# Hole Magnets in Action: Exploring Diverse Applications Across Industries
Hole magnets, seemingly simple components, play surprisingly vital roles in a wide range of industries. This often-overlooked marvel of engineering offers unique solutions for fastening, positioning, and even creating dynamic assemblies. In this article, I’ll delve into the fascinating world of hole magnets, exploring their diverse applications and uncovering how they contribute to innovation across various sectors. From manufacturing and automotive to healthcare and even art, you’ll discover the power and versatility of these essential magnetic components. Get ready to be amazed by the incredible impact of hole magnets!
## Are Hole Magnets Suitable for High-Temperature Applications?
One of the most frequently asked questions I encounter is about the temperature limitations of hole magnets. While the specific temperature resistance depends on the magnet’s material (neodymium, ferrite, samarium cobalt, etc.), it’s crucial to understand that exceeding their Curie temperature can lead to irreversible demagnetization.
Neodymium magnets, known for their high strength, generally have lower temperature resistance than ferrite magnets. For high-temperature applications, consider using samarium cobalt magnets, which can withstand significantly higher temperatures, albeit at a higher cost and typically lower magnetic strength than Neodymium. Ferrite magnets offer a cost-effective solution for moderate temperatures, but their magnetic strength is considerably lower. Always consult the manufacturer’s specifications to ensure the chosen magnet is suitable for the intended operating temperature range.
## Hole Magnets in Manufacturing: How Do They Streamline Processes?
In the manufacturing sector, hole magnets are crucial for streamlining various processes. Consider, for example, their use in jigs and fixtures. By integrating hole magnets into these tools, manufacturers can quickly and securely position workpieces for welding, drilling, or assembly. This eliminates the need for cumbersome clamps and screws, saving time and improving efficiency.
Furthermore, hole magnets play a pivotal role in robotic automation. End-of-arm tooling equipped with hole magnets enables robots to pick and place components with precision and speed. Imagine a robotic arm effortlessly lifting and positioning metal panels in an automotive assembly line, all thanks to the power of precisely placed hole magnets. This significantly enhances productivity and reduces the risk of human error.
## Automotive Applications of Hole Magnets: Where Are They Used?
The automotive industry leverages hole magnets in various clever ways. One common application is in sensors. Hole magnets are used in proximity sensors to detect the position of components such as crankshafts and camshafts. This information is crucial for engine management and control.
Another application can be found in fluid level sensors. A float containing a hole magnet moves up or down in response to the fluid level, triggering a sensor that indicates the fill level. This is used in fuel tanks, oil reservoirs, and coolant systems. They can even be found in holding components within the interior of vehicles, such as trim pieces being held on with minimal exposed hardware.
## Medical Device Applications of Hole Magnets: Enhancing Precision and Safety
The medical device industry benefits significantly from the unique properties of hole magnets. Their precision and reliability are paramount in critical applications. One notable example is in MRI (Magnetic Resonance Imaging) machines. While the large magnets responsible for the imaging are not strictly “hole magnets,” smaller hole magnets can be used in the internal mechanisms and sensors within the machine.
More directly, in the future hole magnets could potentially be used to provide directional control assistance for magnetically guided capsules through the body. Additionally, miniature hole magnets find their way into implantable medical devices, such as hearing aids and drug delivery systems. Their small size and powerful magnetic properties make them ideal for these applications.
| Application | Description | Benefits |
| ———————- | ———————————————————————————————– | ———————————————————————————————— |
| MRI Machines | Used in sensors and mechanisms (indirectly). | Enhanced imaging accuracy and reliability. |
| Medical Implants | Miniaturized magnets in hearing aids and drug delivery systems. | Compact design, reliable operation, and precise drug delivery. |
| Magnetically Guided Capsules | Potential use for directional control within the body. | Minimally invasive procedures and targeted treatment. |
## Securing Art and Displays with Hole Magnets: A Creative Solution
Beyond industrial applications, hole magnets offer creative solutions for securing art and displays. Instead of using nails or screws that can damage surfaces, hole magnets can be discreetly attached to the back of artworks or displays, allowing them to be easily mounted on metal surfaces.
Consider a gallery showcasing sculptures. By embedding hole magnets in the base of each sculpture, the artist can easily arrange and rearrange the display on a metal platform, creating dynamic exhibits without the need for permanent fixtures. This versatility and ease of use make hole magnets a popular choice for artists and designers.
**Case Study: Museum Display using Hole Magnets**
A local museum recently implemented a new display system for its rotating exhibits. They attached steel plates to the walls and embedded hole magnets in the backs of the display cases. This allowed them to quickly change exhibits without damaging the walls or requiring specialized labor. The curator reported a significant reduction in setup time and cost, along with improved flexibility in display design.
## How Do Hole Magnets Compare to Other Fastening Methods?
Compared to traditional fastening methods like screws, bolts, and adhesives, hole magnets offer several advantages. They provide a non-destructive attachment that can be easily repositioned or removed without leaving any marks or damage. They also allow for quick assembly and disassembly, saving time and effort.
However, hole magnets also have limitations. Their holding force is limited by the magnet’s size, material, and the surface it’s attached to. They are not suitable for applications that require extremely high load-bearing capacity. Screws and bolts, on the other hand, offer a more secure and permanent connection.
Here’s a quick comparison:
* **Hole Magnets:** Quick, repositionable, non-destructive, limited holding force.
* **Screws/Bolts:** Secure, permanent, high load-bearing capacity, requires tools, can damage surfaces.
* **Adhesives:** Permanent, can be used on various materials, can be messy, can damage surfaces upon removal.
## Choosing the Right Hole Magnet: What Factors Should I Consider?
Selecting the appropriate hole magnet for a specific application requires careful consideration of several factors. These include the required holding force, the operating temperature, the environmental conditions, and the size and shape limitations.
* **Holding Force:** This is the most critical factor. Determine the weight or force the magnet needs to withstand.
* **Magnet Material:** Choose a material that meets the temperature and corrosion resistance requirements. Neodymium magnets are powerful but sensitive to heat and corrosion. Ferrite magnets are more resistant but have lower strength.
* **Size and Shape:** Select a size and shape that fits the available space and provides the desired holding force.
* **Coating:** Consider a coating to protect the magnet from corrosion, especially in harsh environments.
## How Strong Is a Hole Magnet? Defining Pull Force
“Pull force” is the standard measurement for a hole magnet’s strength, representing the force required to detach the magnet when pulled directly away from a flat steel surface under ideal conditions. This force is measured in pounds (lbs) or kilograms (kg).
However, it’s crucial to understand that the actual holding force in a real-world application can be significantly lower than the stated pull force. Factors such as the surface finish, the presence of air gaps, and the angle of pull can all affect the holding force. A magnet that is pulled sideways, for instance, will have a dramatically reduced holding force than on a direct pull. Therefore, it’s always wise to overestimate the required pull force to ensure a secure and reliable connection.
## What’s the Difference Between Neodymium and Ferrite Hole Magnets?
Neodymium and ferrite magnets are the two most commonly used types of hole magnets, each with its own distinct properties and applications. Neodymium magnets, also known as “rare earth” magnets, offer significantly higher magnetic strength compared to ferrite magnets. This makes them ideal for applications where size and weight are critical.
However, neodymium magnets are more expensive and more susceptible to corrosion and high-temperature demagnetization. Ferrite magnets, on the other hand, are more affordable, corrosion-resistant, and can withstand higher temperatures. Their lower strength makes them suitable for applications where high holding force is not required.
Here’s a table summarizing the key differences:
| Feature | Neodymium Magnets | Ferrite Magnets |
| ——————– | ———————————- | ————————————— |
| Magnetic Strength | Very High | Low |
| Cost | High | Low |
| Temperature Resistance | Lower | Higher |
| Corrosion Resistance | Lower (requires coating) | Higher |
| Typical Applications | High-performance applications, small devices | Cost-effective solutions, speakers, motors |
## Future Trends in Hole Magnet Technology: What’s Next?
The field of magnet technology is constantly evolving, with ongoing research and development focused on improving magnet performance and expanding their applications. One promising trend is the development of new magnetic materials with higher energy products and improved temperature stability.
Another area of innovation is in the design and manufacturing of magnet assemblies. Advanced manufacturing techniques, such as additive manufacturing (3D printing), are enabling the creation of complex magnet shapes and integrated assemblies, opening up new possibilities for magnet applications. As technology advances, hole magnets will continue to play an increasingly important role in various industries.
## Frequently Asked Questions (FAQs)
**How can I protect hole magnets from corrosion?**
Apply a protective coating such as nickel, epoxy, or Parylene. The best coating depends on the specific environment and the level of protection required.
**Can I cut or drill hole magnets?**
It is strongly discouraged to cut or drill hole magnets, especially neodymium magnets. This can generate heat, causing demagnetization and potentially hazardous sparks.
**How do I measure the pull force of a hole magnet?**
Use a pull tester, a device designed to measure the force required to detach a magnet from a steel surface. This provides a more accurate measurement than relying solely on the magnet’s specifications.
**What is the best way to store hole magnets?**
Store magnets in a cool, dry place away from other magnetic materials and sensitive electronic devices. This prevents loss of magnetization and accidental attraction.
**Are hole magnets safe to use around electronic devices?**
Hole magnets can interfere with sensitive electronic devices like pacemakers, credit cards with magnetic strips, and computer hard drives. Keep magnets away from these devices to avoid damage or malfunction.
**Can I use multiple hole magnets to increase the holding force?**
Yes, using multiple magnets can increase the total holding force. However, the increase is not always linear, as factors such as spacing and alignment can affect the overall performance.
## Conclusion
Hole magnets, despite their unassuming appearance, are indispensable components that drive innovation across numerous industries. From streamlining manufacturing processes and enhancing automotive systems to enabling cutting-edge medical devices and creative art installations, their versatility and reliability are undeniable.
Here are the key takeaways:
* Hole magnets are used in a wide range of industries including manufacturing, automotive , medical, and art.
* The choice of magnet type (Neodymium vs Ferrite) depends on the application and the required strength, temperature resistance and budget.
* Pull force indicates the magnets strength but is only an estimate.
* Hole magnets can be used in creative ways for securing displays without causing damage.
* Factors like temperature, corrosion and proper storage can impact the life and function of Hole Magnets.
Hole Magnets in Action: Diverse Applications Across Industries
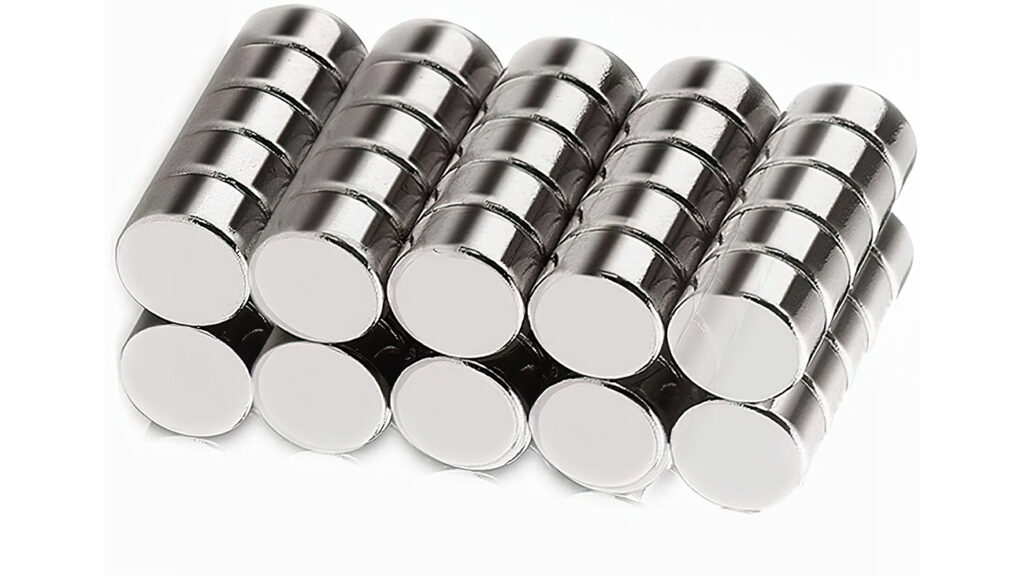