# Magnet Heavy Materials: A Performance Comparison for Optimal Applications
Magnets are essential components in countless technologies, from the speakers in our phones to the massive generators powering our cities. But not all magnets are created equal. This article explores the world of magnet heavy materials, delving into their properties, performance characteristics, and the best applications for each. We’ll compare and contrast different types of these powerful materials, providing you with the knowledge to make informed decisions for your specific needs. Consider this your comprehensive guide to navigating the complex landscape of magnet heavy materials.
## What Are Magnet Heavy Materials and Why Are They Important?
Magnet heavy materials, often referred to as hard magnetic materials or permanent magnets, possess a high coercivity and remanence. This means they resist demagnetization effectively and retain a strong magnetic field even after the external magnetizing force is removed. Think of them as the rockstars of the magnet world, holding their magnetism with unwavering strength. They are critical because they provide a stable and reliable magnetic field without requiring constant power, making them indispensable in a vast range of applications. Their high energy product also allows for miniaturization – more magnetic power in a smaller package.
Consider, for instance, electric motors. They rely heavily on permanent magnets to create the rotating force that drives everything from electric vehicles to washing machines. Without these strong, reliable magnets, modern technology as we know it would be drastically different. The continuous improvement in the performance of magnet heavy materials is driving innovation in countless industries.
## Which Magnet Heavy Materials Offer the Best Performance? A Comparative Overview
The magnet heavy materials landscape consists of several key players, each with its unique blend of properties and performance characteristics. Let’s compare the main contenders: Neodymium Iron Boron (NdFeB), Samarium Cobalt (SmCo), Alnico, and Ferrite magnets. Understanding their strengths and weaknesses is key to selecting the right material. The best choice depends entirely on the specific application’s requirements regarding strength, temperature, cost, and other factors.
**Table 1: Comparison of Magnet Heavy Materials**
| Material | Energy Product (BHmax) (MGOe) | Coercivity (Hci) (kOe) | Temperature Stability | Corrosion Resistance | Cost | Common Applications |
|—————-|———————————|————————–|———————–|———————–|———|————————————————————————————–|
| NdFeB | 30-55 | 10-30 | Moderate | Poor (requires coating) | High | Electric vehicles, wind turbines, hard disk drives, MRI machines |
| SmCo | 16-32 | 10-30 | Excellent | Good | Very High | Aerospace, military applications, high-temperature sensors |
| Alnico | 1-10 | 0.5-2.5 | Excellent | Good | Moderate | Loudspeakers, guitar pickups, sensors, holding magnets |
| Ferrite (Ceramic) | 1-5 | 2-5 | Good | Excellent | Low | Electric motors (small), speakers, magnetic separators, refrigerator magnets |
## How Does Neodymium Iron Boron (NdFeB) Stack Up Against the Competition?
NdFeB magnets are the undisputed champions in terms of magnetic strength. They boast the highest energy product (BHmax), meaning they can pack the most magnetic force into the smallest volume. This makes them ideal for applications requiring high performance in a compact size, such as in electric vehicle motors, where space and weight are critical.
However, NdFeB magnets have some limitations. Relatively speaking, they have lower temperature stability compared to SmCo magnets; their properties degrade significantly at higher temperatures. They are also prone to corrosion, requiring protective coatings like nickel or epoxy. Despite these drawbacks, their unmatched strength often makes them the preferred choice for demanding applications.
## Why is Samarium Cobalt (SmCo) So Popular for High-Temperature Applications?
Samarium Cobalt (SmCo) magnets shine when endurance is paramount. Unlike NdFeB, SmCo maintains its magnetic properties at extremely high temperatures, making it suitable for aerospace, military applications, and other environments where heat is a major concern. They also have superior corrosion resistance compared to NdFeB, minimizing the need for protective coatings in harsh conditions.
The downside of SmCo is its high cost and lower energy product compared to NdFeB. Finding the right SmCo alloy can be challenging, and it’s important to consider the specific temperature ranges and expected performance degradation. However, if long-term stability under extreme thermal stress is the primary focus, SmCo is often the best selection.
## What Makes Alnico a Reliable Choice for Specific Applications?
Alnico magnets offer a unique combination of temperature stability and relative affordability. They excel in applications where consistent performance over a wide temperature range is crucial, such as in sensors, holding magnets, and certain types of electric motors. Furthermore, they can be manufactured into intricate shapes relatively easily.
While Alnico has excellent temperature stability, its lower energy product compared to NdFeB and SmCo makes it unsuitable for applications demanding utmost magnetic strength. Be aware that they are susceptible to demagnetization if exposed to strong opposing fields. If longevity over sheer power is the priority, Alnico provides a reliable middle ground.
## Why Are Ferrite Magnets So Commonly Used in Everyday Items?
Ferrite magnets, also known as ceramic magnets, are the workhorses of the magnet world. Highly affordable and possessing excellent corrosion resistance, they are ubiquitous in everyday items like speakers, refrigerator magnets, and small electric motors. Their cost-effectiveness enables mass production and widespread integration into various consumer products.
Ferrite magnets have the lowest energy product among the materials discussed, which limits their application in areas needing high magnetic strength. However, their resistance to demagnetization and rust makes them ideal for educational purposes and in environments where durability is more important than power.
## What Role Does Magnetic Domain Alignment Play in Performance?
The magnetic properties of a magnet heavily depend on the alignment of its magnetic domains. Magnetic domains are small regions within the material where the individual atomic magnetic moments are aligned. In an unmagnetized material, these domains are randomly oriented, cancelling each other out.
To create a permanent magnet, manufacturers apply a strong external magnetic field, forcing these domains to align in the same direction. The level of alignment achieved directly impacts the magnet’s remanence (the strength of the magnetic field it retains after the external field is removed) and coercivity (its resistance to demagnetization). The more perfectly aligned the domains, the stronger and more stable the magnet.
**Diagram: Magnetic Domain Alignment**
[Imagine a diagram here showing a material with randomly aligned magnetic domains, followed by a diagram showing the same material with all domains aligned after exposure to an external magnetic field.]
## How Does Processing Affect the Final Properties of Magnet Heavy Materials?
The manufacturing process significantly influences the final properties of magnet heavy materials. Techniques like sintering, hot pressing, and powder metallurgy are employed to create dense, uniform magnets with controlled grain sizes and orientations. The choice of manufacturing process depends on the specific material and desired magnetic characteristics.
For example, using powder metallurgy, finely ground magnetic material is compressed and then heated to near the melting point (sintered). Controlling the sintering temperature and atmosphere is critical in achieving the optimal density and grain structure for maximum magnetic performance. Fine grain control, in particular, can lead to increased resistance to demagnetization.
## What Emerging Materials Are Poised to Improve Magnet Performance?
Research into new magnet heavy materials is ongoing, driven by the demand for stronger, more temperature-stable, and cost-effective magnets. Current promising research aims at:
* **Rare-earth-reduced magnets**: These seek to minimize or even eliminate dependence on rare-earth elements like neodymium and dysprosium, which are subject to geopolitical concerns and price volatility. Composites based on manganese-bismuth or iron-nitride are some avenues being explored.
* **Nanocomposite magnets**: Combining different magnetic phases at the nanoscale creates materials with enhanced properties. By carefully controlling the size and distribution of the phases, we can tune the properties for specific applications.
* **High-entropy alloys**: These alloys incorporate multiple elements in near-equal proportions, resulting in unique microstructures and properties. Exploring high-entropy compositions containing magnetic elements is a burgeoning field.
## Can We Achieve Sustainable Magnet Production in the Future?
Sustainability is a growing concern in magnet production, particularly for rare-earth magnets. The extraction and processing of rare-earth elements can have significant environmental impacts. Currently, steps can be taken to lower environmental impact via:
1. **Recycling magnets**: Efficient recycling processes enable the recovery of valuable rare-earth elements from end-of-life products, reducing the demand for newly mined materials. Many companies and research groups are investigating these processes.
2. **Optimizing magnet designs**: Applying innovative designs can minimize the amount of magnetic material needed for a given application, thereby reducing consumption and waste.
3. **Developing alternative materials**: Prioritizing research and development into rare-earth-free magnetic materials that have minimal environmental impact.
## Case Study: Magnet Heavy Materials in Electric Vehicle Motors
Electric vehicles (EVs) rely heavily on high-performance magnets in their electric motors. NdFeB magnets are the dominant choice due to their superior energy product, delivering high torque and power density. However, increasing demand for EVs and the fluctuating prices of rare-earth elements have spurred interest in alternative solutions.
Some manufacturers are exploring alternative motor designs that reduce reliance on rare-earth magnets, such as synchronous reluctance motors, and interior permanent magnet synchronous reluctance motors. These designs present a less expensive, more sustainable option but often have lower torque. The future holds design innovations that balance sustainability with performance in electric vehicle motors.
##よくある質問(FAQ)
How do I choose the right magnet material for my application?
Consider the specific requirements of your application. Key factors include magnetic strength, temperature stability, corrosion resistance, size constraints, and cost. Evaluate the trade-offs between different materials and consider testing prototypes to ensure optimal performance.
What are the main environmental concerns associated with rare-earth magnet production?
The extraction and processing of rare-earth elements can lead to water pollution, soil contamination, and radioactivity. Responsible mining practices and robust recycling programs are crucial in mitigating these environmental impacts.
What protective coatings are commonly used for NdFeB magnets?
Nickel and epoxy coatings are widely used to protect NdFeB magnets from corrosion. These coatings create a barrier that prevents oxidation and degradation of the magnetic material.
Can magnet strength be improved indefinitely?
No, there are theoretical limits to magnet strength dictated by the fundamental properties of materials and the laws of physics. However, ongoing research focuses on pushing these boundaries by developing new materials and optimizing manufacturing processes.
How does temperature affect magnet performance?
Temperature can significantly affect magnet performance. Most magnet materials lose some of their magnetic strength as temperature increases. SmCo magnets exhibit the best temperature stability, while NdFeB magnets are more sensitive to heat.
Are there any safety precautions I should take when handling strong magnets?
Yes, strong magnets can pose safety hazards. They can pinch skin, damage electronic devices, and interfere with pacemakers. Always handle magnets with care and keep them away from sensitive equipment. Shielding strong magnets can also help contain their electromagnetic field to improve safety.
##結論
The world of magnet heavy materials is diverse and constantly evolving. Understanding the strengths and weaknesses of different materials is crucial for selecting the optimal solution for any given application. Key takeaways include:
* **NdFeB:** Highest magnetic strength, but lower temperature stability and corrosion resistance.
* **SmCo:** Excellent temperature stability and corrosion resistance, but more expensive.
* **Alnico:** Good temperature stability and relatively affordable.
* **Ferrite:** Low cost and excellent corrosion resistance.
* **Sustainable solutions:** Increasing emphasis on recycling, optimized designs, and alternative materials to minimize environmental impact.
By carefully considering these factors and staying abreast of the latest advancements, engineers and designers can harness the power of magnet heavy materials to create innovative and efficient solutions for a wide range of applications.
Magnet Heavy Materials: A Comparative Study of Performance
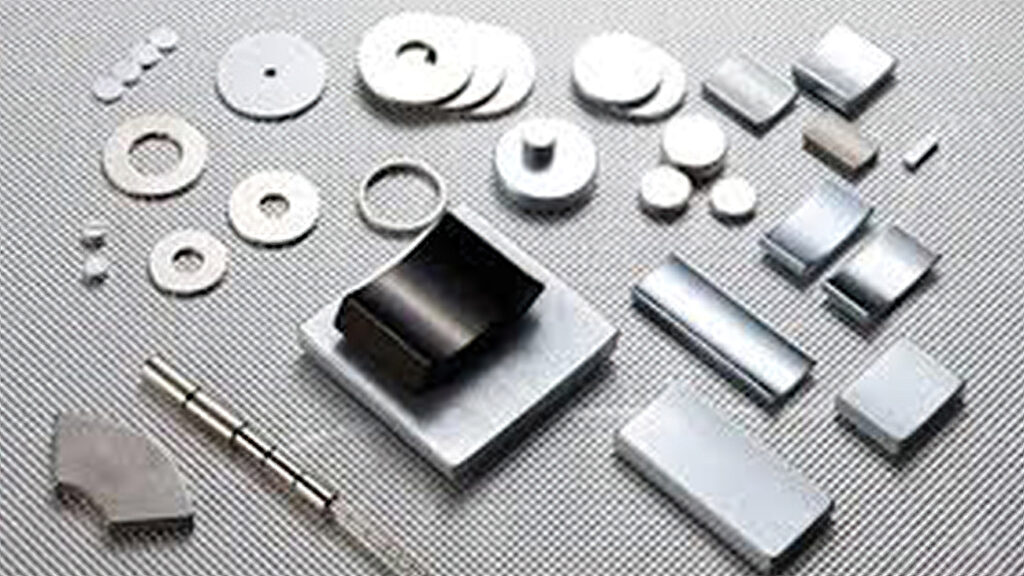