# Hole Magnets for Robotics: Achieving Precision and Performance in Automation
This article explores the crucial role hole magnets play in enhancing the precision and performance of robotic systems. Whether you’re a seasoned robotics engineer or just starting out, this guide will provide valuable insights into selecting, implementing, and optimizing hole magnets for a wide range of robotic applications. Prepare to delve into the world of magnetic solutions and discover how they can transform your robotic projects.
## 1. What Are Hole Magnets and Why Are They Important for Robotics?
Hole magnets, characterized by their central hole or bore, are a specialized type of permanent magnet. They are designed to be mechanically fastened using screws, bolts, or pins. This design feature is particularly important for robotics because it provides a robust and reliable method for integrating magnets into robotic arms, grippers, end-effectors, and other automated systems.
Why are they so important? Because traditional adhesive mounting methods can fail over time due to vibrations, temperature fluctuations, and mechanical stress. Hole magnets offer a far more secure and durable connection, ensuring long-term performance and minimizing downtime.
## 2. How Do Hole Magnets Enhance Precision in Robotic Systems?
Robotics relies on precision for tasks ranging from assembly to inspection. Hole magnets contribute to this precision in several ways:
* **Secure Attachment:** As mentioned earlier, the mechanical fastening provided by the hole minimizes slippage and misalignment, crucial when dealing with sensitive components.
* **Consistent Positioning:** By using precisely manufactured hole magnets and matching hardware, the position of the magnet, and therefore the attached component, can be precisely controlled.
* **Improved Repeatability:** The stability of the magnetic connection ensures that robotic movements are highly repeatable, leading to greater accuracy in automated processes.
Imagine a robotic arm assembling tiny electronic components. Even a slight shift in the magnet’s position could lead to errors. Hole magnets, therefore, are essential for ensuring that the arm consistently places components exactly where they need to be.
## 3. What Materials Are Best for Hole Magnets Used in Robotics?
The choice of magnetic material significantly impacts the performance of hole magnets. Here’s a breakdown of common options:
* **Neodymium (NdFeB):** This is the most powerful type of permanent magnet, offering exceptional strength for its size. It’s ideal for applications requiring high holding force. However, Neodymium magnets can be brittle and susceptible to corrosion, so protective coatings are often necessary.
* **Samarium Cobalt (SmCo):** These magnets offer excellent temperature stability and corrosion resistance, making them suitable for harsh environments where Neodymium magnets might degrade. However, they are generally more expensive and have slightly lower magnetic strength than Neodymium.
* **Ferrite (Ceramic):** Ferrite magnets are a cost-effective option with good corrosion resistance. However, they have lower magnetic strength compared to Neodymium and Samarium Cobalt. They’re often used in applications where cost is a primary concern and high magnetic force is not required.
| Magnet Type | Strength | Temperature Resistance | Corrosion Resistance | Cost |
|—————–|——————|————————|———————-|————|
| Neodymium (NdFeB) | Very High | Moderate | Low (Requires Coating) | Moderate |
| Samarium Cobalt (SmCo) | High | High | High | High |
| Ferrite (Ceramic) | Low | High | High | Low |
The best material depends on the specific requirements of the robotic application, considering factors like strength, temperature, cost, and environmental conditions.
## 4. How Does Holding Force Vary in Different Sizes and Shapes of Hole Magnets?
The holding force of a hole magnet is directly related to its size, shape, and material. Larger magnets, naturally, generate stronger magnetic fields and thus greater holding force.
* **Size:** Increasing the diameter and thickness of the magnet increases the volume of magnetic material, leading to a stronger magnetic field and greater holding force.
* **Shape:** Cylindrical and disc-shaped magnets are common choices. However, specific shapes might be tailored to the application for optimal magnetic flux concentration.
* **Material:** As discussed earlier, the magnetic material itself determines the strength of the magnetic field.
The relationship between size, shape, and holding force is complex and often requires experimentation or simulation to optimize the design for a particular application. Finite Element Analysis (FEA) software can be used to accurately predict the holding force of different magnet designs.
## 5. How to Select the Right Coating for Hole Magnets in Robotic Environments?
Choosing the right coating is critical for protecting hole magnets from corrosion and mechanical damage, especially in demanding robotic environments. Common coatings include:
* **Nickel (Ni):** Provides a good balance of corrosion resistance, hardness, and cost. It’s a popular choice for general-purpose applications.
* **Zinc (Zn):** Offers good corrosion resistance but is less durable than nickel. It’s often used as a lower-cost alternative.
* **Epoxy:** Provides excellent chemical resistance and electrical insulation. It’s suitable for applications involving exposure to harsh chemicals or where electrical isolation is required.
* **Parylene:** A thin, conformal coating that offers excellent protection against moisture and chemicals without significantly altering the magnet’s dimensions.
Consider the specific environmental conditions to which your robotic system will be exposed. For example, if the robot operates in a humid environment, a coating with high corrosion resistance is essential.
## 6. What Design Considerations are Important for Integrating Hole Magnets into Robots?
Integrating hole magnets into robotic systems requires careful planning. Some key considerations include:
* **Mechanical Stability:** Ensuring that the magnet is securely fastened to the robotic component to withstand vibrations and mechanical stress. The size of the hole and the dimensions of the fastening hardware are important.
* **Magnetic Shielding:** Controlling the magnetic field to prevent interference with sensitive electronic components. Shielding materials like mu-metal can be used to contain the magnetic field.
* **Accessibility:** Designing the assembly so that the magnet can be easily accessed and replaced if necessary.
* **Material Compatibility:** Ensuring that the magnet material is compatible with the materials of the robotic component to prevent corrosion or other undesirable interactions.
A well-planned integration strategy ensures that the hole magnets perform reliably and don’t negatively impact the overall performance of the robotic system.
## 7. How Can Finite Element Analysis (FEA) Optimize Hole Magnet Placement for Robotic Applications?
FEA is a powerful tool for simulating the behavior of magnetic fields and optimizing the placement of hole magnets in robotic applications.
* **Predicting Holding Force:** FEA can accurately predict the holding force of different magnet configurations, allowing engineers to select the optimal magnet size and shape.
* **Analyzing Magnetic Flux Distribution:** FEA can visualize the magnetic flux distribution, helping engineers to identify areas of high magnetic field concentration and potential interference.
* **Optimizing Magnet Placement:** FEA can be used to simulate the effects of different magnet placements, allowing engineers to optimize the design for maximum performance.
By using FEA, engineers can avoid costly trial-and-error testing and quickly identify the best magnet configuration for their robotic application.
## 8. What Are Some Case Studies Demonstrating the Successful Use of Hole Magnets in Robotics?
Let’s examine some examples of how hole magnets contribute to success in different robotics scenarios:
* **Automated Assembly:** A manufacturer using robotic arms to assemble electronic components employed hole magnets to securely attach grippers. This resulted in a 20% increase in assembly speed and a significant reduction in errors.
* **Medical Robotics:** In a surgical robot, hole magnets were used to attach delicate surgical instruments. The secure and precise connection provided by the magnets allowed surgeons to perform minimally invasive procedures with greater confidence.
* **Inspection Robots:** A company developing robots for inspecting pipelines used hole magnets to attach sensors to the robot’s chassis. The magnets provided a reliable and easily adjustable mounting solution, allowing the robot to adapt to different pipeline diameters.
These examples demonstrate the versatility and effectiveness of hole magnets in a wide range of robotic applications.
## 9. What Are the Future Trends in Hole Magnet Technology for Robotics?
The field of hole magnets for robotics is constantly evolving. Some emerging trends include:
* **Improved Magnetic Materials:** Research is ongoing to develop new magnetic materials with even higher strength and temperature stability.
* **Additive Manufacturing (3D Printing):** 3D printing is enabling the creation of custom magnet shapes and designs, opening up new possibilities for robotic applications.
* **Smart Magnets:** Integrating sensors and control electronics into hole magnets to provide real-time feedback on magnetic force and position.
These advancements promise to further enhance the precision, performance, and versatility of hole magnets in robotics.
## 10. How Does Temperature Affect The Performance Of Hole Magnets In Robotics?
Temperature significantly impacts the performance of hole magnets. Different materials exhibit varying sensitivity to temperature changes:
* **Curie Temperature:** Each magnetic material has a Curie temperature – the point above which it loses its magnetic properties. Operating near or above this temperature can permanently demagnetize the magnet.
* **Reversible Losses:** Even below the Curie temperature, magnets experience reversible losses in magnetic strength as temperature rises. This loss is typically more pronounced in Neodymium magnets compared to Samarium Cobalt.
* **Irreversible Losses:** Prolonged exposure to high temperatures can cause irreversible demagnetization, even if the temperature is below the Curie temperature.
Therefore, it’s crucial to select a magnet with a Curie temperature significantly higher than the operating temperature of the robot. Active cooling or thermal management strategies may be necessary in high-temperature environments. Statistics show that for every 1°C increase in temperature above 80°C, Neodymium magnets can lose between 0.08% and 0.12% of their magnetic strength.
## Frequently Asked Questions (FAQs)
**What is the best way to clean hole magnets used in robotics?**
Use a soft cloth dampened with isopropyl alcohol. Avoid abrasive cleaners, as they can damage the coating. Make sure the magnet is completely dry before re-installing it.
**How often should hole magnets be inspected in a robotic system?**
Inspect magnets during regular maintenance cycles, checking for signs of corrosion, damage, or loosening. The frequency depends on the application’s severity and environmental conditions.
**Can hole magnets interfere with other components in a robot?**
Yes, magnetic fields can interfere with sensitive electronics and sensors. Shielding might be required in such cases. Properly assess the possible interference and take appropriate measures.
**What is the lifespan of a hole magnet in a robotic application?**
With proper installation and maintenance, hole magnets can last for many years. The lifespan depends on the operating conditions, material composition, and coating used to protect the magnet. Many applications see a lifespan of 10+ years.
**How do I remagnetize a hole magnet that has lost its strength?**
While it’s technically possible to re-magnetize some magnets, it often requires specialized equipment and may not fully restore the original strength. Replacement is generally the more practical and cost-effective approach in most situations.
**Are there safety precautions to consider when working with hole magnets in robotics?**
Yes, strong magnets can pose a pinching hazard. Handle them with care and avoid placing fingers or other body parts between the magnet and a ferrous surface. Magnetic fields may also affect pacemakers and other medical devices.
## Conclusion
Hole magnets are indispensable components for achieving precision and performance in robotics. By understanding their properties, selecting the right materials and coatings, and implementing proper integration strategies, engineers can leverage the power of magnets to enhance the capabilities of robotic systems. Remember these key takeaways:
* **Mechanical Fastening:** Provides a robust and reliable connection.
* **Material Selection:** Optimize for strength, temperature, and environment.
* **Design Considerations:** Account for stability, shielding, and accessibility.
* **Coatings:** Protect against corrosion and damage.
* **FEA Optimization:** Maximize performance through simulation.
* **Temperature Effects:** Acknowledge temperature’s impact on magnetic strength.
By applying these principles, you can unlock the full potential of hole magnets in your robotic projects and achieve superior precision, performance, and reliability.
Hole Magnets for Robotics: Precision and Performance
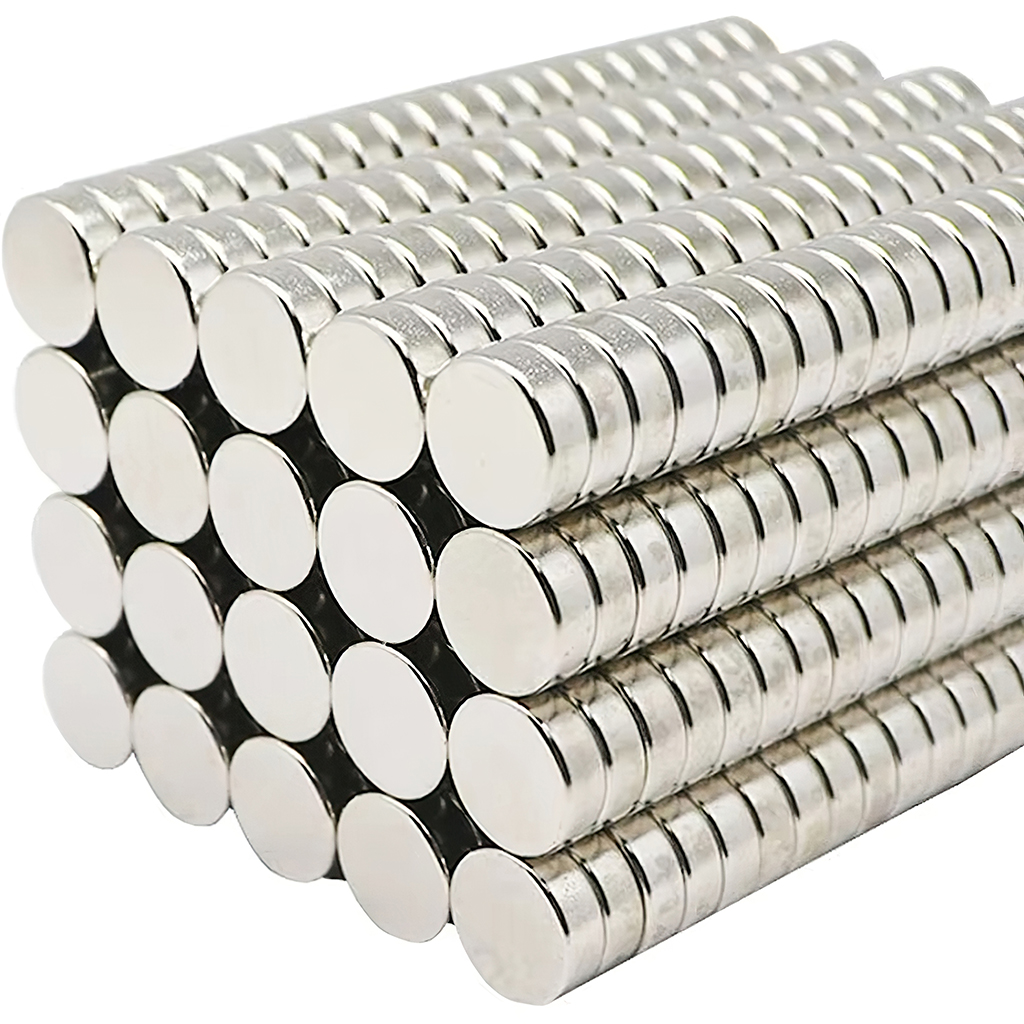