# Beyond Glue: Unveiling Innovative Magnet Fastening Methods for Secure Applications
Magnets are indispensable tools in countless applications, from holding notes on refrigerators to powering complex machinery. However, simply relying on glue to attach magnets can be unreliable, messy, and prone to failure. This article explores innovative and effective methods for fastening magnets, going “beyond glue” to ensure secure and long-lasting connections. We’ll delve into mechanical fasteners, molding techniques, specialized adhesives, and much more, providing you with a comprehensive guide to choosing the best method for your specific needs. This is a valuable read because it empowers you to create more robust and reliable magnetic assemblies, avoiding common pitfalls associated with traditional glue-based solutions.
## Why Are Traditional Glues Often Insufficient for Magnet Fastening?
Traditional adhesives, while convenient, frequently fall short when it comes to securely fastening magnets. There are several key reasons for this:
* **Limited Strength:** Glues designed for general purposes often lack the necessary strength to withstand the constant pull or shear forces exerted by magnets, especially neodymium magnets, which are known for their powerful attraction.
* **Lack of Durability:** Environmental factors such as temperature changes, humidity, and exposure to chemicals can degrade glue over time, leading to weakened bonds and eventual failure.
* **Incompatibility:** Not all surfaces are compatible with every type of glue. The smooth, non-porous surfaces of magnets and the materials they are being attached to can make it difficult for adhesives to form a strong, lasting bond.
* **Potential for Damage:** Some aggressive glues can damage sensitive materials, including the magnet’s coating, leading to corrosion and reduced magnetic strength.
Therefore, exploring alternative fastening methods is crucial for achieving optimal performance and longevity in magnetic applications.
## Are Mechanical Fasteners a Reliable Alternative for Magnet Attachment?
Absolutely! Mechanical fasteners, such as screws, rivets, and clips, offer a remarkably strong and reliable alternative to glue for attaching magnets. They create a physical connection that is much less susceptible to environmental factors and shear forces.
* **Screws:** Using screws to fasten magnets is a straightforward and reversible method. You can embed the magnet in a plastic or metal housing with screw holes, allowing for easy attachment to any surface. Counter-sunk screws provide a flush, clean look. Ensure that you use non-magnetic screws like those made from stainless steel to avoid interfering with the magnet’s field.
* **Rivets:** Rivets provide a permanent and incredibly strong bond. They are ideal for applications where the magnet needs to be securely attached to a sheet metal or other thin materials. The rivet is inserted through pre-drilled holes in both the magnet housing and the target material, then deformed to create a tight, unwavering connection.
* **Clips:** Clips offer a versatile and often adjustable solution. Specially designed clips can be used to hold magnets in place, allowing for quick installation and removal. These are especially valuable in applications requiring frequent maintenance or reconfiguration. For example, I used clips to attach magnets to a whiteboard for creating a modular display system, and it worked perfectly!
**Table: Comparison of Mechanical Fasteners**
| Fastener Type | Strength | Reversibility | Application Examples | Considerations |
|—|—|—|—|—|
| Screws | High | Yes | Mounting magnets in displays, attaching to equipment | Use non-magnetic screws |
| Rivets | Very High | No | Securing magnets to sheet metal, heavy-duty applications | Requires specialized tools for installation|
| Clips | Moderate | Yes | Temporary mounting, adjustable systems | Choose clips rated for magnet force|
## How Can Molding Techniques Integrate Magnets Directly into Components?
Molding techniques, such as injection molding and overmolding, allow for the direct integration of magnets into plastic or rubber components. This eliminates the need for secondary fastening methods and creates a seamless, robust assembly.
* **Injection Molding:** During injection molding, the magnet is placed inside the mold cavity, and molten plastic is injected around it. As the plastic cools and solidifies, it encapsulates the magnet, creating a permanent and extremely strong bond. This method is ideal for high-volume production runs.
* **Overmolding:** Overmolding involves molding a second layer of material (often plastic or rubber) directly onto an existing magnet. This process can be used to create a protective coating around the magnet, improve its grip, or provide a customized shape. I’ve seen overmolding used to create magnetic rubber feet for appliances, which prevent scratching and provide a secure hold.
Molding offers several key advantages, including design flexibility, improved durability, and enhanced aesthetics. By embedding magnets directly into components, you can create parts that are both functional and visually appealing.
## What Role Do Specialized Adhesives Play in Strong Magnet Bonding?
While traditional glues often fail, specialized adhesives designed specifically for magnet bonding can provide surprisingly strong and durable connections. These adhesives are formulated to address the specific challenges associated with bonding magnets, such as smooth surfaces, thermal expansion, and shear forces.
* **Epoxy Adhesives:** Epoxies are known for their exceptional strength, chemical resistance, and ability to bond to a wide variety of materials. Two-part epoxy adhesives offer the best performance for magnet bonding, as they cross-link to form a rigid, high-strength bond.
* **Cyanoacrylate Adhesives (Super Glue):** While standard super glues may not be ideal, specialized cyanoacrylate adhesives formulated for bonding magnets and metals can provide a quick and surprisingly strong bond, especially when combined with a primer. They are easy to use and cure rapidly.
* **Acrylic Adhesives:** Acrylic adhesives offer a good balance of strength, flexibility, and durability. They are particularly well-suited for bonding magnets to plastics and other non-metallic materials.
When selecting a specialized adhesive, consider factors such as the materials being bonded, the operating temperature, and the required strength and durability.
**Statistic:** According to a study by 3M, specialized acrylic adhesives can provide up to 3x the bond strength of traditional adhesives when bonding magnets to metal surfaces.
## How Does the Surface Treatment of Magnets and Materials Affect Bond Strength?
The surface treatment of both the magnet and the material it is being attached to plays a significant role in the success of any fastening method, especially when using adhesives. Proper surface preparation ensures a clean, compatible surface for bonding.
* **Cleaning:** Thoroughly cleaning both surfaces to remove any oil, grease, dirt, or other contaminants is essential. Use a solvent such as isopropyl alcohol or acetone to clean the surfaces, then allow them to dry completely.
* **Abrasion:** Lightly abrading the surfaces with sandpaper or a Scotch-Brite pad can create a mechanical key that enhances adhesion. This is particularly important for smooth, non-porous surfaces. I’ve found that lightly sanding the surface of a neodymium magnet increases the adhesive’s grip significantly.
* **Priming:** Applying a primer specifically designed for bonding magnets or metals can further improve adhesion. Primers promote better wetting and create a chemical bond between the adhesive and the surface.
By investing in proper surface preparation, you can significantly improve the strength and durability of your magnet bonds.
## Should Welding Be Considered for Magnet Attachment in Specific Applications?
Welding, while less common, can be a viable option for attaching magnets to metal structures in specific high-strength applications. However, it’s crucial to understand the limitations and potential risks involved.
* **Laser Welding:** Laser welding offers a precise and controlled method for bonding magnets to metal housings. It minimizes heat input, reducing the risk of demagnetization.
* **Resistance Welding:** Resistance welding uses electrical current to create a localized weld. It’s suitable for joining magnets to thin sheets of metal.
**Important Considerations:**
* **Demagnetization:** The high temperatures involved in welding can cause demagnetization of the magnet, reducing its strength. Careful heat management and specialized welding techniques are necessary to minimize this risk.
* **Magnet Type:** Not all magnets are suitable for welding. Ferrite magnets, for example, are more susceptible to demagnetization than neodymium magnets.
* **Material Compatibility:** The materials of the magnet and the target structure must be compatible for welding.
Welding is best suited for applications that require very high strength and durability, but careful planning and execution are essential to avoid damage to the magnet.
## What is the Role of Encapsulation in Protecting Magnet Fastenings?
Encapsulation involves completely encasing the magnet and its attachment point in a protective material, such as epoxy resin or polyurethane. This provides several benefits:
* **Environmental Protection:** Encapsulation shields the magnet and its bond from moisture, chemicals, and other environmental factors that can degrade the bond over time.
* **Vibration Damping:** The encapsulating material can dampen vibrations, reducing stress on the bond and preventing premature failure.
* **Improved Durability:** Encapsulation enhances the overall durability of the magnetic assembly, making it more resistant to impact and abrasion.
Encapsulation is particularly useful in harsh environments or in applications where the magnet is subjected to significant stress.
**Example:** Encapsulating magnets used in electric motors protects them from vibration and the operating temperature, significantly extending their lifespan.
## How Can Magnetic Shielding Enhance the Performance of Magnet Fastening?
In certain applications, it may be necessary to control or contain the magnetic field. Magnetic shielding involves using materials with high permeability to redirect the magnetic field, preventing it from interfering with nearby components or devices.
* **Shielding Materials:** Common shielding materials include Mu-metal, permalloy, and high-permeability steels. These materials are designed to absorb and redirect magnetic fields.
* **Shielding Techniques:** Shielding can be achieved by enclosing the magnet in a shielded housing or by applying a layer of shielding material directly to the magnet.
By carefully implementing magnetic shielding, you can optimize the performance of your magnetic assembly and prevent interference with sensitive electronics or instruments.
**Diagram:** A simple drawing would show a magnet surrounded by a shielding material diverting the magnetic field lines.
## Case Study: Innovative Magnet Fastening in Automotive Applications.
The automotive industry relies heavily on magnets for various applications, from sensors to electric motors. Innovative fastening methods are crucial for ensuring the reliability and performance of these components.
* **Sensor Mounting:** Automotive sensors often use magnets to detect position or speed. Molding techniques are used to embed the magnets directly into the sensor housing, creating a robust and environmentally sealed assembly.
* **Electric Motor Components:** Electric motors use powerful magnets to generate torque. Specialized adhesives and mechanical fasteners are used to securely attach these magnets to the rotor and stator, ensuring efficient and reliable operation.
* **Attachment of External Accessories:** Magnets are used to attach external accessories, such as light bars or antennas. The magnets are often encapsulated in rubber or plastic housings to provide a secure grip and prevent scratching the vehicle’s surface. Combining the power of magnets and clever fastening methods provides an incredible versatile and useful platform for automotive customization and design.
This exemplifies how creative and robust fastening techniques can make all the difference in complex real-world scenarios.
## What Future Innovations Can We Expect in Magnet Fastening Technologies?
The field of magnet fastening is constantly evolving, with new materials, techniques, and technologies emerging regularly. Some potential future innovations include:
* **Advanced Adhesives:** Development of new adhesives with even higher strength, durability, and temperature resistance. Tailored for extreme use cases with the use of nano-materials in the adhesive matrix.
* **3D-Printed Magnet Housings:** 3D printing allows for the creation of complex and customized magnet housings with integrated fastening features.
* **Smart Magnet Integration:** Incorporating sensors and communication capabilities directly into magnetic assemblies to monitor performance and provide real-time feedback.
* **Recycled Materials:** Increased use of recycled materials in magnet housings and fastening components, promoting sustainability.
These innovations will further expand the possibilities for using magnets in a wide range of applications, enabling more efficient, reliable, and sustainable designs.
##よくある質問(FAQ)
What type of adhesive is best for bonding neodymium magnets to metal?
Two-part epoxy adhesives generally offer the best combination of strength, durability, and chemical resistance for bonding neodymium magnets to metal. Cyanoacrylate adhesives specifically formulated for metal bonding can also provide good results, especially when used with a primer.
How do I prevent magnets from demagnetizing during welding?
Minimize heat input by using laser welding or resistance welding. Use a heat sink to dissipate heat away from the magnet, and avoid prolonged exposure to high temperatures. Choose magnets with high Curie temperatures (the temperature at which a magnet loses its magnetism).
What are the best practices for cleaning magnet surfaces before bonding?
Use a solvent such as isopropyl alcohol or acetone to remove any oil, grease, dirt, or other contaminants. Allow the surfaces to dry completely before applying adhesive or mechanical fasteners. For smooth surfaces, lightly abrade them with sandpaper or a Scotch-Brite pad to create a mechanical key.
Can I use magnets to attach items to painted surfaces without damaging the paint?
Yes, you can use magnets with a soft, protective coating, such as rubber or silicone, to minimize the risk of scratching or damaging the paint. You can also use magnetic sheet with an adhesive backing, which can be easily removed without damaging the paint. I personally prefer using a thin fabric barrier between the magnet and the painted surface for added protection.
Are mechanical fasteners always stronger than adhesives for magnet attachments?
Not necessarily. While mechanical fasteners generally offer higher ultimate strength, specialized adhesives designed for magnet bonding can provide comparable or even superior performance in certain applications, particularly when subjected to shear forces or vibration. The best option depends on the specific requirements of the application.
How do I choose the right magnet material for my application?
Consider factors such as the required strength, operating temperature, size, and cost. Neodymium magnets offer the highest strength but are more susceptible to corrosion and demagnetization at high temperatures. Ferrite magnets are more resistant to corrosion and temperature but have lower strength. Samarium cobalt magnets offer a good balance of strength and temperature resistance but are more expensive.
##結論:キーポイント
* Traditional glues are often insufficient for reliably fastening magnets due to limited strength and durability.
* Mechanical fasteners, such as screws, rivets, and clips, offer a strong and reversible alternative to glue.
* Molding techniques allow for the direct integration of magnets into components, creating seamless and robust assemblies.
* Specialized adhesives designed for magnet bonding can provide surprisingly strong and durable connections.
* Surface treatment of magnets and materials is crucial for optimizing bond strength.
* Welding can be an option for high-strength applications, but care must be taken to prevent demagnetization.
* Encapsulation protects magnet fastenings from environmental factors and vibration.
* Magnetic shielding can enhance the performance of magnet fastening by controlling the magnetic field.
* The future of magnet fastening will likely involve advanced adhesives, 3D-printed housings, and smart integration.
By understanding the various innovative methods available for fastening magnets, you can create more reliable, durable, and efficient magnetic assemblies for a wide range of applications. Remember to carefully consider the specific requirements of your project and choose the method that best meets those needs.
Beyond Glue: Innovative Ways to Fasten Magnets
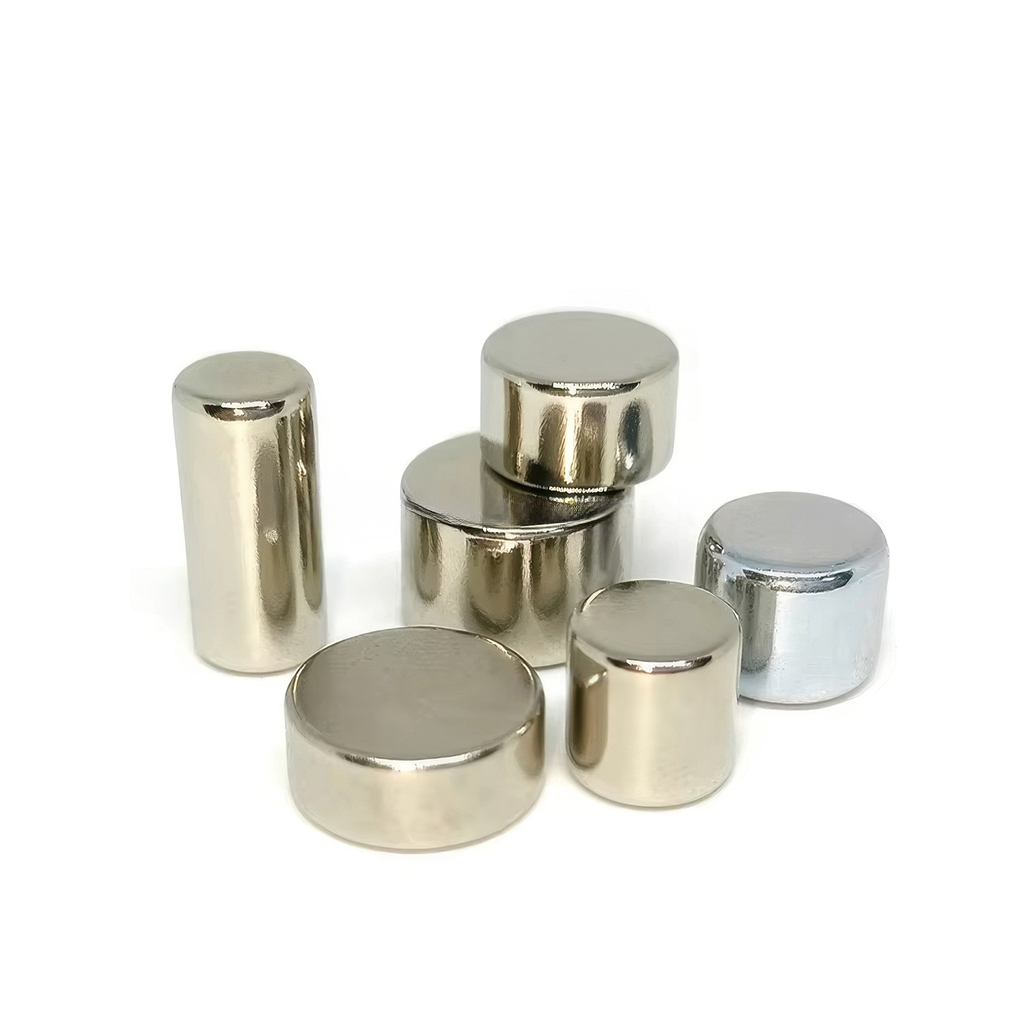