# Choosing the Right Magnet for Your Project: A Detailed Comparison of Magnet Types, Strengths, and Applications
This article is your comprehensive guide to navigating the complex world of magnets. Whether you’re a hobbyist, engineer, or educator, understanding the nuances of magnet types, strengths, and applications is crucial for project success. This detailed comparison will equip you with the knowledge to confidently choose the right magnet for any task, saving you time, money, and frustration. Read on to unlock the secrets of magnetism and harness its power in your next endeavor!
## What Are the Different Types of Magnets and Their Core Properties?
Magnets come in a surprisingly diverse range of materials, each with unique properties that make them suitable for specific applications. Understanding these differences is the first step in choosing the right magnet. Let’s look at the four main types: Neodymium (NdFeB), Samarium Cobalt (SmCo), Alnico, and Ceramic (Ferrite).
* **Neodymium (NdFeB) Magnets:** Renowned for their exceptional strength, Neodymium magnets are the strongest type commercially available. Made from an alloy of neodymium, iron, and boron, they offer incredible magnetic force in a small package. However, they are susceptible to corrosion and high temperatures.
* **Samarium Cobalt (SmCo) Magnets:** With excellent resistance to high temperatures and corrosion, Samarium Cobalt magnets are ideal for harsh environments. While not quite as strong as Neodymium magnets, they retain their magnetic properties over a wider temperature range.
* **Alnico Magnets:** Composed of aluminum, nickel, and cobalt, Alnico magnets offer good temperature stability and are relatively resistant to corrosion. They are less strong than Neodymium and Samarium Cobalt magnets but provide a classic magnetic feel.
* **Ceramic (Ferrite) Magnets:** The most commonly used and cost-effective type, Ceramic magnets are made from iron oxide and barium or strontium carbonate. They are highly resistant to corrosion but have a lower magnetic strength compared to the other types.
**Table 1: Magnet Type Comparison**
| Property | Neodymium (NdFeB) | Samarium Cobalt (SmCo) | Alnico | Ceramic (Ferrite) |
| —————– | ——————- | ———————- | —— | —————– |
| Strength | Very High | High | Medium | Low |
| Temperature Resistance | Low | High | High | Medium |
| Corrosion Resistance | Low | High | Medium | High |
| Cost | Moderate | High | Medium | Low |
## How Do Magnet Strength and Size Affect Performance?
The strength of a magnet, typically measured in Gauss or Tesla, is a critical factor. However, it’s not just about the raw strength number. The *size* and *shape* of the magnet also play significant roles in its overall performance. A small, powerful Neodymium magnet can generate more force than a larger, weaker Ceramic magnet, but the larger magnet might have a more extensive magnetic field.
The relationship between magnet strength, size, and application can be complex. For instance, you might need a small, strong magnet to hold a lightweight object securely or a larger, weaker magnet to cover a wider area. Understanding the specific requirements of your project is essential for determining the optimal magnet size and strength. Think about the contact area, the distance the magnet needs to exert force, and the weight of the object it needs to attract.
Choosing a magnet with the right balance of strength and size is often a process of trial and error. Experimenting with different magnet sizes and strengths within your project’s parameters is often necessary to fine-tune the performance and achieve the desired results. Remember to consider handling and safety too, especially with very strong Neodymium magnets, which can pose a pinching hazard.
## What is the Significance of Curie Temperature?
The Curie temperature is the temperature at which a ferromagnetic material loses its permanent magnetic properties. This is a crucial consideration, especially if your magnet will be operating in a heated environment. Exceeding the Curie temperature will cause the magnet to demagnetize, potentially rendering it useless.
For example, Neodymium magnets have a relatively low Curie temperature (around 310-400°C), making them unsuitable for high-temperature applications. Samarium Cobalt and Alnico magnets, on the other hand, have much higher Curie temperatures (up to 800°C), allowing them to function effectively in hotter conditions. Consider the operating environment and choose a magnet with a Curie temperature well above the expected maximum.
It’s not just the maximum temperature that matters; prolonged exposure to elevated temperatures can also lead to gradual demagnetization over time, even if the Curie temperature is not reached. This degradation is often referred to as “magnetic aging” and should be taken into account when designing long-term applications. Always consult the magnet’s specifications and consider safety margins regarding temperature.
## How Does Corrosion Resistance Impact Magnet Longevity?
Corrosion can significantly reduce a magnet’s lifespan and performance. Exposure to moisture, chemicals, or even certain gases can cause the magnet material to degrade, leading to weakening and eventual failure. The corrosion resistance of a magnet depends on its composition and any protective coatings applied.
Neodymium magnets are particularly susceptible to corrosion due to their iron content. To mitigate this, they are typically coated with layers of nickel, epoxy, or other protective materials. Samarium Cobalt and Ceramic magnets offer excellent corrosion resistance due to their inherent chemical stability. Alnico magnets also exhibit good corrosion resistance but may develop surface oxidation over time, which doesn’t usually affect their performance.
The environment in which the magnet will be used is a critical determinant in selecting the right type. If the magnet will be exposed to harsh conditions, such as saltwater, acidic environments, or high humidity, choosing a corrosion-resistant material is crucial. Consider stainless-steel housings or special coatings for added protection. Regular inspection and maintenance can also help prolong the lifespan of magnets in corrosive environments.
## What are the Common Applications for Each Magnet Type?
Each magnet type excels in specific applications due to its unique combination of properties. Knowing these common uses can help guide your choice.
* **Neodymium Magnets:** Used in hard drives, electric motors, speakers, magnetic separators, and jewelry clasps due to their high strength.
* **Samarium Cobalt Magnets:** Employed in high-performance motors, sensors, and aerospace applications where high temperature and corrosion resistance are required.
* **Alnico Magnets:** Found in electric motors, generators, guitar pickups, and educational demonstrations due to their temperature stability and classic magnetic properties.
* **Ceramic Magnets:** Widely used in loudspeakers, door latches, magnetic toys, and holding magnets because of their low cost and corrosion resistance.
Consider a few examples: In a high-speed electric motor, you would likely choose a Neodymium or Samarium Cobalt magnet for its high strength and efficiency. In a refrigerator magnet, a Ceramic magnet is usually sufficient due to its low cost and adequate holding power. For a compass, an Alnico magnet provides consistent and reliable directional performance. By aligning the magnet’s properties with the application’s demands, you can optimize performance and ensure the longevity of your project.
## What Role Does Magnet Shape Play in Its Effectiveness?
The shape of a magnet significantly affects its magnetic field and performance. Common shapes include discs, rods, rings, blocks, and horseshoes, each offering unique advantages.
* **Disc Magnets:** Provide a concentrated magnetic field on one or both flat surfaces.
* **Rod Magnets:** Emit a magnetic field along their length, suitable for attraction and repulsion.
* **Ring Magnets:** Allow for mounting on shafts or axles and provide a circular magnetic field.
* **Block Magnets:** Offer a strong and versatile magnetic field, often used for holding and lifting.
* **Horseshoe Magnets:** Concentrate the magnetic field between their poles, maximizing holding power.
For example, a horseshoe magnet is ideal for lifting heavy objects because its shape concentrates the magnetic field at the poles. Disc magnets are often used in sensors and actuators where a focused magnetic field is needed. The shape should be selected based on the direction and concentration of the magnetic force required for your specific application. Using Finite Element Analysis (FEA) software can simulate magnetic fields and help optimize magnet shape for your design.
## How Do Protective Coatings Affect Magnet Performance and Cost?
Protective coatings are often applied to magnets to enhance their corrosion resistance and mechanical strength. Common coatings include nickel, epoxy, zinc, and gold. These coatings add a layer of protection against environmental factors, extending the magnet’s lifespan.
* **Nickel Coating:** Provides good corrosion resistance and a shiny appearance.
* **Epoxy Coating:** Offers excellent resistance to chemicals and moisture but can be brittle.
* **Zinc Coating:** A cost-effective option for general corrosion protection.
* **Gold Coating:** Provides excellent corrosion resistance and is biocompatible, suitable for medical applications.
Consider the cost-benefit ratio of each coating. While more expensive coatings offer better protection, they may not be necessary for all applications. For example, a Neodymium magnet used indoors in a dry environment may only need a basic nickel coating, while a magnet used outdoors or in a corrosive environment may require a more robust epoxy or gold coating. The cost of the coating should be weighed against the potential cost of replacing a corroded magnet.
## How Can I Demagnetize a Magnet Safely?
Demagnetizing a magnet involves reducing its magnetic field. This can be achieved through various methods, including heating, applying a strong opposing magnetic field, or subjecting the magnet to mechanical shock.
* **Heating:** Exceeding the magnet’s Curie temperature will demagnetize it. However, this is not always practical or safe.
* **Opposing Magnetic Field:** Placing the magnet in a strong opposing magnetic field can disrupt its internal magnetic alignment.
* **Mechanical Shock:** Repeatedly striking or vibrating the magnet can also weaken its magnetic field, but this is less controlled.
Demagnetization is often used in applications where magnets need to be temporarily disabled or when disposing of magnets safely. However, attempting to demagnetize powerful magnets without proper equipment and precautions can be dangerous. Always wear appropriate safety gear, such as gloves and eye protection, and consult with a professional if you are unsure about the process. Never attempt to demagnetize magnets by microwaving them, as this can be extremely dangerous and potentially cause a fire.
## What Safety Precautions Should I Take When Working With Magnets?
Working with magnets, particularly strong Neodymium magnets, requires careful attention to safety. These magnets can generate powerful forces that can cause injuries if not handled properly.
* **Pinch Points:** Avoid placing fingers or other body parts between magnets, as they can snap together with considerable force, causing painful pinches or even broken bones.
* **Medical Implants:** Individuals with pacemakers or other implanted medical devices should avoid close contact with strong magnets, as they can interfere with the device’s operation.
* **Electronic Devices:** Keep magnets away from electronic devices such as computers, credit cards, and mobile phones, as they can damage or erase data.
* **Metal Objects:** Be careful when handling magnets near metal objects, as they can be unexpectedly attracted, potentially causing injury or damage.
Always store magnets in a safe place, out of reach of children. Wear appropriate safety gear, such as gloves and eye protection, when handling strong magnets. If you are unsure about the force or safety of a magnet, consult with a professional. Understanding and following these safety precautions will help prevent accidents and ensure a safe working environment.
## How Can I Measure Magnetic Field Strength Accurately?
Measuring magnetic field strength accurately requires specialized equipment called magnetometers or Gaussmeters. These devices measure the magnetic flux density, typically in units of Gauss or Tesla.
Analog Gaussmeters are more economical but provide less precision, while digital Gaussmeters offer higher accuracy and resolution. Hall effect sensors are commonly used in Gaussmeters to measure magnetic fields.
Proper calibration is essential for accurate measurements. Calibrate the Gaussmeter according to the manufacturer’s instructions before taking any measurements. Take measurements in a controlled environment, away from external magnetic fields or other sources of interference. Multiple measurements should be taken and averaged to minimize error. By following these guidelines, you can obtain accurate and reliable measurements of magnetic field strength, which are crucial for optimizing your magnet applications.
## FAQ 섹션:
**What is the strongest type of magnet available?**
Neodymium (NdFeB) magnets are the strongest commercially available magnets due to their high magnetic energy product. However, their performance degrades at higher temperatures.
**Are Neodymium magnets safe to handle?**
Yes, but caution is needed. Strong Neodymium magnets can pinch fingers if allowed to snap together. They should also be kept away from electronic devices and medical implants.
**How do I choose the right magnet size for my project?**
Consider the required holding force, the available space, and the type of material the magnet will be attaching to. Experimenting with different sizes is often necessary.
**Can magnets lose their strength over time?**
Yes, magnets can lose some strength over time due to factors like temperature, external magnetic fields, and mechanical stress. This is called demagnetization. The rate of demagnetization varies depending on the magnet type and operating conditions.
**How do I dispose of magnets safely?**
Wrap the magnets securely in cardboard or other cushioning material to prevent them from snapping together or attracting metal objects. Dispose of them according to local regulations for electronic waste or hazardous materials. Large quantities may require special handling.
**What’s the difference between Gauss and Tesla?**
Gauss (G) and Tesla (T) are units of magnetic flux density. 1 Tesla equals 10,000 Gauss. Tesla is the SI unit, while Gauss is commonly used in the United States.
## 결론:
Choosing the right magnet for your project is a critical decision that can significantly impact its performance, longevity, and cost. By understanding the different types of magnets, their properties, and applications, you can make informed choices that align with your specific needs. Remember to consider the magnet’s strength, size, temperature resistance, corrosion resistance, shape, and cost. Prioritize safety when handling magnets, and always consult with a professional if you have any questions or concerns.
주요 요점:
* **Neodymium Magnets:** High strength, moderate temperature resistance, prone to corrosion.
* **Samarium Cobalt Magnets:** High strength, excellent temperature and corrosion resistance.
* **Alnico Magnets:** Medium strength, good temperature stability, classic magnetic properties.
* **Ceramic Magnets:** Low cost, high corrosion resistance, lower strength.
* **Consider Environmental Factors:** Temperature, humidity, and exposure to chemicals.
* **Prioritize Safety:** Handle strong magnets with care to avoid injury.
Choosing the Right x Magnet for Your Project: A Detailed Comparison
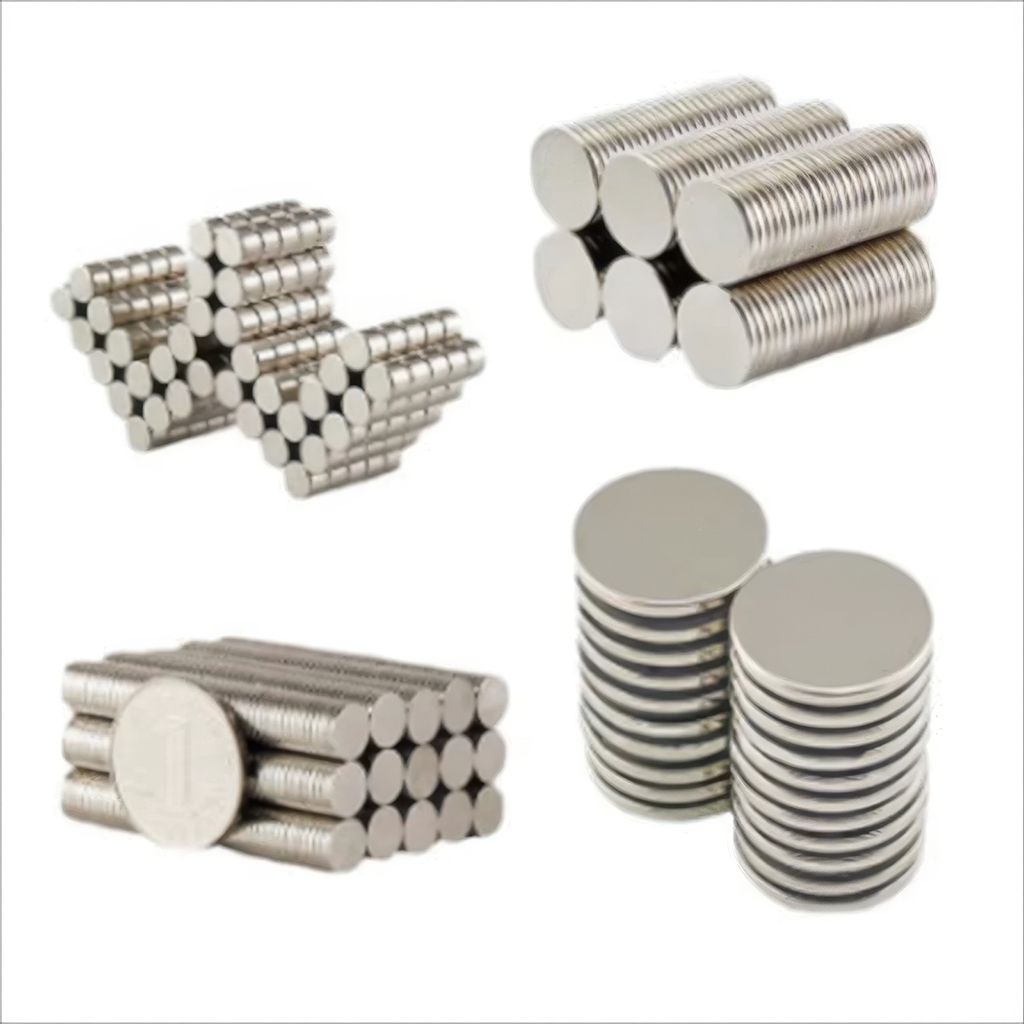