# From Manufacturing to Medical: Unveiling the Versatile Role of Hole Magnets
Hole magnets, those unassuming discs with a central aperture, are far more than just simple fasteners. They’re silently revolutionizing industries from heavy manufacturing to cutting-edge medical devices. This article explores the incredible adaptability of hole magnets, diving into their diverse applications and showcasing why they’re essential components across vastly different sectors. Get ready to discover the power and potential hidden within these magnetic marvels!
## Why Are Hole Magnets Gaining Traction in Manufacturing?
The manufacturing sector demands strength, precision, and reliability. Hole magnets are increasingly replacing traditional fastening methods due to their superior performance and ease of use. They offer a non-destructive and reversible attachment method, crucial for prototyping and iterative design processes. The ability to quickly assemble and disassemble components without damaging them is a significant advantage.
Think about the automotive industry. Assembly lines utilize hole magnets extensively. Holding jigs equipped with these magnets secure car parts during welding and painting, improving efficiency and accuracy. Their consistent holding force ensures components remain firmly in place, minimizing errors and rework.
Moreover, the inherent adjustability offered by hole magnets allows for greater flexibility in manufacturing processes. Operators can easily reposition components as needed, optimizing workflow and reducing downtime. This adaptability is especially valuable in custom manufacturing scenarios where precision and rapid adjustments are paramount.
## How Do Hole Magnets Contribute to Precision in Medical Devices?
The medical field demands extreme precision and reliability. Hole magnets, with their consistent magnetic field and ability to be precisely positioned, are finding increasing use in medical devices.
One crucial application is in MRI machines. Hole magnets are integrated into sensors that need to be precisely aligned within the powerful magnetic field of the MRI. Their stable magnetic properties ensure accurate readings and clear images, crucial for diagnosis.
Another interesting use is in surgical instruments. Miniature hole magnets are used in robotic surgery tools, enabling surgeons to manipulate instruments with incredible precision. The consistent magnetic attraction allows for fine motor control, leading to less invasive procedures and faster recovery times for patients. The small size and powerful holding force make them ideal for these intricate applications.
## From Simple Fasteners to Sophisticated Assemblies: What Types of Hole Magnets Are Used?
The term “hole magnet” encompasses a wide range of materials and configurations. The specific type chosen depends heavily on the application and performance requirements.
* **Neodymium (NdFeB) Magnets:** These are the strongest type of permanent magnets and are often used when high holding force is required in a small footprint. They’re a popular choice for medical device applications where space is limited.
* **Samarium Cobalt (SmCo) Magnets:** These magnets offer excellent temperature stability and corrosion resistance, making them suitable for demanding environments. They are often used in aerospace and defense applications.
* **Ferrite Magnets:** These are the most cost-effective type of magnet and are widely used in manufacturing and industrial applications where cost is a primary consideration.
* **Alnico Magnets:** These magnets offer good temperature stability but lower holding force compared to neodymium magnets.
The selection of the appropriate magnet material involves considering factors like temperature range, corrosiveness of the environment, required holding force, and budget. Furthermore, the size and shape of the hole significantly impact the magnet’s performance.
## What Role Do Hole Magnets Play in Magnetic Separation in Manufacturing?
Magnetic separation is a critical process in many manufacturing industries, especially in recycling and material processing. Hole magnets play a vital role in removing ferrous contaminants from non-ferrous materials.
In recycling plants, powerful magnetic separators equipped with hole magnets are used to separate steel and iron from other recyclable materials, such as plastics and aluminum. This process allows for the efficient recovery of valuable resources and helps reduce waste. The hole magnets enable the construction of robust magnetic grids or drums that effectively capture ferromagnetic materials.
In the food processing industry, magnetic separators are used to remove tiny metal fragments from food products, ensuring consumer safety. These separators are often equipped with high-strength neodymium hole magnets to capture even the smallest metal particles. This is a critical safety measure to prevent injury and product recalls.
## How do Hole Magnets Contribute to Motor Assembly?
Electric motors are ubiquitous, powering everything from electric vehicles to household appliances. Hole magnets play a critical role in the efficient and reliable operation of electric motors.
Magnets are used in the rotor and stator assemblies to generate the magnetic field that drives the motor. High-performance neodymium hole magnets are often preferred due to their superior magnetic strength, allowing for smaller and more efficient motor designs. This leads to increased power density and improved performance.
Precision is crucial in motor assembly. Hole magnets facilitate precise placement and alignment of the magnets within the motor, ensuring optimal performance and minimizing energy losses. Their inherent holding force simplifies the assembly process and reduces the risk of misalignment.
## Can Hole Magnets Be Used in Holding Fixtures for Welding?
Welding requires secure and precise positioning of components. Hole magnets are commonly used in welding fixtures to hold metal parts in place during the welding process.
Magnetic welding clamps equipped with hole magnets provide a quick and easy way to secure workpieces, freeing up the welder’s hands. These clamps offer adjustable angles and strong holding force, allowing for accurate and efficient welding.
The use of magnetic welding fixtures improves weld quality and reduces the risk of errors. They also contribute to a safer working environment by minimizing the need for manual holding, preventing potential accidents.
## Are Hole Magnets Used in Medical Implants?
While not as prevalent as in other medical applications, hole magnets are finding niche applications in medical implants.
One emerging area is in magnetic dental implants. Hole magnets can be used to secure dentures, providing a more stable and comfortable fit. These magnets attach to titanium posts implanted in the jawbone, offering a strong and reliable connection.
Researchers are also exploring the use of hole magnets in targeted drug delivery systems. Magnets can be used to guide drug-containing nanoparticles to specific areas of the body, improving treatment efficacy and reducing side effects. This is a promising area of research that could revolutionize cancer treatment and other therapies. These magnets are typically coated with biocompatible materials to ensure safety within the body.
## What Advantages Do Hole Magnets Bring to Automation Systems?
Automation is transforming industries across the board. Hole magnets offer several advantages in automation systems, contributing to increased efficiency and productivity.
They are used in robotic grippers to pick and place parts quickly and efficiently. The magnets provide a strong and reliable grip, allowing robots to handle a wide range of materials and shapes.
Additionally, hole magnets are used in sensors for detecting the position and movement of objects. These sensors are integrated into automated machines to monitor performance and ensure precise control.
The ease of integration and reliable performance of hole magnets make them ideal for automation applications. They contribute to increased speed, accuracy, and efficiency in manufacturing and other industries.
## Can Hole Magnets Affect Other Electronic Components?
It’s important to be aware of the potential impact of magnetic fields on other electronic components. While hole magnets themselves are not susceptible to interference, their magnetic fields can affect sensitive electronic devices.
Magnetic fields can interfere with the operation of sensors, actuators, and other electronic components. It’s crucial to carefully consider the placement of magnets and other components to minimize potential interference. Shielding can be used to reduce the impact of magnetic fields on sensitive equipment.
Particularly in medical devices, thorough testing is essential to ensure that the magnets do not interfere with the operation of other electronic components. Safety regulations dictate these stringent testing processes.
## How Can I Choose the Right Hole Magnet for My Specific Application?
Selecting the right hole magnet requires careful consideration of several factors. To make the right choice, you need to answer a few questions about your specific needs:
1. **What is the required holding force?** Determine the minimum force needed to securely hold the object in place.
2. **What is the operating temperature?** Choose a magnet material that can withstand the operating temperature range.
3. **What is the environmental condition?** Consider factors like humidity, corrosion, and exposure to chemicals.
4. **What are space limitation?** Define the available physical space to determine magnet dimensions.
5. **What is the budget?** Balance performance requirements with cost considerations.
Consult with a magnet supplier to discuss your specific requirements and receive expert advice. They can help you select the optimal magnet material, size, and shape for your application. Provide as much detail as possible about your application to ensure a tailored solution.
## FAQ: Common Questions About Hole Magnets
**What are the different grades of neodymium magnets?**
Neodymium magnets are graded based on their maximum energy product, a measure of their magnetic strength. Common grades include N35, N42, N52, with higher numbers indicating stronger magnets. The choice of grade depends on the required holding force and application requirements.
**Are hole magnets prone to demagnetization?**
The likelihood of demagnetization depends on the magnet material and operating conditions. Neodymium magnets are relatively resistant to demagnetization at moderate temperatures, while ferrite magnets are more susceptible at higher temperatures. Exposure to strong opposing magnetic fields can also cause demagnetization.
**How are hole magnets manufactured?**
Hole magnets are typically manufactured through powder metallurgy. The raw magnetic material is ground into a fine powder, pressed into the desired shape with the hole already formed, and then sintered at high temperatures. The magnet is then magnetized in a strong magnetic field.
**Can hole magnets be customized with different coatings?**
Yes, hole magnets can be coated with various materials to improve corrosion resistance, abrasion resistance, and aesthetic appearance. Common coatings include nickel, zinc, epoxy, and Parylene. The choice of coating depends on the specific application and environmental conditions.
**What safety precautions should I take when handling strong hole magnets?**
Strong hole magnets can pose pinch hazards and can damage electronic devices. Always handle magnets with care, keeping fingers and other body parts away from the magnetic field. Keep magnets away from electronic devices, credit cards, and other magnetically sensitive items. If you’re implementing hole magnets in a medical device, follow all the relevant regulatory safety guidance.
**Are there any environmentally friendly alternatives to traditional hole magnets?**
Researchers are exploring alternative magnet materials that are less reliant on rare earth elements. These alternatives are still under development but offer the potential for more sustainable magnet production in the future. Some emerging options include iron nitride magnets and textured manganese aluminum alloys.
## Conclusion: Hole Magnets – Versatile Components Shaping Industries
From the assembly line floor to the surgical suite, hole magnets play a silent but crucial role in modern industries. Their versatility, reliability, and precision make them indispensable components.
Here are the key takeaways:
* Hole magnets are used extensively across diverse industries, from manufacturing and automotive to medical devices and electronics.
* They offer strong holding force, precise positioning, and ease of use.
* Different magnet materials are available to accommodate various operating conditions and performance requirements.
* Hole magnets are used in applications like magnetic separation, welding fixtures, motor assembly, and medical implants.
* Careful consideration is needed when selecting the appropriate magnet material and size for a specific application.
* Understanding the potential impact of magnetic fields on other electronic components is crucial for safe and reliable operation.
From Manufacturing to Medical: The Role of Hole Magnets
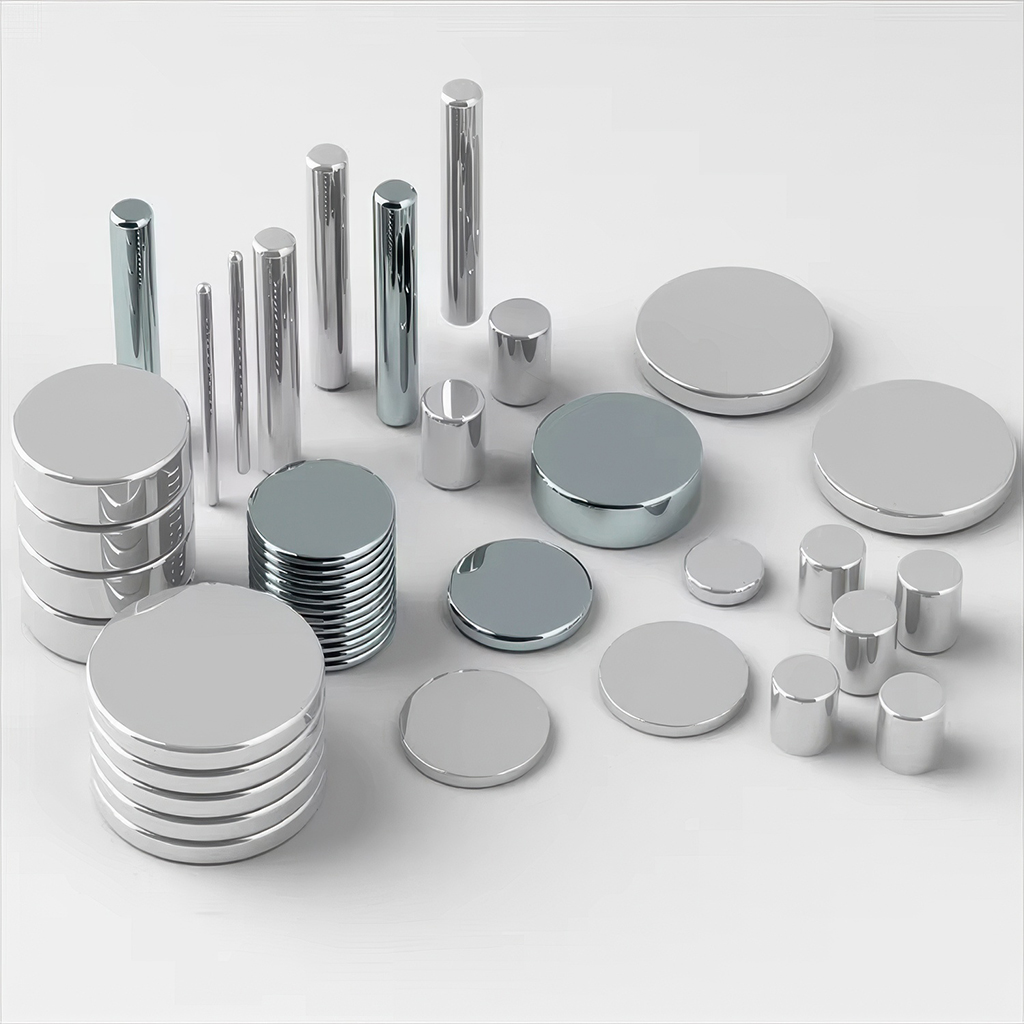