# Analyzing the Properties of Magnet Heavy Alloys: A Deep Dive
Magnet heavy alloys are crucial materials in numerous high-tech applications, from electric vehicle motors to medical imaging equipment. Their exceptional magnetic performance makes them indispensable, but understanding their properties is key to optimizing their use. This article provides a comprehensive analysis of these alloys, exploring their composition, magnetic characteristics, mechanical behavior, and environmental considerations. Whether you’re an engineer, researcher, or simply curious about materials science, this guide will offer valuable insights into the fascinating world of magnet heavy alloys.
## Why are Magnet Heavy Alloys So Important?
Magnet heavy alloys, primarily composed of rare earth elements like neodymium (Nd) or samarium (Sm) combined with iron (Fe) and boron (B) or cobalt (Co), offer unparalleled magnetic strength. This exceptional performance stems from their unique crystalline structures and electronic configurations. This strength allows for miniaturization and efficiency in many devices. Consider, for example, the difference in size and power output between a modern electric car motor utilizing neodymium magnets and an older motor relying on traditional ferrite magnets. The increase in power density is remarkable.
Their importance extends beyond pure performance. The ability to create powerful magnetic fields in a compact space enables advancements in various fields. From more efficient wind turbines generating clean energy to smaller, more powerful hard disk drives storing vast amounts of data, magnet heavy alloys are driving innovation across numerous industries. Furthermore, ongoing research focuses on improving their temperature stability and corrosion resistance, expanding their potential applications even further.
## What are the key components of Magnet Heavy Alloys?
The composition of magnet heavy alloys significantly impacts their magnetic properties. Neodymium magnets (NdFeB), for instance, typically contain neodymium, iron, boron, and sometimes small additions of dysprosium (Dy) or terbium (Tb) to enhance their high-temperature performance. Samarium cobalt magnets (SmCo), on the other hand, consist primarily of samarium and cobalt, often with minor additions of iron, copper, or zirconium.
Each element contributes differently to the overall performance. Rare earth elements like neodymium and samarium are responsible for the high magnetic anisotropy, which aligns the magnetic moments of the atoms in a specific direction, leading to strong magnetization. Iron contributes to the overall magnetic moment, while boron and cobalt stabilize the structure and improve magnetic hardness (resistance to demagnetization). The precise composition must be carefully controlled to achieve the desired magnetic properties for specific applications. An example formula for a common Neodymium magnet is Nd2Fe14B.
## How Strong Are These Magnets? Understanding Magnetic Properties
The most important properties of magnet heavy alloys are their remanence (Br), coercivity (Hc), and maximum energy product (BHmax). Remanence refers to the strength of the magnetic field remaining after the magnetizing field is removed. Coercivity represents the resistance of the magnet to demagnetization. The maximum energy product is the most important measure of a magnet’s strength, representing the energy a magnet can supply to an external circuit.
Here’s a table comparing typical magnetic properties of common magnet heavy alloys:
| Alloy Type | Remanence (Br) (Tesla) | Coercivity (Hc) (kA/m) | Maximum Energy Product (BHmax) (kJ/m³) |
|—|—|—|—|
| NdFeB (N42) | 1.28-1.32 | 955-1035 | 318-342 |
| SmCo5 | 0.8-1.1 | 720-880 | 120-200 |
| Sm2Co17 | 1.0-1.2 | 800-1200 | 160-280 |
These values highlight the superior performance of NdFeB magnets compared to SmCo magnets in terms of energy product, but SmCo magnets often exhibit better temperature stability. The choice of alloy depends on the specific requirements of the application, considering factors like operating temperature, desired magnetic strength, and cost.
## What is the Curie Temperature, and Why Does it Matter?
The Curie temperature (Tc) is the critical temperature at which a ferromagnetic material loses its magnetic properties and becomes paramagnetic. For magnet heavy alloys, maintaining performance at elevated temperatures is crucial in many applications. Exceeding the Curie temperature results in a significant drop in magnetization, rendering the magnet useless.
The Curie temperature of NdFeB magnets is typically lower than that of SmCo magnets. Standard NdFeB magnets have a Curie temperature around 310-340°C, while SmCo magnets can maintain their magnetism up to 700-800°C. For applications requiring high-temperature stability, SmCo magnets are often preferred, despite their lower overall energy product. Incorporating heavier rare earth elements like dysprosium into NdFeB alloys can raise the Curie temperature, but this often comes at the expense of reduced remanence and increased cost.
## How Do Manufacturing Processes Affect Magnet Heavy Alloy Properties?
The manufacturing process profoundly influences the final properties of magnet heavy alloys. Two primary manufacturing routes exist: powder metallurgy and melt spinning. Powder metallurgy involves compacting and sintering fine powder particles, while melt spinning involves rapidly quenching a molten alloy to form a ribbon-like structure.
* **Powder Metallurgy:** This method allows for precise control over the composition and microstructure, producing magnets with high magnetic properties. However, it can be more expensive and may result in lower density compared to melt spinning.
* **Melt Spinning:** This technique offers a cost-effective way to produce NdFeB magnets with good magnetic properties. The rapid solidification creates a fine-grained microstructure, enhancing coercivity. However, it can be more challenging to control the grain orientation, potentially affecting remanence.
The subsequent heat treatments and shaping processes also play a crucial role in optimizing the magnetic properties. Proper annealing can relieve internal stresses and enhance grain alignment, leading to improved performance.
## Can Corrosion Resistance Be Improved in Magnet Heavy Alloys?
Magnet heavy alloys, particularly NdFeB magnets, are susceptible to corrosion, especially in humid environments. Corrosion can degrade the magnetic properties and ultimately lead to failure. Protecting these magnets from corrosion is crucial for long-term reliability.
Several approaches can be employed to improve corrosion resistance:
* **Coatings:** Applying protective coatings, such as nickel, epoxy, or parylene, provides a barrier against moisture and corrosive agents.
* **Alloying Additions:** Alloying with elements like cobalt, aluminum, or nickel can improve corrosion resistance by forming protective oxide layers.
* **Grain Boundary Engineering:** Modifying the grain boundary composition and microstructure can reduce the pathways for corrosive attack.
Selecting the appropriate corrosion protection strategy depends on the specific application and operating environment. Regular inspection and maintenance are also essential to ensure the long-term integrity of these magnets.
## How Do Magnetic Fields Affect Nearby Electronics?
Magnet heavy alloys produce strong magnetic fields that can interfere with nearby electronic devices. This interference can disrupt the operation of sensitive equipment, such as sensors, displays, and communication systems.
Shielding the magnetic field is often necessary to prevent interference. This can be achieved by enclosing the magnet in a ferromagnetic material, such as steel or mu-metal, which redirects the magnetic field lines away from sensitive components. The effectiveness of the shielding depends on the material’s permeability and the thickness of the shield. Proper grounding and filtering can also help to mitigate the effects of electromagnetic interference.
## What About the Environmental Impact of Rare Earth Mining?
The production of magnet heavy alloys relies heavily on rare earth elements, and their mining and processing can have significant environmental impacts. The extraction of rare earths often involves environmentally damaging practices, such as deforestation, soil erosion, and water contamination.
Addressing these environmental concerns requires a multi-faceted approach:
* **Sustainable Mining Practices:** Implementing responsible mining practices that minimize environmental disturbance and pollution.
* **Recycling and Reuse:** Developing efficient recycling processes to recover rare earth elements from end-of-life products.
* **Material Substitution:** Exploring alternative materials that can partially or fully replace rare earths in certain applications.
Consumers can also contribute by supporting companies that adopt sustainable sourcing practices and by properly disposing of products containing rare earth magnets. An increased focus on sustainable practices will be crucial for the long-term viability of the magnet heavy alloy industry.
## Can New Alloys Improve Magnet Performance? The Future of Magnet Heavy Alloys
Research and development efforts are continuously focused on improving the performance and reducing the cost of magnet heavy alloys. This includes exploring new alloy compositions, refining manufacturing processes, and developing novel magnetic materials.
Some promising research areas include:
* **Rare-Earth-Free Magnets:** Developing magnets based on more abundant and sustainable elements, such as iron, nickel, and aluminum.
* **Nanocomposite Magnets:** Combining hard and soft magnetic materials at the nanoscale to achieve enhanced magnetic properties.
* **Advanced Additive Manufacturing:** Using 3D printing techniques to create magnets with complex geometries and tailored properties.
These advancements hold the potential to revolutionize the magnet industry and unlock new applications for these critical materials. The future of magnet heavy alloys lies in innovation and a commitment to sustainability.
## FAQ Section
**What is the difference between NdFeB and SmCo magnets?**
NdFeB magnets generally have a higher energy product and are stronger at room temperature. SmCo magnets have better temperature stability and corrosion resistance.
**Are magnet heavy alloys safe to handle?**
Yes, but care should be taken. The strong magnetic fields can interfere with pacemakers and other medical devices. Also, smaller magnets can be a choking hazard for children.
**How can I tell if a magnet is made of a heavy alloy?**
Visual inspection alone is not accurate. However, heavy alloy magnets are typically stronger compared to ferrite magnets of similar size. Material certifications and datasheets provide the most definitive confirmations.
**Why are some NdFeB magnets more expensive than others?**
The price depends on the specific grade, which affects performance properties. Magnets that are made of better composition, made with Dysprosium, or a higher grade will be notably more costly.
**Are magnet heavy alloys recyclable?**
Yes, but the recycling process is complex and not widely implemented. However, there is now a heavier focus on recovering rare earth elements to reduce emissions from newly mined materials.
**How do I store magnet heavy alloys?**
Store them in a dry, cool environment and keep them away from sensitive electronics and other magnets to prevent demagnetization or interference. It is also important to handle the materials correctly to avoid any breaking or chipping of the magnets because this can affect its performance.
## 결론
Magnet heavy alloys are indispensable materials in a wide range of applications, offering exceptional magnetic performance. Understanding their properties, manufacturing processes, environmental impacts, and future development directions is crucial for optimizing their use and ensuring their long-term sustainability.
Here are the key takeaways from this blog post:
* Magnet heavy alloys are vital for applications requiring strong magnetic fields in compact spaces.
* Neodymium magnets (NdFeB) offer superior energy product, while samarium cobalt (SmCo) magnets provide better temperature stability.
* Manufacturing processes significantly influence the magnetic properties of these alloys.
* Corrosion protection is crucial for ensuring the long-term reliability of magnet heavy alloys.
* Environmental considerations, particularly regarding rare earth mining, must be addressed through sustainable practices and recycling initiatives.
* Ongoing research is focused on developing new and improved magnet heavy alloys with enhanced performance and sustainability.
Analyzing the Properties of Magnet Heavy Alloys
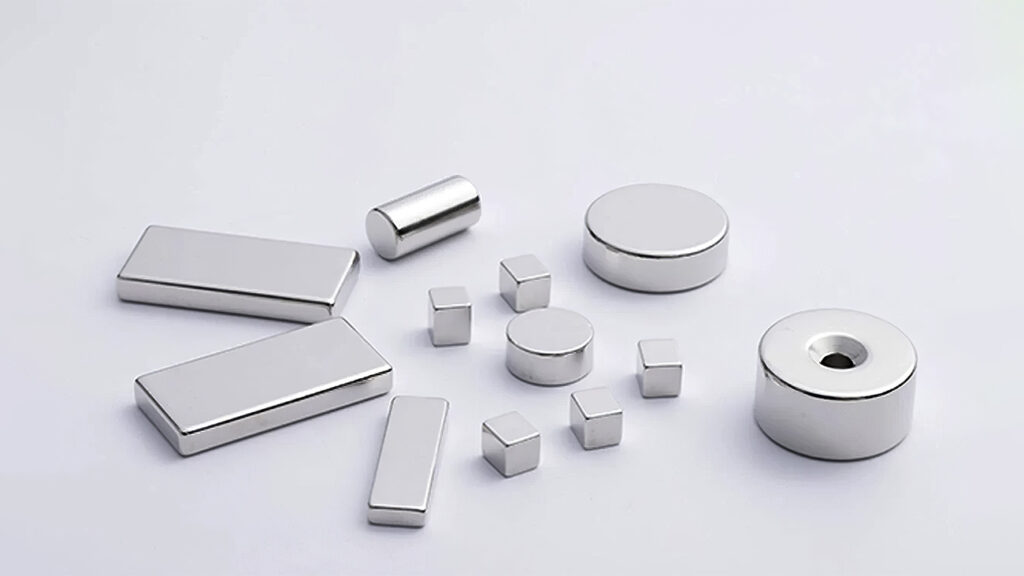