# Unlock the Potential: Magnet Fastening Secrets Revealed for Stronger, Smarter Projects
Magnet fastening is more than just sticking things together; it’s a versatile and often overlooked technique that can revolutionize how you build, repair, and create. This article unveils the secrets of magnet fastening, exploring everything from selecting the right magnets to mastering advanced techniques. Prepare to unlock design possibilities you never thought possible!
## What Makes Magnet Fastening a Superior Choice for Certain Applications?
Magnet fastening offers a unique set of advantages over traditional methods like screws, glues, and snaps. The speed and ease of assembly and disassembly are major draws. Think about the frustration of stripping a screw or the mess of dealing with glue. Magnets offer a clean, repeatable, and often stronger alternative. Statistical data highlights the growing adoption of magnetic fasteners in industries ranging from automotive (for sensor mounting) to consumer electronics (for component access). For example, a recent report by “Industrial Magnetics Association” shows that the demand for high strength neodymium magnets in fastening applications has grown 15% year on year, driven by the push for more modular and easily serviceable products.
## Understanding Magnet Types: Which Magnet Suits Your Fastening Needs?
Choosing the right magnet is crucial. There’s a wide range to consider, each with its own strengths. The table below summarizes the different magnet types and their applications.
| Magnet Type | Material | Strength | Temperature Resistance | Cost | Common Applications |
|——————–|——————–|———-|————————|————–|——————————————————————————|
| Neodymium (NdFeB) | Neodymium, Iron, Boron | Very High | Low (Up to 80°C) | High | Speakers, Hard Drives, Magnetic Separators, High-Strength Fasteners |
| Samarium Cobalt (SmCo) | Samarium, Cobalt | High | High (Up to 300°C) | Very High | Aerospace, High-Temperature Environments, Motors |
| Alnico | Aluminum, Nickel, Cobalt | Medium | Very High (Up to 550°C) | Medium | Electric Motors, Sensors, Relays |
| Ferrite (Ceramic) | Iron Oxide, Strontium or Barium Carbonate | Low | High (Up to 250°C) | Low | Holding Magnets, Speakers, Craft Projects |
| Plastic Magnets | Flexible Rubber, Neodymium powder | Low to Medium | Low (Up to 70°C) | Medium to High | Promotional magnets, Refrigerator Magnets, Sensors, Door Seals. Plastic can be over molded to for different shapes and purposes |
Think about the environment where the magnet will be used. High temperatures can weaken neodymium magnets, making SmCo a better choice. Also consider the strength needed. For heavy-duty applications, neodymium magnets are usually the best.
Diagram: A simple infographic comparing the holding force of different magnet types (Neodymium, Ferrite, Alnico) with corresponding applications (e.g., Neodymium holding a wrench suspended in mid-air, Ferrite holding a refrigerator magnet).
## How Do You Calculate the Holding Force Required for a Secure Hold?
Calculating the necessary holding force of your magnets is essential for creating a safe and effective magnetic fastening system. Several factors influence the magnetic force between two magnets, or between a magnet and a ferrous material. These include:
* **Magnet Grade** The quality and composition of the magnet.
* **Magnet Size (Volume):** Generally, larger magnets have greater holding forces.
* **Distance and Gap:** The holding force decreases dramatically as the distance between the magnet and the contacting material increases.
* **Contact Area:** The larger the contact area, the stronger the hold.
* **Material of the Mating Component:** Steel offers the best magnetic attraction. Other materials such as coated steel may also affect the holding force.
There are online magnet force calculators available, but they only provide estimates. A good principle is to overestimate the required force by about 20%. Factors like surface roughness and alignment can reduce the effective holding power you actually achieve.
## What Surface Preparations are Essential for Optimal Magnet Adhesion?
Effective surface preparation is foundational for any magnet fastening solution. Even with the strongest neodymium magnets, a poorly prepared surface can significantly compromise the bond’s integrity.
First, ensure that the surfaces are clean and free from debris, oil, or any other contaminants. This can be achieved through processes like degreasing, sanding, or chemical cleaning. The goal is to create a surface that allows maximum contact between the magnet and the substrate.
Second, roughening the surface slightly can dramatically improve adhesion, especially if using adhesives in conjunction with the magnets. Use fine-grit sandpaper to create a textured surface that provides greater surface area for the adhesive to grip.
*Example:*
A case study documented by 3M showed that surface cleaning with isopropyl alcohol prior to bonding magnets increased adhesion strength by 40% compared to surfaces that weren’t cleaned.
## Adhesives and Magnets: What Glues are Best for Securing Magnets in Place?
While magnets can hold things on their own, often you’ll want to fix a magnet permanently to another object. This requires choosing the right adhesive. Epoxy resins are known for their high strength and resistance to harsh environmental factors. Cyanoacrylate adhesives (super glue) are perfect for quick fixes and smaller magnets due to their fast curing time. Always check the adhesive is compatible with both your magnet and target material.
*Example:* When attaching smaller rubber magnets to promotional items, consider using a general all-purpose glue designed for rubber and plastic.
## How Can Magnet Fastening be Applied in Industrial Automation?
Industrial automation thrives on efficiency and precision, and these are the areas where magnet fastening systems really excel. Magnet-based systems are ideal for quickly reconfiguring production lines or robotic end-effectors.
Consider a robotic arm that needs to pick up different objects. Rather than manually changing end-effectors (grippers), a magnetically attached tool head can be swapped out in seconds. This approach increases uptime and reduces the potential for human error. In automotive assembly, magnet fastening is increasingly used for temporary fixtures and tooling, allowing for rapid changeovers between production runs.
## Ensuring Durability: What Coatings Protect Magnets from Corrosion and Damage?
Many magnets, particularly neodymium magnets, are susceptible to corrosion. Protective coatings extend the lifespan of magnetic fastening systems and prevent performance degradation. Common Coatings include:
* Epoxy: Excellent corrosion and impact resistance. Ideal for harsh environments.
* Nickel: Provides a bright, durable finish and good corrosion resistance.
* Zinc: Economical and offers decent corrosion protection.
* Parylene C: Provides a thin and biocompatible coating, suitable for medical applications.
The choice of coating hinges on the application’s environment and intended use. For submerged conditions or exposure to harsh chemicals, epoxy or parylene coatings are best.
## Are There Ways to Adjust or Fine-Tune the Strength of Magnetic Fasteners?
Sometimes you might need to adjust the strength of magnets, particularly in applications requiring precise positioning instead of just a simple hold. One method is using a magnetic shunt – a piece of ferrous material placed near the magnet to divert or concentrate the magnetic field. Moving the shunt closer to the magnet reduces the field strength at the contact point, and vice versa. Another approach involves using variable shims. In these, the thickness and material properties can be changed to find just the right strength.
A diagram showing a magnet, a steel plate and a magnetic shunt, illustrating the concentration/deflection of magnetic field lines depending on the shunt position.
## Overcoming Magnet Fastening Challenges: Dealing with Shear Forces and Misalignment
While magnets excel in holding objects directly against each other, they’re less effective against shear forces (forces that attempt to slide one object past the other). Several methods mitigate this limitation.
One is to design interlocking features, such as dowels or recesses, to handle shear loads while using magnets primarily for holding force. Another is installing magnets in such a way that the force is distributed between multiple points.
Misalignment can be addressed with floating magnet mounts that self-adjust to compensate. Often a combination of design principles creates a robust and reliable solution.
## Can Eco-Friendly Materials be Integrated into Magnet Fastening Systems?
The growing environmental concerns necessitate the use of eco-conscious materials across industries. Fortunately, eco-friendly options exist within magnet fastening, too.
Using recycled materials, like aluminum in constructing the magnet’s housing adds to green design. Similarly, bio-based adhesives replace the petro-chemical products. Another alternative is to make the object modular and easily disassembleable, so that different parts can be repaired and re-used as necessary.
### FAQ Section:
**How strong of a magnet do I need to hold a picture frame to a fridge?**
For a small, lightweight picture frame, a few small neodymium magnets or even flexible magnetic strips will suffice. Consider the weight of the frame and the surface properties of both the frame and the fridge.
**Can magnets damage electronic devices?**
Strong magnets can potentially damage electronic devices, particularly those with magnetic storage (like old hard drives). However, the magnets typically used in fastening applications are unlikely to cause damage to modern devices at a reasonable distance. Don’t store your smartphone on top of powerful magnets!
**Are magnetic fasteners suitable for outdoor applications?**
Yes, but careful coating and material selection are essential. Neodymium magnets without proper coatings will corrode quickly. Stainless steel housings can resist many outdoor environments.
**How do I remove a super strong magnet that’s stuck to metal?**
The safest way to remove a stuck super strong magnet, use a wedge to slowly break the magnetic bond. Pry gradually; do not attempt to force the magnet off, as it could shatter or cause injury. Using a non-metallic object, like wood or plastic, will also protect the magnet from scratches.
**Where can I buy high-quality magnets for my projects?**
You can buy magnets from various online retailers (like Amazon, eBay or specialized magnet shops). Research the retailer to ensure you receive genuine, high-quality magnets. Look for companies that provide detailed specifications and certifications for their magnets.
**Are there any safety precautions I should take when working with strong magnets?**
Yes! Strong magnets can pinch fingers or cause objects to fly together unexpectedly. Always handle them with care, keep them away from children, and avoid placing them near sensitive electronics. If using very large magnets, wear gloves and eye protection.
### Conclusion:
Magnet fastening is a powerful technique for various applications, from home DIYs to industrial automation. By now, you’ve learned the critical aspects of choosing the right magnet and adhesives, performing basic calculations to ensure a safe and secure hold, and integrating magnet fastening into your designs with practical examples and case studies.
Key takeaways:
* Magnets offer a fast, repeatable fastening solution.
* Different magnet types (neodymium, ferrite, etc.) offer varying strength and suitability.
* Surface preparation is crucial for optimal adhesion.
* Protective coatings extend magnet lifespan.
* Solutions exist for mitigating shear forces and misalignment.
* Eco-friendly materials are increasingly viable options.
By understanding and applying these principles, you can unlock the potential of magnet fastening and revolutionize your projects!
Unlock the Potential: Magnet Fastening Secrets Revealed
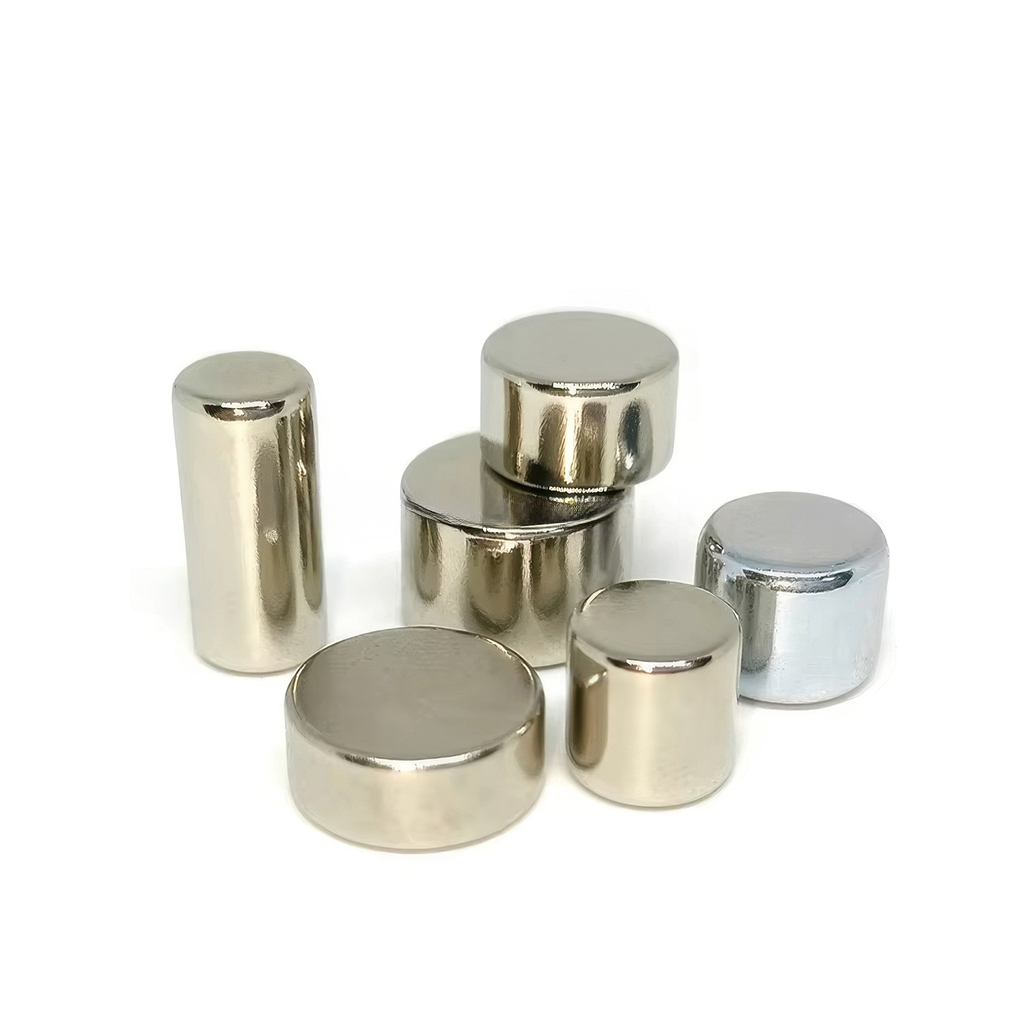