retention** because it creates a more uniform and consistent compressive force around the entire magnet. An interference fit can create stress concentrations at the corners of the magnet, potentially leading to cracking or chipping over time. However, interference fitting can be a more cost-effective solution for certain applications.
## How Does Motor Operating Temperature Affect Magnet Fastening Reliability?
Temperature plays a major role in magnet fastening reliability. Elevated temperatures can weaken adhesives, cause thermal expansion mismatch between the magnet and the housing, and accelerate corrosion.
* **Adhesive Degradation:** High temperatures can reduce the strength and elasticity of adhesives, leading to bond failure.
* **Thermal Expansion Mismatch:** Magnets and motor housings typically have different coefficients of thermal expansion. This difference can induce stresses on the adhesive bond or mechanical retention features, potentially causing failure.
* **Corrosion:** Elevated temperatures can accelerate corrosion, especially in humid environments. Corrosion products can weaken the bond between the magnet and the housing.
Therefore, careful consideration of the motor’s operating temperature range is essential when selecting a magnet fastening method. High-temperature adhesives or robust mechanical retention systems may be necessary for demanding applications. Data indicates that for every 10°C increase in operating temperature, the lifespan of some adhesives can decrease by as much as 50%.
## What Surface Preparation is Necessary for Optimal Adhesive Bonding?
Proper surface preparation is essential for achieving a strong and durable adhesive bond. This involves removing contaminants, creating a rough surface for better adhesion, and applying a primer if necessary.
* **Cleaning:** Remove oil, grease, dirt, and other contaminants from both the magnet and the housing using a suitable solvent.
* **Abrasion:** Roughen the surfaces with sandpaper or grit blasting to increase the surface area for bonding.
* **Priming:** Apply a primer to the surfaces to improve adhesion and protect against corrosion.
Following these steps will significantly improve the bond strength and long-term reliability of your magnet fastening system. For instance, studies show that proper abrasion can increase bond strength by up to 30%.
## What are the Best Practices for Applying Adhesives to Motor Magnets?
Applying adhesive correctly is just as important as selecting the right adhesive and preparing the surfaces.
* **Consistent Application:** Apply a uniform layer of adhesive to both the magnet and the housing. Avoid applying too much or too little adhesive.
* **Bubble Prevention:** Minimize air bubbles in the adhesive layer, as these can weaken the bond.
* **Proper Curing:** Follow the adhesive manufacturer’s instructions for curing time and temperature.
* **Fixturing:** Use fixtures to hold the magnets in place during the curing process, ensuring proper alignment and preventing movement.
These practices ensure that the adhesive bonds effectively and provides the necessary strength and durability. Remember, adhesive failures are often attributed to improper application rather than the adhesive itself.
## How can Finite Element Analysis (FEA) Help Optimize Magnet Fastening Design?
Finite Element Analysis (FEA) allows engineers to simulate the performance of magnet fastening systems under various operating conditions. This can help identify potential weaknesses and optimize the design before manufacturing.
* **Stress Analysis:** FEA can predict the stress distribution in the adhesive bond or mechanical retention features, allowing engineers to identify areas of high stress concentration.
* **Thermal Analysis:** FEA can simulate the temperature distribution in the motor and predict the impact of thermal expansion on the magnet fastening system.
* **Vibration Analysis:** FEA can analyze the motor’s vibration characteristics and predict the potential for magnet loosening or detachment due to vibration.
By using FEA, engineers can optimize the magnet fastening design to minimize stress, improve thermal performance, and enhance vibration resistance, ultimately leading to a more reliable and durable motor.
## What Quality Control Measures Should Be in Place for Magnet Fastening?
Implementing robust quality control measures is essential to ensure that magnets are consistently and reliably fastened in motors.
* **Incoming Inspection:** Inspect incoming magnets and adhesives to ensure they meet specifications.
* **Process Control:** Monitor and control the adhesive application and curing processes.
* **Destructive Testing:** Periodically perform destructive testing (e.g., pull tests) to verify the bond strength.
* **Non-Destructive Testing:** Employ non-destructive testing methods like ultrasonic testing to detect voids or delaminations in the adhesive bond.
* **Visual Inspection:** Implement thorough visual inspections at multiple stages of the process to identify any obvious defects.
These quality control measures will help identify and correct any issues before they lead to motor failures. By implementing these measures, you can ensure that your magnet fastening processes are robust and reliable, leading to higher-quality motors.
## Frequently Asked Questions (FAQ)
**What is the primary cause of magnet detachment in electric motors?**
The primary causes include inadequate adhesive selection, improper surface preparation, high operating temperatures, and vibration. Poor design featuring insufficient mechanical retention can also contribute.
**How often should I replace the magnets in an electric motor?**
Unless there’s a specific reason like damage or degradation, most magnets used in modern electric motors are designed to last the lifespan of the motor. Regular inspection and preventive maintenance of the fastening method are far more important than preemptive magnet replacement. Factors like operating temperature and duty cycle can impact magnet lifespan.
**Can I use super glue to fasten magnets in a motor?**
While cyanoacrylates (super glues) offer fast curing, they are generally **not suitable** for fastening magnets in high-performance motors due to their lower strength and poor temperature resistance. Epoxies or specialized adhesives designed for magnet bonding are typically preferred.
**What is the best way to clean magnets before bonding?**
The best approach depends on the contaminant. However, generally, using a solvent like isopropyl alcohol or acetone, followed by abrasion with sandpaper, and then a final wipe with a clean cloth, is a good starting point. Always follow the adhesive manufacturer’s recommendations.
**Are there any environmentally friendly adhesives for magnet bonding?**
Yes, there are bio-based adhesives that offer comparable performance to traditional epoxies. These are becoming increasingly popular as manufacturers seek to reduce their environmental footprint. Researching specific products and their technical specifications is crucial for ensuring suitability.
**What’s the optimal adhesive thickness for magnet fastening?**
The optimal adhesive thickness depends on several factors, including the adhesive type, the size of the magnets, and the operating conditions of the motor. Generally, a thin, uniform layer of adhesive (typically between 0.05mm and 0.15mm) is preferred. Too much adhesive can lead to stress concentrations, while too little adhesive may not provide adequate bonding strength. Always consult the adhesive manufacturer’s recommendations.
## Conclusion
Ensuring the proper fastening of magnets in your electric motors is a critical step to optimize performance, reliability, and longevity. Understanding the different fastening methods, selecting the appropriate materials, and implementing robust quality control measures are all essential for success.
Here are the key takeaways to remember:
* Magnet retention is critical for motor performance and longevity.
* Adhesive bonding, mechanical retention, shrink fitting, and interference fit are common fastening methods.
* Proper adhesive selection and surface preparation are essential for adhesive bonding.
* Temperature plays a significant role in magnet fastening reliability.
* FEA can help optimize magnet fastening design.
* Robust quality control measures are essential for ensuring consistent and reliable magnet fastening.
By following these guidelines, you can ensure that your motors perform optimally and reliably for many years to come. Good luck!
Fastening Magnets in Motors: Ensuring Reliability and Performance
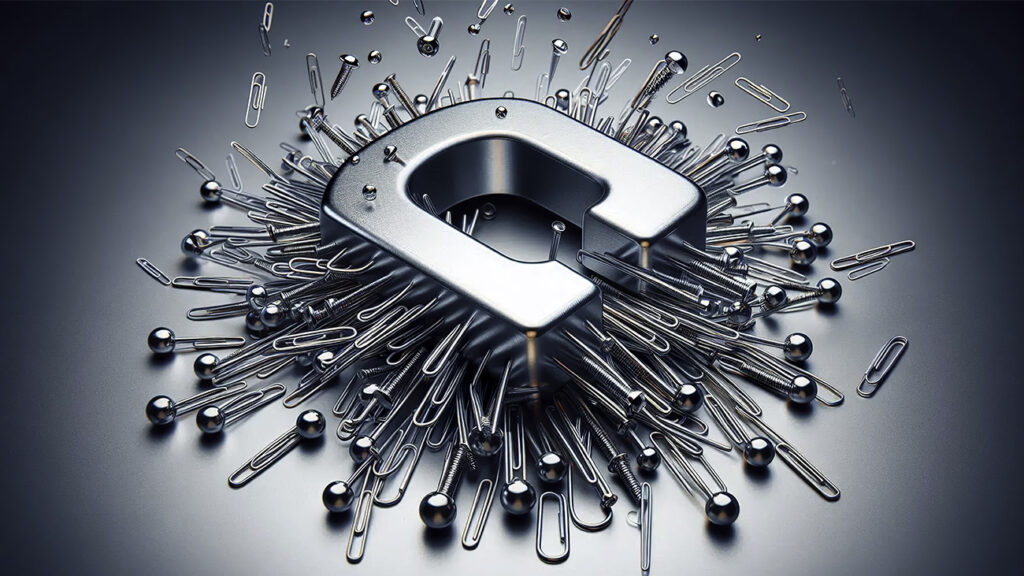