# Unveiling Ferrite Magnet Secrets: Modeling and Simulation in Magnetic Circuits
Ferrite magnets are ubiquitous, powering everything from electric motors to loudspeakers. But understanding their behavior within complex magnetic circuits can be challenging. This article provides a comprehensive guide to modeling and simulating ferrite magnet performance, empowering you to design more efficient and effective magnetic systems. We’ll explore the key principles, techniques, and software tools involved, making this journey accessible even if you’re not a magnetic circuit guru.
## Why is Accurately Modeling Ferrite Magnet Behavior Crucial for Magnetic Circuit Design?
Accurate modeling is the cornerstone of successful magnetic circuit design. Ferrite magnets, while cost-effective and versatile, exhibit nonlinear behavior and are influenced by temperature, manufacturing variations, and demagnetization effects. Failing to account for these factors can lead to:
* **Suboptimal Performance:** The circuit might not deliver the desired magnetic field strength or distribution. Imagine designing a motor that doesn’t reach its target speed and torque.
* **Increased Development Costs:** Extensive prototyping and iterations become necessary to correct design flaws. This translates to wasted time and resources.
* **Reliability Issues:** Undesirable demagnetization can occur, leading to reduced performance over time and potential system failure.
Consider a simple application like holding a door open. If your ferrite magnet isn’t sized and positioned correctly, the door might slam shut unexpectedly! Modeling accurately predicts these scenarios, saving you headaches down the line.
## How Do B-H Curves Help Us Understand Ferrite Magnet Characteristics?
The B-H curve (also known as the hysteresis loop) is the fingerprint of a magnetic material. For ferrite magnets, it plots the relationship between the magnetic flux density (B) and the magnetic field strength (H). This curve is essential for understanding:
* **Remanence (Br):** This represents the residual magnetism of the ferrite magnet after the external field is removed. A higher Br indicates a stronger magnet.
* **Coercivity (Hc):** This indicates the resistance of the magnet to demagnetization. A higher Hc means the magnet is more difficult to demagnetize.
* **Permeability (µ):** The slope of the B-H curve represents the permeability, which describes how easily the material becomes magnetized in the presence of an external field.
Here’s a simple table illustrating typical values for a common ferrite magnet material:
| Property | Symbol | Value | Unit |
|————-|——–|———————|———|
| Remanence | Br | 0.4 Tesla | T |
| Coercivity | Hc | 300 kA/m | A/m |
| Permeability| µ | ~100 (relative) | Unitless|
Understanding these parameters from the B-H curve allows us to predict how the ferrite magnet will behave in various applications and under different operating conditions.
## What are the Different Modeling Approaches for Ferrite Magnets in Magnetic Circuits?
Several modeling approaches exist, each with its own trade-offs between accuracy and computational complexity. Here are some common methods:
1. **Lumped Parameter Model:** This is the simplest approach, treating the magnet as a voltage source in an electrical circuit analogy. While computationally efficient, it sacrifices accuracy by neglecting spatial variations of the magnetic field. This is like assuming the Earth is flat – fine for small areas, but disastrous for global travel.
2. **Finite Element Analysis (FEA):** FEA divides the geometry of the magnetic circuit into small elements and solves Maxwell’s equations numerically. FEA offers high accuracy but requires significant computational resources and expert knowledge of meshing and solver parameters. Think of this like building a 3D model of the Earth – very precise, but a lot of work.
3. **Boundary Element Method (BEM):** BEM focuses on the surfaces of the magnetic components, reducing the computational domain. It’s particularly well-suited for open-boundary problems but can be less efficient for complex geometries.
4. **Hybrid Methods:** These combine different modeling techniques to leverage their strengths and mitigate their weaknesses. For example, a lumped parameter model might be used for the magnet, while FEA handles the air gap field.
The choice of modeling approach depends on the specific application, desired accuracy, and available computational resources.
## How Can Simulation Software Help in Analyzing Ferrite Magnet Behavior?
Simulation software is invaluable for analyzing ferrite magnet behavior in magnetic circuits. Here are some key features and benefits:
* **Realistic Geometry Modeling:** Import CAD models or create custom geometries to accurately represent the physical structure of the magnetic circuit.
* **Material Property Definition:** Define the B-H curve, temperature dependence, and other relevant material properties of the ferrite magnet.
* **Solver Selection:** Choose the appropriate solver (e.g., static, transient, harmonic) based on the nature of the problem.
* **Meshing:** Discretize the geometry into a mesh of elements for FEA or BEM analysis.
* **Boundary Conditions:** Define boundary conditions to represent external fields, currents, or other constraints.
* **Post-Processing:** Visualize the magnetic field distribution, flux density, and other relevant parameters.
Popular simulation software packages include ANSYS Maxwell, COMSOL Multiphysics, and SimScale. These tools allow you to explore different design iterations virtually, optimizing performance and minimizing prototyping costs.
## What Factors Influence the Accuracy of Ferrite Magnet Simulations?
Several factors can impact the accuracy of ferrite magnet simulations. Ignoring these can lead to inaccurate results and flawed designs:
* **Material Data Accuracy:** Inaccurate or incomplete B-H curve data can lead to significant errors. Always use reliable material data sheets from the magnet manufacturer.
* **Mesh Quality:** A poorly constructed mesh can introduce numerical errors, particularly in regions with high field gradients. Refine the mesh in critical areas.
* **Solver Settings:** Improper solver settings, such as the convergence criteria or time step size, can affect the accuracy and stability of the simulation.
* **Temperature Effects:** Ferrite magnet performance is temperature-dependent. Accurately model the temperature distribution and its impact on the B-H curve. At higher temperatures, the remanence typically decreases.
* **Demagnetization Effects:** Strong opposing fields can permanently demagnetize the ferrite magnet. Include demagnetization effects in your model, especially in applications with pulsed fields.
Consider a scenario where you are simulating a motor. If you ignore the temperature rise within the motor during operation, you may overestimate the motor’s torque output.
## Can We Predict Demagnetization Risks in Ferrite Magnets Through Simulation?
Yes! Simulation is particularly valuable for predicting demagnetization risks. By accurately modeling the magnetic field distribution and the magnet’s B-H curve, you can identify regions where the magnet is subjected to strong opposing fields. The simulation can show you if the operating point falls below the “knee” of the B-H curve, which is the point where irreversible demagnetization begins.
This is crucial for applications like magnetic brakes or actuators, where the magnet is subjected to large reverse fields. Simulation allows you to optimize the magnet geometry, material selection, and operating conditions to minimize the risk of demagnetization.
## How Does Temperature Affect Ferrite Magnet Performance and How Can We Model It?
Temperature has a significant impact on ferrite magnet performance. As temperature increases, the remanence (Br) and coercivity (Hc) typically decrease. This means the magnet becomes weaker and more susceptible to demagnetization.
To accurately model temperature effects, you need to:
* **Obtain Temperature-Dependent B-H Curves:** Many magnet manufacturers provide B-H curves at different temperatures.
* **Model Thermal Distribution:** Simulate the temperature distribution within the magnetic circuit using computational fluid dynamics (CFD) or thermal FEA.
* **Couple Magnetic and Thermal Simulations:** Create a coupled simulation that accounts for the interaction between the magnetic and thermal fields. The magnetic field generates heat, and the temperature affects the magnetic properties.
For example, a loudspeaker might experience a temperature increase due to the current flowing through the voice coil. This temperature increase can affect the performance of the ferrite magnet driving the speaker.
## What are Some Common Applications Where Accurate Ferrite Magnet Modeling is Essential?
Accurate ferrite magnet modeling is essential in a wide range of applications, including:
* **Electric Motors:** Designing efficient and reliable electric motors requires precise modeling of the magnetic field distribution in the air gap and the interaction with the stator windings.
* **Loudspeakers:** Optimizing the magnet size and shape for maximum sound output and minimal distortion.
* **Magnetic Sensors:** Designing sensitive magnetic sensors for position, speed, or current measurement. Accurate modeling is vital for achieving the desired sensitivity and linearity.
* **Magnetic Resonance Imaging (MRI):** Ensuring the homogeneity of the magnetic field in an MRI scanner requires precise modeling of the superconducting magnets and the surrounding shielding. While ferrite magnets are not typically used in the main field magnets, they may be used for shielding or field correction purposes.
* **Magnetic Separators:** Designing efficient magnetic separators for removing ferrous materials from non-ferrous materials.
## What Future Trends are Emerging in Modeling and Simulation of Ferrite Magnet Systems?
The field of modeling and simulation of ferrite magnet systems is constantly evolving. Some emerging trends include:
* **Multiphysics Simulations:** Integrating magnetic, thermal, mechanical, and electrical simulations to capture the complex interactions in real-world applications.
* **Machine Learning:** Using machine learning algorithms to predict magnet behavior based on limited data or to optimize magnet designs.
* **Digital Twins:** Creating virtual replicas of physical magnetic systems for real-time monitoring, prediction, and optimization.
* **Improved Material Models:** Developing more accurate and comprehensive material models that account for hysteresis, temperature dependence, and other factors.
These advancements are paving the way for more accurate, efficient, and robust designs of ferrite magnet systems.
## Case Study: Optimizing a Ferrite Magnet Motor with Simulation
Let’s consider a case study of optimizing a small DC motor using simulation. The initial motor design used a simple ferrite magnet configuration. Through simulation, we identified several areas for improvement:
* **Inhomogeneous Field Distribution:** The magnetic field was not uniformly distributed in the air gap, leading to torque ripple.
* **Demagnetization Risk:** The magnets were susceptible to demagnetization under high load conditions.
Using FEA simulation, we explored different magnet shapes and arrangements. We also analyzed the influence of the stator tooth geometry. The simulation results indicated that optimizing the magnet shape and adding a backing iron yoke significantly improved the field uniformity, reducing torque ripple by 30% and lowering the risk of demagnetization. This resulted in a more efficient and reliable motor, achieved without building numerous physical prototypes.
## Frequently Asked Questions (FAQs)
**What is the difference between hard and soft ferrites?**
Hard ferrites have high coercivity and remanence, making them suitable for permanent magnet applications. Soft ferrites, on the other hand, have low coercivity and remanence, making them ideal for high-frequency applications like inductors and transformers.
**How do I obtain accurate B-H curve data for my ferrite magnet?**
The best source of B-H curve data is the magnet manufacturer. They typically provide data sheets that include B-H curves at different temperatures. If you need to generate your own B-H curve, you can use a hysteresisgraph instrument.
**What are the limitations of lumped parameter models for ferrite magnets?**
Lumped parameter models are simple and computationally efficient, but they neglect spatial variations of the magnetic field. This can lead to inaccurate results, especially in complex geometries or when high accuracy is required. They are best suited for preliminary designs.
**How can I validate my simulation results?**
Validate your simulation results by comparing them to experimental measurements. You can measure the magnetic field distribution using a Gaussmeter or measure the performance characteristics of the magnetic circuit, such as the holding force or motor torque. Ensure you are using calibrated equipment.
**What is the best meshing strategy for simulating ferrite magnets in FEA?**
Use a fine mesh in regions with high field gradients, such as the air gap between the magnet and the pole pieces. Also, ensure that the mesh is fine enough to accurately represent the geometry of the magnet and the surrounding structures. Consider using adaptive meshing techniques to automatically refine the mesh in critical areas.
**Can I use simulation to optimize the cost of a ferrite magnet design?**
Yes, simulation allows you to explore trade-offs between performance and cost. For example, you can simulate different magnet sizes and shapes to find the optimal design that meets your performance requirements at the lowest cost. You can also evaluate different ferrite materials with varying prices and properties.
## Conclusion
Modeling and simulation of ferrite magnet behavior in magnetic circuits is crucial for designing efficient, reliable, and cost-effective magnetic systems. By understanding the principles, techniques, and software tools involved, you can unlock the full potential of ferrite magnets in your applications.
Key Takeaways:
* Accurate modeling of ferrite magnet behavior is essential for optimal performance.
* The B-H curve is a crucial tool for understanding ferrite magnet characteristics.
* FEA simulation provides high accuracy but requires computational resources.
* Temperature and demagnetization effects must be considered for accurate simulations.
* Simulation can be used to optimize magnet designs for performance, reliability, and cost.
Modeling and Simulation of Ferrite Magnet Behavior in Magnetic Circuits
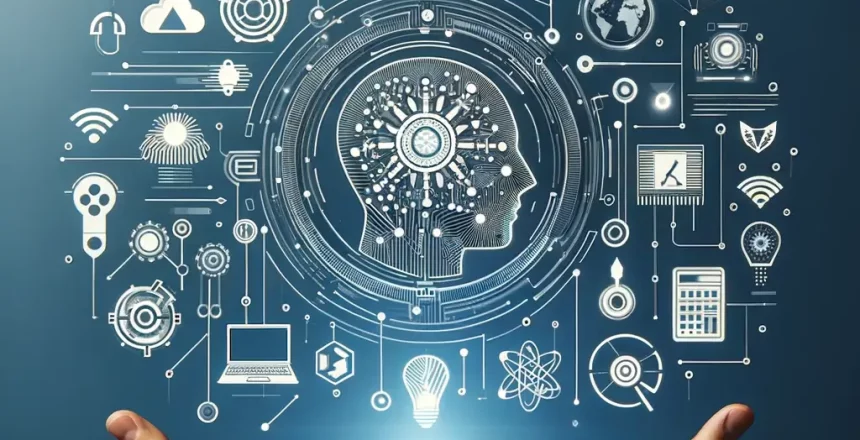