# Maximizing Magnetic Remanence: The Key Influence of Grain Orientation on Ring Magnets
Ring magnets are ubiquitous, found in everything from electric motors to hard drives. Their effectiveness hinges on their magnetic remanence – how much magnetism they retain after being subjected to an external magnetic field. Understanding and controlling the factors that influence remanence is crucial for optimizing magnet performance. This article focuses on one of the most significant factors: **grain orientation**. We’ll explore how aligning the magnetic grains within a ring magnet can dramatically impact its remanence, and therefore, its overall performance. If you’re a design engineer, a materials scientist, or simply fascinated by the world of magnetism, this deep dive into grain orientation techniques and their impact is a valuable read.
## What is Grain Orientation and Why Does it Matter for Ring Magnet Performance?
Imagine a ring magnet as being composed of countless tiny, individual magnets, or “grains.” Each grain has its own magnetic moment, pointing in a specific direction. If these grains are randomly oriented, their magnetic fields tend to cancel each other out, resulting in a weak overall magnet. However, if we can align these magnetic moments, we create a powerful, unified magnetic field. **Grain orientation** refers to the degree to which these grains are aligned in the same direction. The better the alignment, the higher the magnet’s remanence, and the stronger the magnet.
## How Does Anisotropy Relate to Grain Orientation and Magnetic Remanence?
The relationship between **anisotropy**, grain orientation, and magnetic remanence is fundamental to understanding high-performance magnets. Anisotropy describes the preference of a material to magnetize in a specific direction (the easy axis). In many hard magnetic materials used for ring magnets (like Neodymium Iron Boron – NdFeB), this easy axis corresponds to the crystallographic orientation of the grains.
When grains are aligned (good grain orientation), their easy axes are also aligned. This maximizes the magnetic remanence along that preferred direction, resulting in a powerful magnet. Conversely, when grains are randomly oriented, the anisotropy is effectively averaged out, leading to lower remanence. Think of it like a team pulling on a rope. If everyone pulls in the same direction (aligned grains, high anisotropy), the force is maximized. If everyone pulls in random directions (randomly oriented grains, low anisotropy), the net force is weak.
## Isotropic vs. Anisotropic Ring Magnets: What’s the Difference in Terms of Grain Orientation?
We can broadly categorize ring magnets into two groups based on grain orientation: isotropic and anisotropic.
* **Isotropic Ring Magnets:** These magnets have randomly oriented grains. They can be magnetized in any direction after they are manufactured. While they are easier and less expensive to produce, their remanence is significantly lower. Consider a simple ceramic magnet on your refrigerator; it’s likely isotropic.
* **Anisotropic Ring Magnets:** These magnets have their grains aligned during manufacturing. This alignment provides a preferred direction of magnetization, leading to significantly higher remanence and magnetic performance. However, they can only be magnetized along their preferred axis. Most high-performance magnets used in motors and generators are anisotropic.
The following table summarizes the key differences:
| Feature | Isotropic Ring Magnets | Anisotropic Ring Magnets |
|—————-|————————-|————————–|
| Grain Orientation | Random | Aligned |
| Remanence | Lower | Higher |
| Magnetization Direction | Any | Preferred Axis Only |
| Manufacturing Cost | Lower | Higher |
## What Manufacturing Techniques Enhance Grain Orientation in Ring Magnets?
Several manufacturing techniques are employed to achieve high grain orientation in ring magnets. These techniques generally involve applying a magnetic field during the powder metallurgical process.
1. **Die Pressing with Magnetic Field:** This method involves compacting magnetic powder in a die while applying a strong magnetic field. The field aligns the grains perpendicular or parallel to the pressing direction, depending on the material and field configuration.
2. **Injection Molding with Magnetic Field:** Here, magnetic powder is mixed with a binder and injected into a mold in the presence of a magnetic field. The field aligns the grains as the material solidifies. This is commonly used for complex shapes.
3. **Hot Pressing/Hot Deformation:** These processes involve compacting and deforming the magnetic material at elevated temperatures while applying a magnetic field. This can lead to even higher degrees of grain orientation.
4. **Sintering Techniques:** Controlling the sintering process is important. Sintering is the process of compacting and forming a solid mass of material by heat or pressure without melting it to the point of liquefaction.
## How Does Particle Size Distribution Affect Grain Alignment During Manufacturing?
The size distribution of the magnetic powder particles plays a vital role in achieving optimal grain alignment. A narrow particle size distribution tends to result in better alignment than a broad distribution. This is because smaller particles can rotate and align more easily with the applied magnetic field than larger particles. If you have a mix of both large and small particles, the larger particles can hinder the rotation of the smaller ones, leading to imperfect alignment.
To achieve a narrow particle size distribution, techniques like milling and sieving are used to carefully control the particle sizes before the alignment process.
* **Milling:** Reduces the size of magnetic materials.
* **Sieving:** Separates powder based on size.
## What Role Does the Applied Magnetic Field Strength Play in Achieving High Remanence?
The strength of the applied magnetic field used during manufacturing has a direct impact on the degree of grain orientation and, consequently, the remanence of the ring magnet. A stronger magnetic field provides a greater driving force for aligning the magnetic moments of the grains. However, there is a saturation point. Once the majority of the grains are aligned along the field direction, increasing the field strength further may not significantly improve the alignment or remanence.
* **Low Field:** Insufficient grain alignment, low remanence
* **Optimal Field:** Maximum grain alignment, high remanence
* **Excessive Field:** No significant improvement, potential for added cost and complexity
## How Does Temperature Affect Grain Orientation and Remanence in Ring Magnets?
Temperature profoundly influences grain orientation and remanence. At elevated temperatures, the thermal energy of the atoms and magnetic grains increases, causing them to vibrate more vigorously. This increase in thermal agitation can disrupt the alignment of the magnetic moments, thereby reducing remanence. The Curie temperature is the critical temperature above which a ferromagnetic material loses its ferromagnetism. It is crucial to keep the application temperature well below the Curie temperature of the magnetic material.
* **Low Temperatures:** Enhanced remanence, higher stability.
* **High Temperatures:** Reduced remanence, potential for demagnetization.
## Can Grain Orientation Be Measured? What Techniques Are Used?
Measuring grain orientation is crucial for quality control and optimizing manufacturing processes. Several techniques are used to characterize the texture and alignment of grains in magnetic materials:
1. **X-ray Diffraction (XRD):** This technique analyzes the diffraction patterns of X-rays to determine the crystallographic structure and preferred orientation of the grains. Pole figures, which show the distribution of crystallographic orientations, can be obtained from XRD data.
2. **Electron Backscatter Diffraction (EBSD):** EBSD is a scanning electron microscopy (SEM) technique that provides local crystallographic orientation information. EBSD can map the grain orientation distribution at high resolution.
3. **Magnetic Measurements:** Demagnetization curves and magnetic hysteresis loops can provide indirect information about grain orientation.
4. **Optical Microscopy:** Can visually show grains to some extent.
## What Materials Benefit Most from Optimized Grain Orientation in Ring Magnets?
Certain magnetic materials benefit more significantly from optimized grain orientation than others. Hard magnetic materials with high magnetocrystalline anisotropy, such as NdFeB and SmCo, exhibit the most dramatic improvements in remanence when their grains are aligned. These materials possess a strong preference for magnetization along a specific crystallographic direction; aligning the grains exploits this anisotropy to maximize their magnetic performance.
* **Neodymium Iron Boron (NdFeB):** Highest energy product, large improvement with grain alignment.
* **Samarium Cobalt (SmCo):** High temperature stability, significant improvement with grain alignment.
* **Ferrite:** Lower cost, moderate improvement with grain alignment.
## Practical Applications: How Does Grain Orientation Optimization Impact Real-World Devices?
Optimizing grain orientation has a profound impact on the performance of various real-world devices that utilize ring magnets.
* **Electric Motors:** Higher remanence translates to stronger magnetic fields, leading to increased motor torque and efficiency.
* **Generators:** Increased power output due to stronger magnetic fields.
* **Hard Disk Drives:** Higher data storage density due to the ability to create smaller and more stable magnetic domains.
* **Magnetic Resonance Imaging (MRI):** Stronger and more uniform magnetic fields are essential for high-resolution imaging.
**Case Study Example: Improving Motor Performance with Grain Oriented Ring Magnets:**
Consider a small electric motor used in a consumer appliance. By switching from an isotropic ring magnet to an anisotropic ring magnet with optimized grain alignment, the motor’s torque output can be increased by 20-30%. This improvement translates into a more powerful and efficient appliance. Furthermore, the improved efficiency allows for downsizing the motor, leading to a more compact and lighter product.
**Statistics and Facts**
* By improving grain orientation, remanence can increase by as much as 50% or more relative to an isotropic magnet of same material.
* Optimizing grain alignment can lead to motors that are both much more powerful and more compact in size.
## FAQ Section
**What exactly does “grain” mean in the context of magnets?**
In magnetic materials, “grain” refers to individual crystallites, or small, single-crystal regions, that make up the bulk material. Each grain possesses its own magnetic properties and crystalline orientation. When these grains are oriented in the same direction, the magnet’s total magnetic power is the cumulative effect of the grains aligned, and results in a more powerful magnetic field.
**Can any type of magnetic material have its grain orientation enhanced? Are there limitations?**
While the grain orientation of most magnetic materials can theoretically be influenced to some extent, certain materials, particularly those with high magnetocrystalline anisotropy (like NdFeB and SmCo), benefit the most dramatically from grain alignment. The effectiveness of grain orientation also depends on the manufacturing process and the ability to apply a sufficiently strong magnetic field during processing.
**Is grain orientation the *only* factor affecting remanence in ring magnets?**
No, grain orientation is a key factor, but other parameters also influence remanence. These include the chemical composition of the magnetic material, the density of the magnet, the presence of defects, and the operating temperature. Optimizing grain orientation is just one piece of the puzzle in achieving high-performance magnets.
**How does the shape of the ring magnet affect the importance of grain orientation?**
The shape can influence the effectiveness of grain orientation. For simple ring geometries, aligning the grains along the circumference is generally optimal. However, for more complex shapes, the ideal grain orientation may vary depending on the specific application and magnetic field requirements. Finite element analysis (FEA) can be used to model the magnetic field distribution and optimize the grain orientation for complex shapes.
**Is achieving perfect grain orientation (100% alignment) possible?**
In practice, achieving perfect grain orientation is extremely difficult and maybe near impossible. There’s always some degree of misalignment due to limitations in the manufacturing process. However, advancements in manufacturing technologies are constantly pushing the boundaries and enabling higher degrees of grain alignment.
**What are the trade-offs between grain orientation and other magnetic properties?**
While optimizing grain orientation typically enhances remanence, it can sometimes affect other magnetic properties, such as coercivity (resistance to demagnetization). For example, maximizing remanence might require a specific grain orientation that slightly reduces coercivity. The optimal trade-off depends on the specific application requirements.
## Conclusion: Understanding and Utilizing Grain Orientation for Optimal Ring Magnet Performance
Understanding and controlling grain orientation is paramount to maximizing the magnetic remanence and overall performance of ring magnets. By carefully selecting the appropriate magnetic material, optimizing manufacturing processes, and employing techniques to align the magnetic grains, we can unlock the full potential of these versatile components.
Here are the key takeaways:
* **Grain orientation** refers to the alignment of magnetic grains within a material.
* **Anisotropic magnets** with aligned grains exhibit higher remanence than **isotropic magnets** with randomly oriented grains.
* **Manufacturing techniques** like die pressing with a magnetic field, injection molding, and hot pressing enhance grain alignment.
* **Particle size distribution**, **applied magnetic field strength**, and **temperature** significantly impact grain orientation and remanence.
* **Grain orientation can be measured** using techniques like X-ray diffraction and electron backscatter diffraction.
* **Optimized grain orientation** leads to improved performance in electric motors, generators, hard drives, and MRI machines.
The Influence of Grain Orientation on the Magnetic Remanence of Ring Magnets
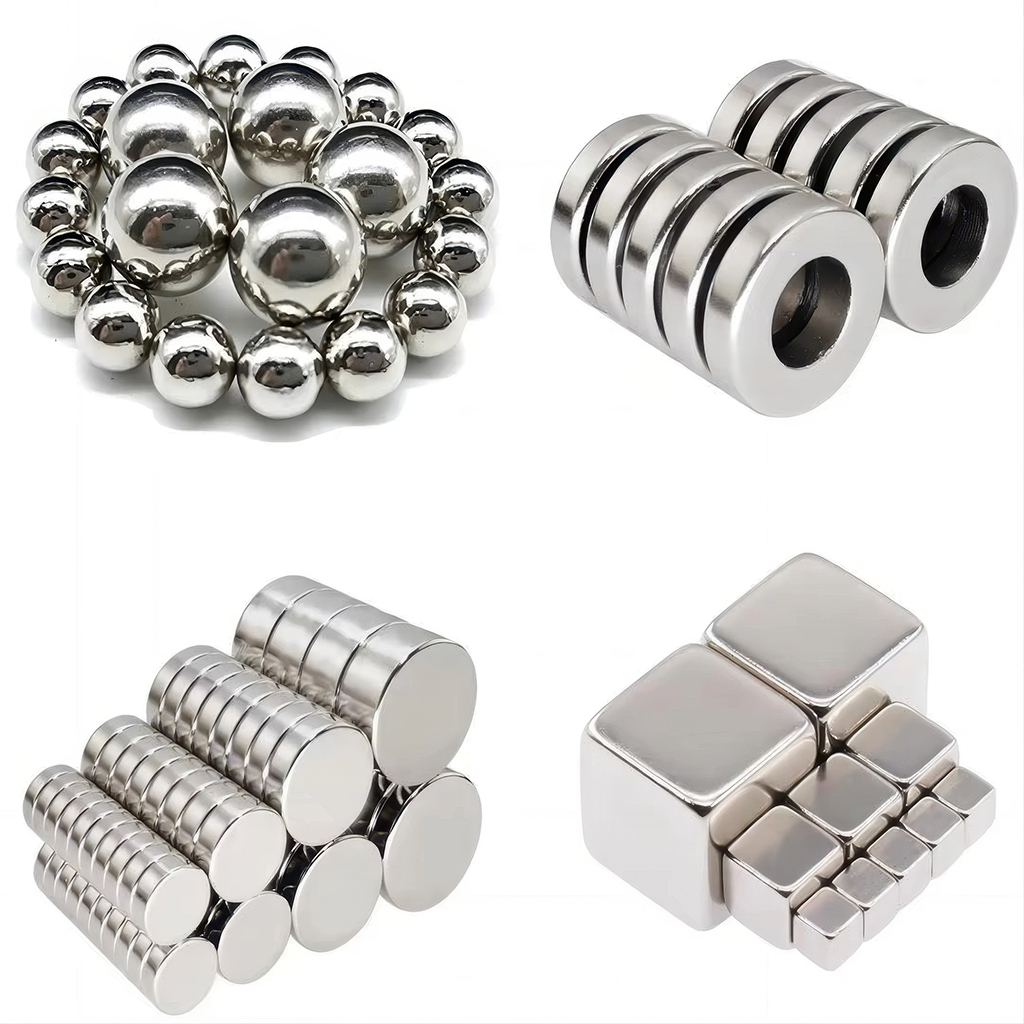